USB3, GigE, Camera Link and CXP explained. Here’s everything engineers need to know to choose the correct interface for machine vision automation.
TTI has sponsored this post.
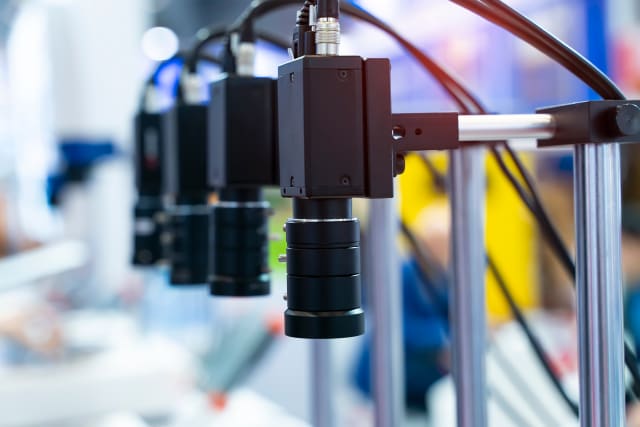
With what scholars are calling the Fourth Industrial Revolution upon us, manufacturing is steadily moving towards artificial intelligence (AI) to help make production lines more efficient and to better utilize human skill in a wide range of industries. In this shifting landscape with its expanding variety of applications, machine vision has emerged as a key force in driving productivity.
Employing systems of cameras to monitor manufacturing processes, machine vision is most immediately associated with reducing operator intervention and assuring quality control. But it can do much more. It can gather and report extremely accurate information against important operational metrics. It can isolate defective product, scan inventory, identify emergent events and carry out a quickly growing array of complex tasks that help increase throughput by cutting waste and reducing downtime while better tracking product quality. But as the need for real-time machine intervention increases, the required equipment must perform in ways that were not possible even a short time ago.
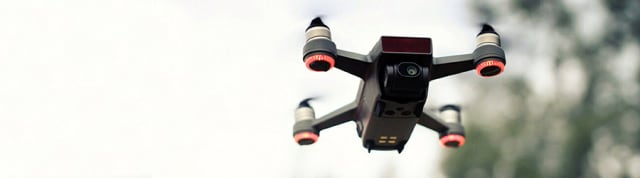
Interfaces for diverse applications
Standards for interfaces and interface hardware are key to successful machine vision. These standards express the confluence of bandwidth (resolution, frame rate, bit depth, etc.), data rate, signal speed and signal integrity to meet specific goals. They also dictate the types of connectivity equipment needed — cables, connectors, assemblies, connector shells, strain relief accessories and the like — which in turn must be balanced against local network capabilities as well as short- and long-term budget restrictions.
The opportunities are vast. But manufacturers must gain a deep understanding of their needs when considering machine vision automation. Optimal performance can be different for each manufacturer, portfolio offering, system and even production line. Considerations include:
Clarity: Especially with the advent of “smart” inspection platforms with multiple inspection metrics, remote data access and capabilities to monitor equipment effectiveness as well as the state of production, applications require sharp, clear real-time imaging to help provide brand-standard product quality. This can require high data volumes, and the bandwidth to transfer it quickly and completely.
Motion: Besides higher bandwidth, machine vision systems capturing real-time data from moving platforms will require durable cables that can withstand repeated motion. Systems using conveyors, where cameras must move in linear motion, require cables tested for repeated cycles on drag chain cable trays. For processes such as pick and place, robotic assemblies must often move cameras in random directions. Here, angled connectors can ease strain on cables and locking screws can help provide robust connections during vibration and short, random motions.
Distance: Many manufacturing lines require cable assemblies that can transmit data over longer distances without significant signal loss. Longer functional cable lengths can help reduce the need for additional cameras and equipment costs.
Automation level: Greater functionality requires more robust connections. Is the machine vision system required to simply capture and present images, enhancing operator decision- making? Or is an automated control unit making decisions based on data received, such as real-time triggering?
Speed/latency: Applications involving repetitive tasks — a chief source of inefficiency when performed without automation — can operate at high speeds. High signal speed and high data rates enable higher resolution and frame rates. Also, system latency must be low enough to keep pace with real-time processing.
Integration: As systems become more complex and one- of-a-kind — more cameras, smaller camera sizes, unique positioning and more — interfaces that connect to standard PC architectures and/or do not require additional hardware can be critical to helping lower overall system costs. Compatibility with long-established standards is also a plus as manufacturers often choose to alter or expand based on what they can already easily manage and troubleshoot.
