Learn the difference between shunt, open-loop, close-loop and flux gate current sensors for battery management systems and motor control.
TTI has sponsored this article.
Electrification has a profound impact on a wide range of industries. In the past, current sensing technology was mainly used in industrial sectors, but with the introduction of the Paris agreement and the push to pursue clean energy along with the launch of rechargeable lithium-ion batteries, there are now many applications expanding current sensor use. In addition, this movement has created the need to move to a much higher range of current than ever before. Lithium-ion batteries used in automotive applications have a very high energy density; therefore, the need for high power current sensors has become paramount.
Here’s what engineers need to know about current sensor technology and how to use it in electric vehicles.
What are current sensors and where are they used?
As platforms become more electrified, current sensing is required in applications such as power conversion, battery charging in electrical vehicles, and industrial equipment and processes. To monitor electrical current flow and measurements in applications, high power current sensors can help satisfy the needs.
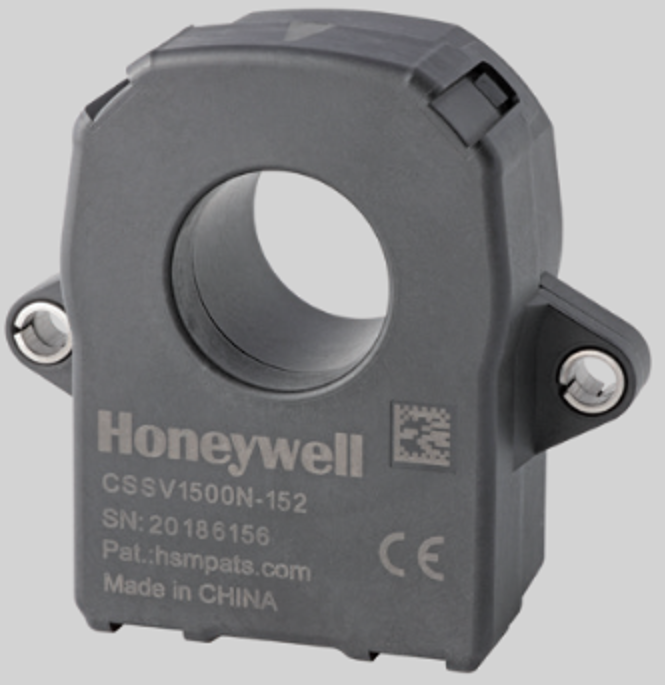
Current sensors are designed to detect and measure the current passing through a wire or conductor. They generate a signal that is proportional to the current, which can take the form of analog voltage, current, or a digital output.
This output signal serves various purposes:
- It can display the measured current
- It can be stored for further analysis in a data acquisition system
- It can be used for control purposes to limit or stop the flow of current
Current sensors play a critical role in maintaining the safety of battery systems. In modern battery systems, they monitor two key parameters of the battery: state of charge (SoC) and state of health (SoH). To do so, they must accurately track the power consumption of electric vehicles and estimate the remaining charge in the battery.
Current sensors are designed to measure current. Shunt sensors, for example, use Ohm’s law and manipulate Ohm’s law depending on what factor is being solved. For example, if voltage is being calculated, then Ohm’s law can be rewritten as V= I*R.
Types of current sensors
There are different current sensor technologies: Shunt current sensors (or direct in-line), open-loop current sensors, close-loop current sensors and flux gate current sensors. Each has certain advantages and disadvantages.
In a shunt current sensor, a precisely calibrated shunt resistor is placed in series with the load (the part of the circuit where current needs to be measured). As the current flows through the shunt resistor (often referred to as the bus bar), a specific resistance value can be obtained along with an accompanying voltage. The resultant current can then be accurately calculated. Shunt current sensors contain a conductive copper alloy bar that is placed in series with the current source to be measured.
