For a sky full of flying cars to become reality, they'll have to lighten up. Smart selection of cables and connectors will play a big role.
When it comes to getting from one place to another, current modes of transportation cover almost all environments, whether by land, sea, or air. Despite these vectors being conquered, numerous emerging technologies provide new options. One such method of transportation takes its inspiration from quadcopter drone technologies, which show extraordinary amounts of freedom, safety, and potential for automation.
Electric vertical takeoff and landing vehicles, or eVTOLs, can fly like common commercial drones, taking off and landing without requiring long airstrips. While drones typically have blades affixed to motors pointing directly upward, more modern eVTOLs can take advantage of movable engines that allow for more forward thrust, thereby improving efficiency. Cables and connectors play a surprisingly important role in the viability of eVTOLs and their impact on overall mass. Knowing how the right connectors and cables will aid in design can help engineers create viable and sustainable eVTOLs.
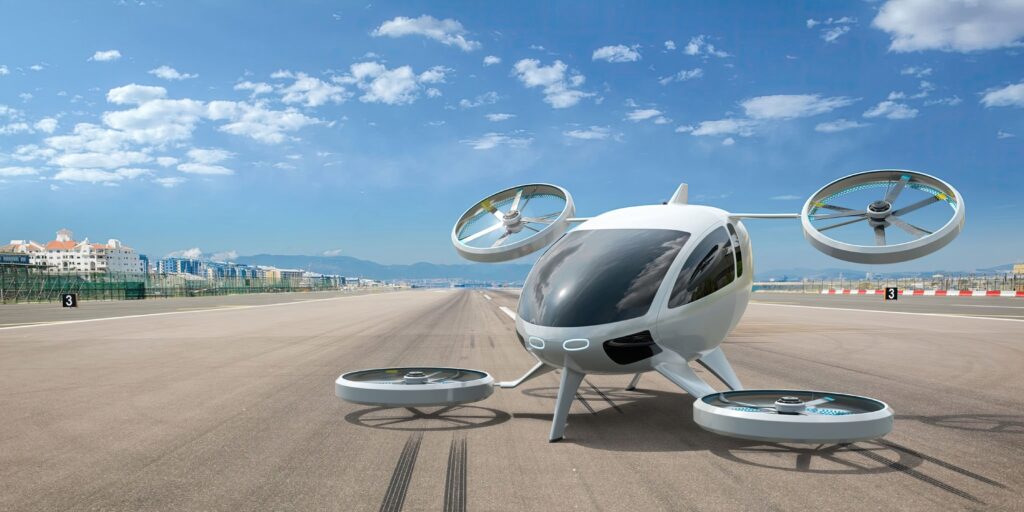
Compared to helicopters, which are notoriously difficult to pilot, such vehicles are far easier to manage due to simplified controls. Additionally, the vast amount of software and hardware already developed to create autonomous drones means that eVTOLs are ripe for deploying autonomous flight systems, thus eliminating pilot error.
Most airspace above urban zones is virtually unused, so eVTOLs could move around at high speed, significantly reducing transportation times between locations. Thus, eVTOLs could ferry people and cargo within urban environments, reducing road dependency and making highways more ideal for transporting heavy goods.
Bridges and tunnels can increase road and rail traffic capacity, but the massive infrastructure cost makes such projects hard to justify. eVTOLs would merely need landing pads and charging stations. This not only reduces costs for taxpayers but also lowers maintenance expenses, as roads will experience less traffic if pedestrians use eVTOLs.
While they offer many benefits, eVTOLs face many design challenges if they are to become an effective mode of transportation. In this article, we’ll discuss these challenges while focusing on the interconnect design and its importance in the development of efficient and effective eVTOLs.
What challenges do eVTOLs face?
Despite all the advantages that eVTOLs present, they are still more of a concept than an actual solution that can be deployed in a commercial environment, and this reality comes down to numerous challenges that they face.
The first, and arguably the most critical factor, is weight. Because eVTOLs are entirely electric, they must carry hefty batteries. Compared to fossil fuels, batteries have far less energy density, meaning that any battery is far heavier than a tank of gasoline with the same energy capacity. For comparison, the energy density of gasoline is 47.5MJ/kg compared to lithium-ion batteries at 0.3MJ/kg.
Due to the need for heavy batteries, the rest of an eVTOL needs to be as light as possible. While modern materials such as carbon fiber can achieve this, they come at an added price and design complexity.