An overview of machine vision interfaces
Established or quickly-emerging interface standards shaping the direction of machine vision are USB3 Vision®, Camera Link® , and CoaXPress® (CXP), along with GigE Vision®, an industrial camera standard for data transfer over Gigabit Ethernet protocols.
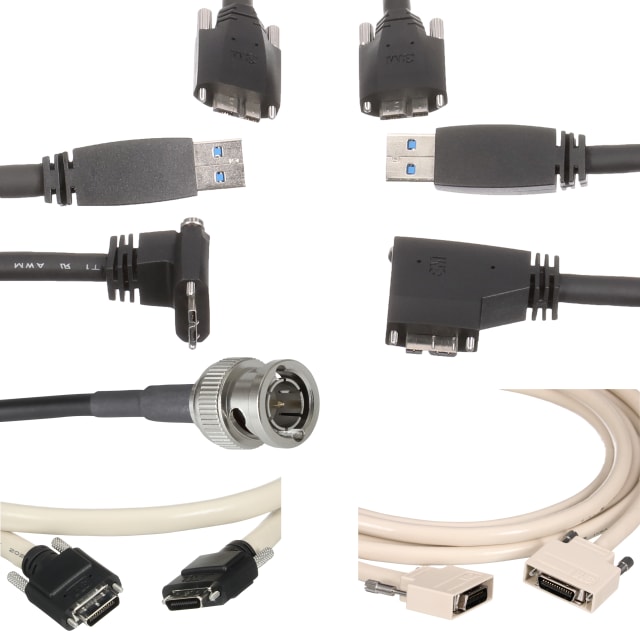
USB3 Vision®
USB3 Vision is fast-growing and very popular for its compatibility and ease of integration. It accommodates high speed, high resolution data at a relatively low system cost, and allows for multi-camera configurations.
Its limitations in transmission distance often pose barriers. But recent 3M USB3 cable assemblies can deliver transmission distance up to >10 meters (greater than 14 meters depending on cable type and equipment), far beyond standard requirements for USB3 Vision cable solutions.
GigE Vision®
GigE Vision stands out for its ease of system integration. Cable lengths can exceed 32 feet and equipment is compatible with many different networks. Originally created to provide a framework for transmitting video and other control data over gigabit Ethernet networks, GigE Vision has become an easy way to connect multiple cameras at low cost. However, as it relies on the often limited bandwidth of local networks, it can have latency issues which can critically affect tasks that require high speed, real-time precision.
Camera Link
Introduced in 2000, Camera Link was the first interface built specifically for machine vision applications. With the ability to transmit high speed, high resolution data, it is excellent for applications such as line scan cameras where real-time data and low delay is required. Functional cable length can be quite short (less than 5 meters) making it very difficult to apply to mobile platforms. Also, it can be significantly higher priced when specified for systems requiring high volume data capability.
CoaXPress®
CoaXPress, or CXP, is expected to become the mainstream interface for high speed and high resolution camera systems. With the recently released CoaXPress 2.0, it can provide transmission speed up to 12.5 Gbps/channel — high throughput for real-time applications and harsh industrial environments. CXP is excellent for multiple-camera systems, but it requires relatively complex support equipment and can result in higher overall expense.
With the latest cable assemblies providing functional cable length greater than 13 meters (CXP6) and greater than 10 meters (CXP12) for flex durable and thinner diameter (less than 5 mm O.D.) cable, CoaXPress is excellent for achieving longer transmission distance in larger systems.
Choosing the correct interface for machine vision automation
This table helps match manufacturing needs with available machine vision interfaces. Further refinements can be made based on local networks, physical space and desired level of automation.

*10 meter functional cable length is available from 3M™ USB3 Vision Industrial Camera Cable Assembly, 1U30E Series. Performance of up to >14 meters can be achieved depending on the equipment used with the cable assembly.
As a global supplier of cable assemblies and related equipment in the world’s leading machine vision standards, 3M can help specify interface solutions to help you maximize your manufacturing capabilities — and beyond. Our variety of well-proven Camera Link interconnect solutions is based our extensive knowledge and experience as one of the originators of the CL standard decades ago.
We continually introduce new solutions for USB3 Vision® and CoaXPress®, helping enable cable flex, transmission distance and design configurations not previously possible in manufacturing. At the same time, we’re exploring the possibilities of implementing machine vision standards for additional innovations in areas such as electronic devices. 3M experts are available for your unique requirements.
To learn more visit TTI and 3M.