Changing to 48-volt vehicle architecture is inevitable, according to automotive Tier 1.
TTI has sponsored this post.
Ever since internal combustion engines dominated the automotive industry, vehicles have been mechanical systems — with electrical add-ons here and there. This perception is changing with the rise of electric powered vehicles and features. Consequently, the engineers tasked with making this shift a reality must overcome a challenge: modern 12-volt electrical systems can’t keep up.
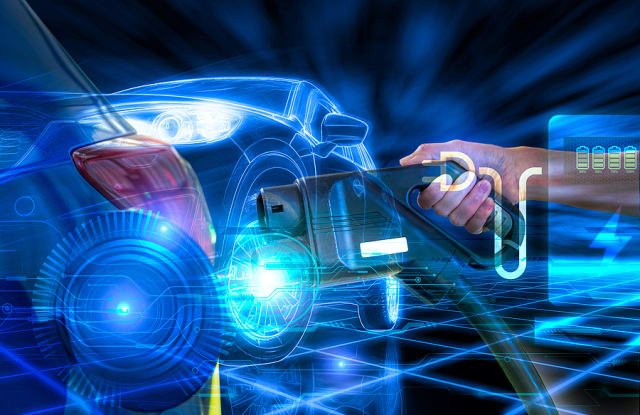
Go back far enough and engineers only needed a six-volt battery to run headlights, turn signals and other essential features. But as more electrical systems (such as power windows, locks and stereos) became standard, the six-volt system could no longer keep everything running. As a result, the industry switched to a 12-volt standard in the 1950’s.
Modern day vehicles are mirroring this history. Engineers designing vehicles — be it cars, snowmobiles, electric scooters, jet skis and even forklifts — must now consider numerous complex, power-hungry systems and features. In automotive, for example, advanced driver assistance systems (ADAS), autonomous driving systems, sensors, infotainment modules and on-board computers are becoming standard. These electronics put too much strain on a 12-volt battery — thus 48-volt batteries are predicted to become the new standard architecture in transportation. To help smooth this transition towards a 48-volt future, Molex offers its MX-150 mid-voltage interconnect technologies.
The shift to 48-volts is inevitable
Ironically, the transfer to 48-volt systems is stymied by the sheer number of electronics within modern vehicles. According to Kirk Ulery, distribution business development manager at Molex, though the need to move to 48-volts is apparent, most standard parts available to automotive manufacturers are designed for 12-volt architectures. This makes it expensive and complex to jump to 48-volt systems.
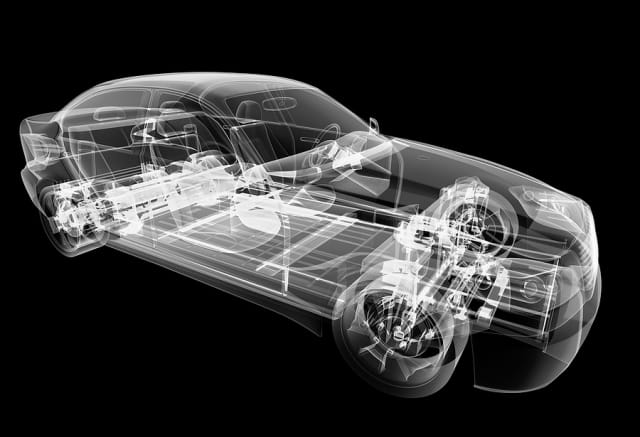
Nonetheless, Ulery sees the writing on the wall. “We’re getting to a point where the wire size must increase in a 12-volt system to handle the amount of power you need for all the new features. That’s where the 48-volt system comes in. It goes back to Ohm’s law. When you increase your voltage by a factor of four, you increase the power by a factor of four. So, you have four times the wattage to power these devices.”