Shunt sensors have some advantages. They are very robust, and are also typically lower in cost due to a very simplified design. However, they also have several distinct disadvantages: excessive heat, zero off-set, poor accuracy, required compensation, susceptibility to corrosion, and creepage. Some end users prefer shunt-based solutions for low-current (50 amp) measurements. However, due to the increasing needs of current measurement range and accuracy requirements, EV suppliers are migrating away from shunt-based current sensors and changing to magnetic flux-based current sensors, especially in high-current environments above ±500 amps to ±1500 amps and beyond to further improve measurement accuracy.
Honeywell offers a variety of magnetic-based current sensors with different configurations to satisfy customers’ high current application needs and requirements. These sensors fall into three types: Open-loop Hall-effect current sensors, close-loop Hall-effect current sensors, and flux gate and advanced flux gate current sensors.
The open-loop Hall-Effect current sensor comprises a few key components: a Hall element, ferromagnetic magnetic core and an amplifier. Functioning as a transducer, the Hall element detects the presence and intensity of a magnetic field, generating a voltage value aligned with the current in the targeted conductor.
Open-loop current sensors have both benefits and drawbacks. On the positive, they offer a simpler design, reduced cost compared to closed-loop Hall technology and a notable advantage in response time. These features make them particularly suitable for applications in motor control. Additionally, open-loop current sensors exhibit higher current measurement capability and are well-suited for operation in a wide temperature range. Even though open-loop sensors can be very accurate, they are not as accurate as a closed-loop Hall-effect design. Also, if the internal circuitry is not designed correctly, temperature drifts can pose a challenge.
Open-Loop Hall-effect current sensors offer low cost, simpler design, compact size, light weight, high bandwidth and fast response time.
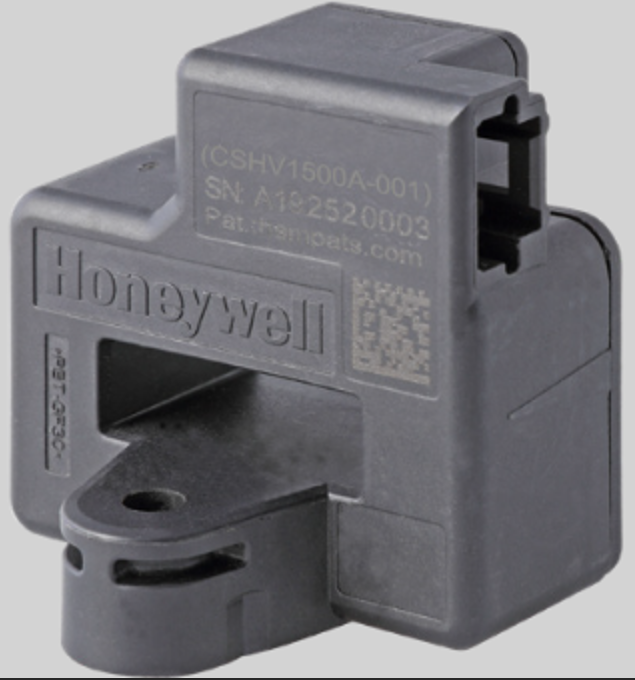
The closed-loop Hall-effect current sensor is designed with several key components: a ferromagnetic magnetic core, a Hall-effect sensor, a secondary conductor and a feedback amplifier. The magnetic core concentrates the magnetic field. As primary current (IP) flows through the core’s conductor wire, it generates and concentrates a magnetic field within the core. The Hall-effect sensor detects this magnetic field, producing a proportional voltage corresponding to the primary current. Subsequently, the feedback amplifier amplifies this voltage and directs it back to the secondary coil, generating a magnetic field in the opposite direction.
Closed-loop current sensors can be designed to measure ac and dc currents and offer high accuracy and low temperature drift.
Closed-loop current sensors offer high accuracy, high sensitivity and linearity, lower offset error, temperature stability and immunity to magnetic field drift.