If eVTOLs become autonomous, communication between each eVTOL will be essential due to the severity of possible collisions. eVTOLs will need to be able to see the flight path of all other vehicles and plot a safe route accordingly. Such a network would need to handle vast amounts of data in real time with significantly reduced latency. According to researchers at KAUST, latencies down to 10 ms will be needed for autonomous flight control.
At a minimum, an eVTOL network would need to work on top of a 5G network, utilizing edge computing to have data immediately routed to other vehicles (i.e., not pass through ISPs). However, integrating cellular communication systems and onboard artificial intelligence for autonomous flight introduces additional systems and components, further increasing weight and reducing the energy available to the craft for flight. Energy efficiency is of paramount importance, and designers must reduce the weight of any and every component. Depending on the size of the craft, electronics can account for 20% or more of the total weight.
How do connectors and cables come into the picture?
Cables and connectors may not seem as critical as other components in the design of eVTOLs, but their importance is quickly realized when exploring each aspect.
Connecting and powering the various eVTOL systems requires long cabling lengths, sometimes adding up to miles, which can account for a significant portion of the aircraft’s total weight. Power cables alone can account for close to 1% of the total weight of a 5,000-lb. craft. The signal and data cables further increase this number. Power cable weight is seen as such a significant weight contributor that aerospace engineers at NASA have studied how the design of power cables can be optimized to minimize weight.
Since eVTOLs are entirely based on electricity, electrical stress can be extremely high, with high voltages and currents present. This means that any cable and connector used to deliver power from the batteries to the motors needs to handle such power levels safely and have sufficient insulation to provide adequate protection, which tends to lead to large, bulky cables. Ensuring the optimal conductor and insulation materials can help limit power cables’ impact on overall weight. Many engineers designing eVTOLs opt for solutions commonly found in aviation platforms, including aluminum cables that are designed with these concerns in mind.
Whether high voltage or current is chosen, the final cable and connector choice must reduce weight as much as possible. Any extra weight in an eVTOL will increase the difficulty of takeoff and limit its range.
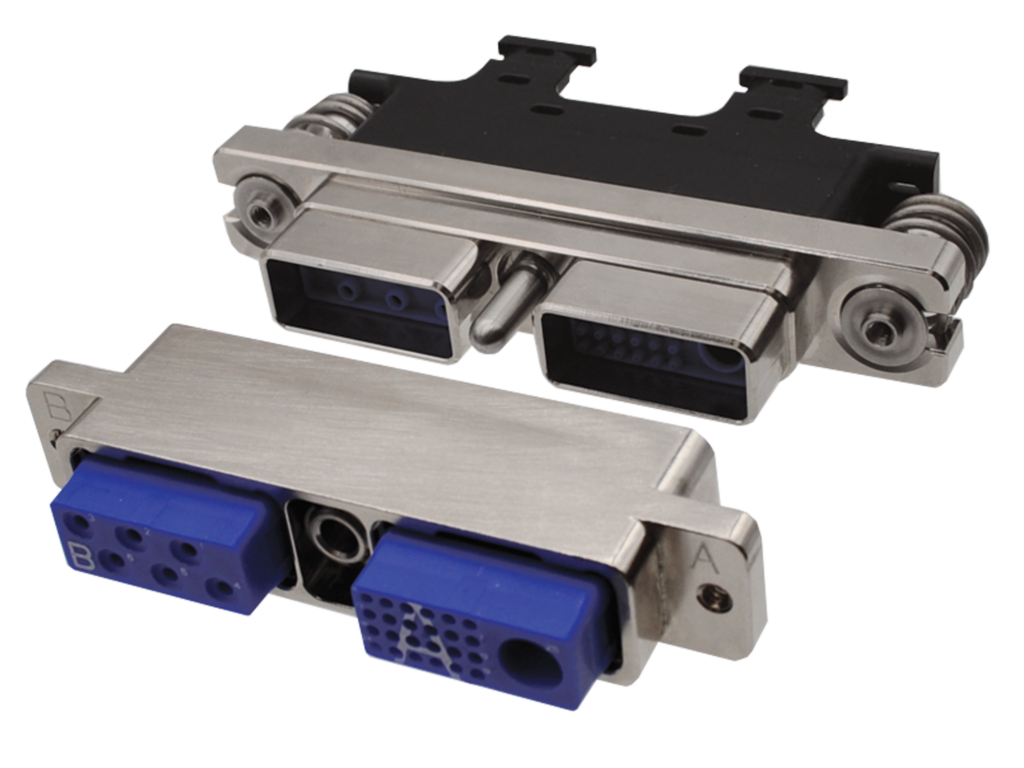
Such connectors must operate safely in extended temperature ranges while retaining a high IP rating to prevent damage during poor weather conditions. Consider, for example, the connectors found in the landing gear, rotary motors, antenna systems for GPS and radar for eVTOLS. Most of these systems have some or much exposure to the environment. When landing in cities such as Dubai these connections may face weather conditions that include sandstorms, extreme temperature changes, sudden torrential rain, and high winds.