We can see the shift to 48-volts today with electric and mild-hybrid vehicles. In mild hybrids, the vehicle will stop the internal combustion engine and run on electrical power when able. It will then start the engine as required. Meanwhile, fully electric vehicles run completely on electrical motors.
“The common thing is that they are moving traditional mechanical functions off a serpentine belt to a series of electric motors,” points out Ulery. He gives an example of a heavy-duty pickup truck using mechanical energy for its power steering. In many vehicles this function is becoming electrified. “The amount of time you need the power steering was robbing some of the engine’s horsepower. By moving it to a separate electrical system, you can control that and maintain more power through the drivetrain … It makes a significant difference in the amount of power you have for the vehicle.”
This demonstrates how even heavy-duty applications are becoming electric in mechanical vehicle systems, and how much the number of power-hungry systems operating electrically is increasing. As a result, 12-volt batteries will not be able to handle the increased load. Therefore, the shift to 48-volt architectures is less a question of if, and more a question of when.
The benefits and challenges of transitioning vehicles to 48-volts
For engineers, one of the primary benefits of 48-volt architecture is its ability to operate at similar wattages using smaller gauge wires. In other words, the larger the voltage, the lower the current needs to be to maintain the power. Thus, smaller, lighter and less expensive wiring harnesses can be used to improve a vehicle’s range, price and ecological footprint.
Ulery sees this as a primary incentive for the change. “The current drive to 48-volts has to do with smaller wires. They cost less, weigh less and are easier to maneuver [around other internal systems under the hood] … Generally, smaller wires with the same amount of wattage [produce] a significant reduction in weight and costs.”
The higher voltage also creates the ability to design a wiring harness with lower resistive losses. “There are some requirements you have to look at when you get to smaller wires. They tend to have slightly higher resistance,” says Ulery. “When you design a wiring harness you know the bulk resistance. [It] is a significant factor in determining the size of the wires.” This means engineers can optimize the wire harness for weight and resistance loss by adjusting the size of the wires. Generally, 48-volt systems can result in a lighter harness that also has lower resistance losses when compared to 12-guage architectures.
Like weight, temperature is another limiting factor when designing the wiring harness of a vehicle. Electric and hybrid vehicles need to stay cool, as heat increases the rate of mechanical deterioration and can cause catastrophic battery failure. Since the shift towards a 48-volt architecture can result in a wiring harness with lower resistive losses, it will also lose less energy to heat. As a result, the higher voltage could translate into a vehicle that operates at a lower temperature.
“Temperature is an issue we calculate for whenever we’re designing automotive wiring,” Ulery explains. “We typically use a current rating that’s based on a specific temperature rise when fully energized.” He adds that a fully energized system is an extreme case, and the calculation would result in an over-engineered wire — which would produce a cooler vehicle anyway. He says, “the duty cycles are such that temperature rise is not usually an issue.”
So why not take the plunge and shift to 48-volts now? Costs, part availability and legacy systems within the automotive industry makes the transition difficult. “It’s a challenge to find components that work with 48-volts,” says Ulery. He then used the Tesla Cybertruck as an example. Though the new vehicle is primarily a 48-volt architecture, the company stepped down voltages in some locations to ensure available parts were compatible.
“No vehicle OEM builds everything,” says Ulery. “The only thing they tend to make are the engines and body panels. Everything else in the car is purchased. Back-up sensors, digital cameras, radios are all purchased. So, to change the industry will take time as suppliers need to change parts to the 48-volt architecture.”
In other words, shifting to 48-volts too soon comes with part availability, compatibility and format adoption risks. In addition, the manufacturer would need to increase development costs to design parts that work at the new voltage. So, much like the Cybertruck, as more vehicles move to 48-volts, many of their sub-systems will likely still operate at 12-volts.
MX-150 mid-voltage connector provides new options for transportation
One part that is widely available for 48-volt automotive and transportation applications are the MX-150 mid-voltage connector provided by Molex. This connector is an expansion of the MX-150 product line which is standard to the automotive industry. So, selecting this connector helps to minimize format adoption and compatibility risks.
