Both 2D and 3D printing can produce capacitors and other electronic components—here’s how it works.
This article is part of The engineer’s complete guide to capacitors. If you’re unsure of what type of capacitor is best for your circuit, read How to choose the right capacitor for any application.
What is a printed capacitor?
Capacitors can be printed both with inkjet (2D) printing as well as 3D printing. Inkjet printing can be used to fabricate complete, functional electronics circuits, and can accommodate material classes such as metals, ceramics, polymers and carbon nanotubes. Multiple layers can be printed, which means parallel plate capacitors can be printed.
Inkjet printing can accommodate passive devices like resistors, inductors and capacitors as well as active devices like field effect transistors. This fabrication technique lends itself to fabrication on various surfaces (such as glass and flexible surfaces for wearable electronics). For example, inkjet printing is used to fabricate antennas on automobile front windows and electric heaters for defrosting automobile rear windows.
Printable inks can be divided into three main categories: conductors, dielectric materials and semiconductors. Deposition methods for patterning components to provide structures with the desired thickness and inkjet resolution are controlled tightly. Various techniques are used and require the proper tuning of the set of different ink parameters like viscosity, conductivity, surface tension and compatibility of the solvents with the underlying materials.
Capacitors are produced by depositing a conductor (such as silver), covering it with a dielectric ink (such as organic polymers or ceramics) and then applying another conductor layer. Other oft-used conductors include gold, copper, platinum and nickel. Multiple layers can be printed.
Inkjet printed electronics are used to produce radio frequency identification (RFID) tags and find applications in consumer electronics, the automotive industry, smart packaging and buildings, healthcare and the Internet of Things (IoT).
How to 3D print a capacitor
Using a 3D printer, capacitors like polycarbonate, polypropylene and more can be produced. Discrete capacitors can be fabricated as either through-hole or surface-mount devices.
While printed capacitors would seem to indicate just another packaging scheme, the technology provides much more than that. First, because components are fabricated in house, supply chain considerations are less significant. Second, intellectual property is more secure since design data does not need to be transmitted to vendors. Third, the printed components can have tailored form factors to save PCB real estate. Fourth, the electrical performance (operation) of 3D printed capacitors is comparable to traditional discrete devices.
One common (relatively inexpensive) method of fabricating 3D printed capacitors is fused deposition modeling (FDM, also known as fused filament fabrication, FFF). Filament materials are fed into an FDM 3D printer and include ABS (acrylonitrile butadiene styrene) plastic (a common thermoplastic polymer), PLA polymer plastic, nylon, HDPE (high density polyethylene, a thermoplastic made from petroleum), wood filaments, metal filaments and an electrically conductive form of carbon known as graphene. Graphene can be used as a conductor, semiconductor or insulator.
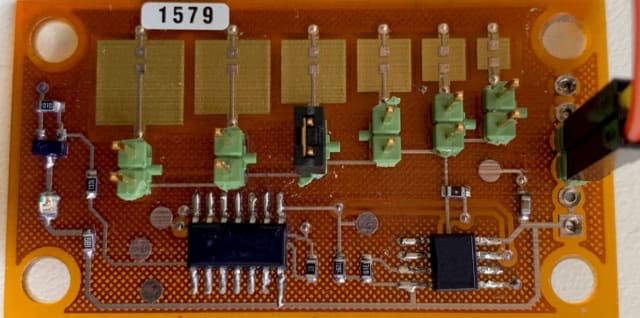
An example of a PCB using 3D printed capacitors is shown above. Produced by Nano Dimension in 2019, 6 capacitors appear across the top of the assembly. Since capacitance is directly proportional to plate area, the capacitor with the largest capacitance is on the left and the capacitor with the smallest capacitance on the right. The PCB and the capacitors were produced using FDM 3D printing. The integrated circuits, SMD resistors and other components were attached using soldered connections.