Finally, as all these connectors and cables are being used in an environment subjected to shock and vibration generated by motors and landing/takeoff, any connector used must resist accidental disconnects over extended use. As such, simple screw terminals or clips will likely be insufficient, requiring locking nuts, press-fit connections and unique mating mechanisms.
How can RF connectors help power the future of eVTOLs?
A wide range of compact RF connector styles and mounting options is available to satisfy the various RF needs of an EVTOL. This includes connectors down to 1.0 mm, which can operate at frequencies up to 110GHz. This makes them ideal for all aviation tracking systems, including ADS-B and Pilot Aware. They can also be used with cellular systems, including 4G, 5G, and mmWave bands of 5G.
For designs that require communication speeds beyond copper’s capabilities, a range of optical connectors can help engineers achieve extremely high inter-device speeds across the entire eVTOL and do so at significantly reduced weight due to the use of tiny fiber-option cables. Such cables are also immune to electromagnetic interference, making them far safer for use in autonomous environments where sensor data cannot be compromised.
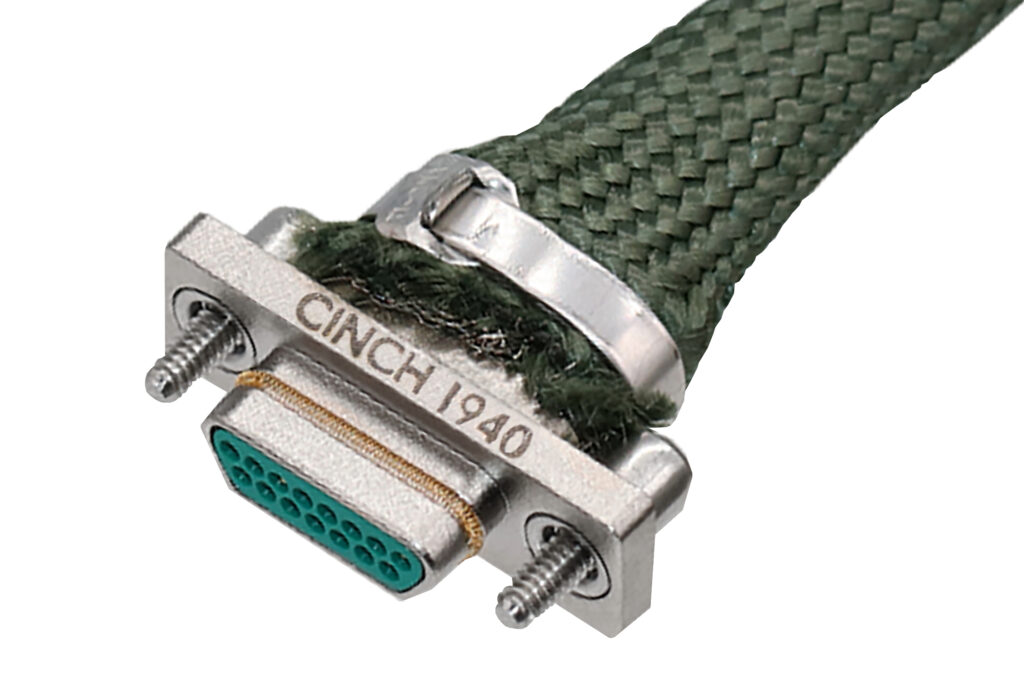
Not all connectors can be replaced with RF or fiber optics. For such applications, micro-D connectors become invaluable. Their design allows for either shielded or unshielded cables to be used. In cases where EMI is not a concern, the absence of shielding can help reduce size, weight, and cost. Their specific D shape also makes them polarized. Compared to standard D-sub connectors, micro-D connectors are significantly lighter and take up to 80% less space while offering the same performance in the harshest environments.
Conclusion
While there is a lot of hype surrounding eVTOLs, they are still in their infancy, and any existing systems are more of a concept than an actual viable design that could be supported economically. The extreme technical challenges faced by eVTOLs and endless amounts of legislation present numerous roadblocks to engineers when trying to get such ideas to take off. However, the industry has growing confidence that the necessary infrastructure can be built and that technological roadblocks, such as battery density, will be overcome.