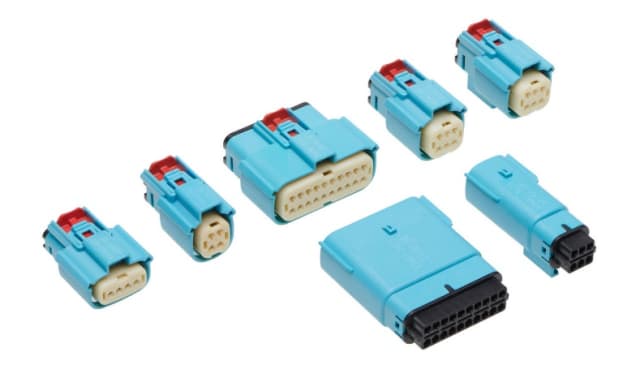
“MX-150 is one of the largest global Molex product lines,” says Ulery. “With the mid-voltage [version], we have it certified up to 60-volts. We made some slight changes to our housing to make sure that we meet all IEC requirements for creepage and clearance. … So, customers are assured that when they use it for 48-volts, or even 60-volts, that the connectors will pass any type of regulatory requirements that they might be subjected to.”
In fact, the connector is already in use for 48-volt applications. And since it’s compatible with legacy MX-150 connectors, customers shifting to a 48-volt architecture spent less time and money on engineering. For example, the connector position assurance (CPA) key ensures all connections are properly mated and safe from accidental disconnections. So, the engineering to connect legacy MX-150 connectors is already done.
“You can both feel and hear the latch click,” says Ulery. “Then the CPA slides under the latch to make sure that it cannot come apart unless you physically move the key. If anyone’s ever tried to do work on even simple electronics on a vehicle, you learn very quickly how hard these things are to get apart.”
MX-150 mid-voltage connectors also have applications for other vehicles. “We’re seeing so much electrification today,” says Ulery. “Electric bicycles, scooters, even electric snowmobiles, personal watercraft and marine applications. Every one of those that’s set up to be fully electrified can benefit from a 48-volt system.”
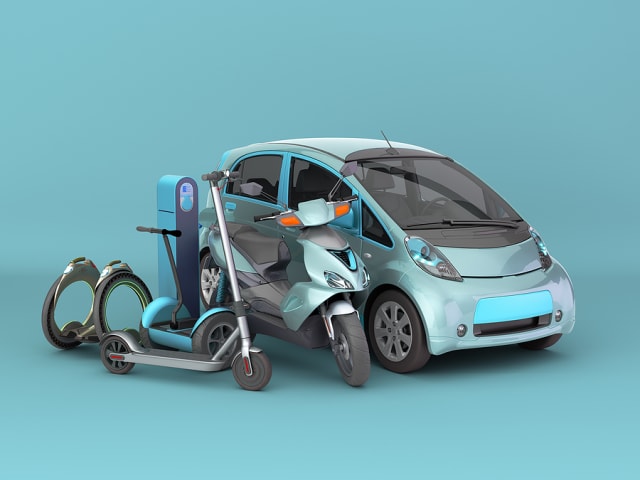
Engineers testing parts in physical prototypes running on 48-volts must still overcome one hurdle: sourcing the parts to test. Vehicle parts tend to be available in bulk to reduce their costs for manufacturers. In other words, getting access to a few dozen connectors for the sake of testing can be difficult.
Ulery says for Molex customers this problem is solved by their partner TTI. “TTI has our reliable interconnect technologies in stock, and local contacts so [customers] can call immediately and get the parts they need. I work closely with TTI to get them to understand where connectors can be used and the value proposition to add them into designs. They have the engineering expertise to help [TTI and Molex] customers get their products out faster.”
To get access to MX-150 mid-voltage connectors and other Molex connectors via TTI, visit Molex at TTI.