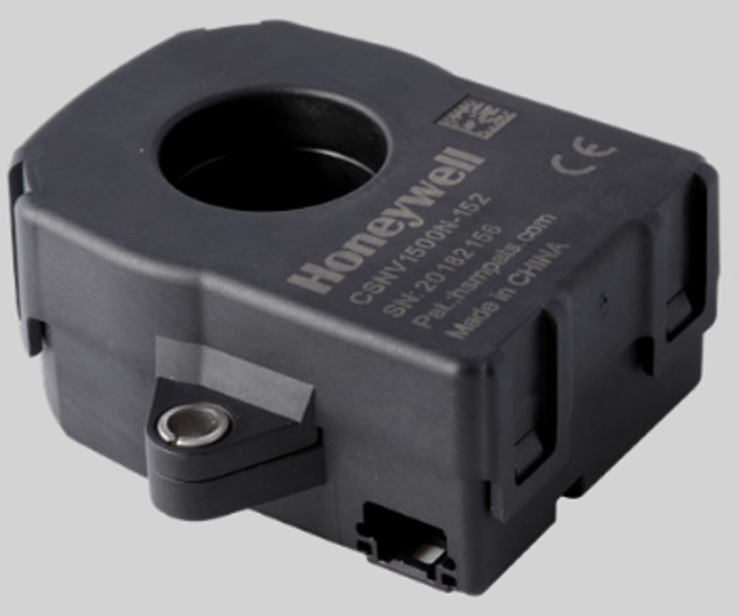
Flux gate current sensors operate in a similar manner as Hall-effect based closed-loop current sensors. However, the sensing technology used to monitor the magnetic field in the sensor’s magnetic core is different. In the case of a Flux gate sensor, the primary conductor carrying the current to be measured passes through the center of a magnetic core loop. The current flow in the conductor tends to generate a magnetic flux in the core.
Flux gate current sensors are versatile, accurate, and have excellent linearity and wide frequency response. These sensors are used in a wide range of applications, including electric vehicles, EV charging stations, renewable energy systems, power and industrial automation.
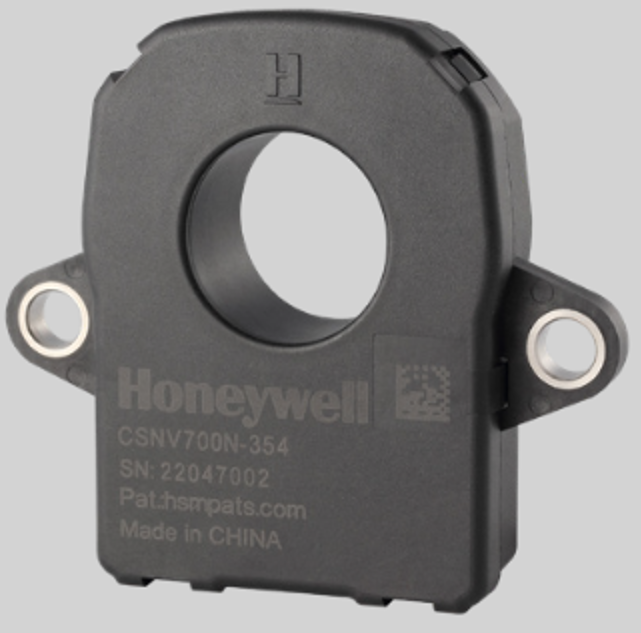
Current sensors in EVs
In electric vehicle applications, a battery management system (BMS) is a crucial and sophisticated subsystem designed to monitor, control and optimize the performance of the rechargeable batteries within the vehicle’s battery pack. The BMS continuously monitors various parameters and the health of batteries within the battery pack. This includes parameters such as voltage, current and temperature. Real-time monitoring with a current sensor allows the BMS to detect any abnormalities or deviations which stray away from optimal operating conditions.
Current sensors also play a pivotal role in motor control applications. They facilitate real-time monitoring of the current flow through the motor. They also provide robust protection for the motor and prevent potential damage caused by excessive current flowing into the motor’s windings. These sensors can initiate protective measures such as motor shutdown or alarm activation when the current exceeds predefined thresholds.
Honeywell offers an extensive portfolio of advanced current sensors. Through continuous innovation and refinement, Honeywell develops new products that offer differentiation from our competition. To learn more, visit Honeywell at TTI.