Study finds that dependence on robots may lead to more errors, especially over time.
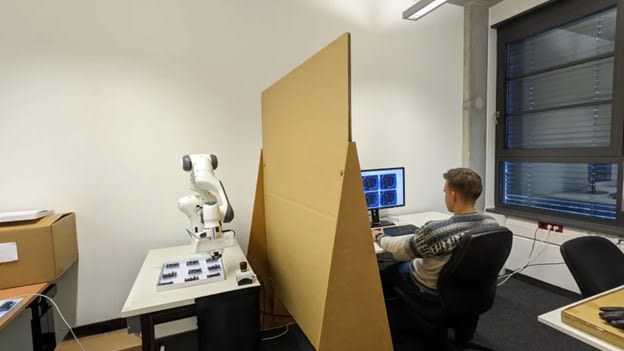
People appear to put in less effort when they are told robots are helping them with a task, according to an October 2023 study by researchers at the Technical University of Berlin. The research reveals dependence on robots may lead to more errors, especially over time.
The study involved examining the results of 42 German students performing a task to look for manufacturing defects on circuit boards. The first group reviewed the boards alone. The second group reviewed boards that they were told had already been inspected by a robot. The second group could not see or hear the robot. They were told the robot left red marks near potential defects. The first group found an average of 4.2 out of 5 defects, while the second group found an average of 3.3 out of 5 defects.
The reduced effort is likely to have a direct effect on the detection of circuit-board defects, shares Dietlind Helene Cymek, the first named author of the study. The finding that humans attempt to engage in “social loafing” with robots indicates that human-robot teams could be less efficient than engineers’ estimations.
The concern could have safety implications, says Dr. Linda Onnasch, senior author of the study.
“In our experiment, the subjects worked on the task for about 90 minutes. We already found that fewer quality errors were detected when they worked in a team. In longer shifts, when tasks are routine and the working environment offers little performance monitoring and feedback, the loss of motivation tends to be much greater. In manufacturing in general, but especially in safety-related areas where double checking is common, this can have a negative impact on work outcomes,” says Onnasch.
The study indicates that examining human versus robot capabilities could help engineers determine which entity should perform a task first. In some instances, robotic vision systems exceed the capabilities of human vision. When this is true, a company should have a robot check the work that people performed. In other instances, robotic vision systems perform more poorly than human workers.
For example, robotic vision systems can miss fine cracks. They can also confuse small grains of dust or oil residue with fine cracks. When a task involves spotting and distinguishing fine cracks, dust grains, and oil residue, a company should have a person check the work that the robot performed. Alternatively, the company could mandate that only human workers perform the task.
A company might also benefit by refraining from telling human workers that robots were involved in completing a task before them.
Cymek acknowledges that the main limitation of the research is the laboratory setting.
“To find out how big the problem of loss of motivation is in human-robot interaction, we need to go into the field and test our assumptions in real work environments, with skilled workers who routinely do their work in teams with robots,” says Cymek.