Sensors are the eyes and ears of your operation and actuators are the hands.
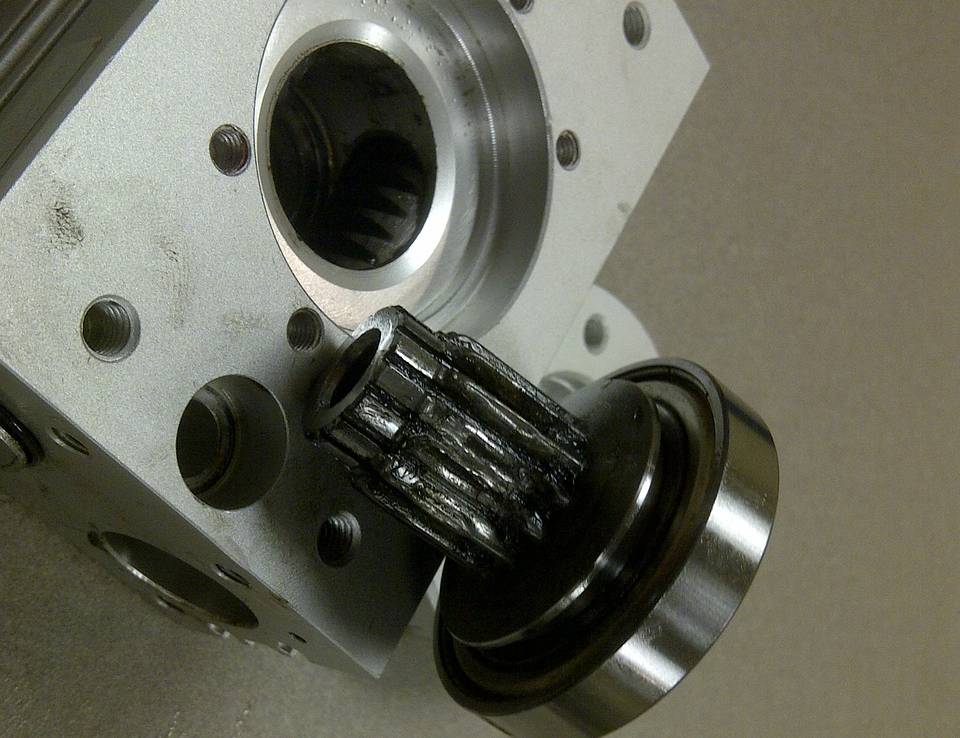
Every manufacturing engineer considering an IIoT implementation should put considerable focus into how the systems contribute to data collection, real-time decision-making and automated control within the production environment.
Sensors are the eyes and ears of your operation. These data collection devices continuously monitor various physical or environmental parameters on the shop floor. Sensors have been developed to measure almost any condition on the shop floor. Here are some common types:
Temperature (for controlling furnaces or ovens)
Pressure (for monitoring hydraulic or pneumatic systems)
Vibration (for detecting imbalance in motors or machinery)
Humidity (for ensuring optimal conditions in certain manufacturing processes)
Proximity (for part detection on a conveyor belt or pallet)
Torque and Force (for ensuring precise assembly or machining)
These days, most sensors provide real-time data that are essential for understanding the status of machines, the health of equipment and the quality of products.
Sensors can capture data continuously or at regular intervals, feeding it back to a centralized system or edge devices. This data allows you to monitor machine performance and production quality in real-time. By continuously monitoring conditions such as temperature, vibration and pressure, sensors can help predict equipment failures before they happen—enabling predictive maintenance strategies. This minimizes downtime and unplanned repairs. Sensors can also ensure product quality by tracking parameters such as size, weight or chemical composition, ensuring products are within acceptable tolerances.
The data collected by sensors is sent to centralized cloud systems or edge devices for real-time analysis, enabling manufacturers to make informed decisions on production adjustments and process improvements.
Actuators: The Hands of Your IIoT System
Once sensors collect and transmit data, actuators play the critical role of executing actions based on the data received. Actuators are devices that respond to control signals by performing physical tasks, including:
Opening or closing a valve (to control fluid or gas flow in a pipeline)
Adjusting motor speeds (for conveyor belts or robotic arms)
Turning machines on or off (for automated start/stop of equipment)
Controlling temperature (by activating heating or cooling systems)
Moving robotic arms or equipment (for assembly, material handling or other precision tasks)
In an IIoT system, actuators are responsible for automating responses to specific conditions detected by sensors. This creates the foundation for closed-loop control systems that can operate independently of human intervention. For example, if a temperature sensor detects overheating, the actuator could activate a cooling system without manual intervention. This automation reduces human labor and the chances of errors or inefficiencies in production. It also speeds up response times to deviations, minimizing waste and downtime.
Actuators can also adjust machine settings dynamically. For example, based on real-time data, they can modify the speed or pressure of a machine, ensuring the production process adapts to the changing needs of the workflow.
In more advanced IIoT setups, edge computing and AI-driven algorithms use sensor data to make autonomous decisions, triggering actuators without human oversight. This could be as simple as adjusting a process or as complex as rerouting products based on real-time data streams.
Working together in IIoT
In a typical IIoT system, the interaction between sensors and actuators follows a continuous cycle of data collection and response, which is often referred to as closed-loop control. Here’s an example:
Sensors detect changes: A temperature sensor detects that the temperature in a furnace is rising above the set threshold.
Data is sent: The sensor transmits this information to the controller (either an edge device or cloud platform) in real-time.
Data is analyzed: The controller analyzes the data and determines that corrective action is needed (e.g., the furnace is overheating).
Actuator takes action: Based on the analysis, the controller sends a signal to an actuator that opens a valve to release cooling air or turns on a cooling system.
Process adjustment: The actuator performs the task, and the sensor continues to monitor the process, feeding back data to ensure the temperature returns to safe levels.
Benefits of sensors and actuators in manufacturing
Increased Production Efficiency:
Sensors and actuators enable real-time adjustments to processes, ensuring that machines operate within optimal parameters. This minimizes downtime and keeps production flowing smoothly.
Enhanced Predictive Maintenance:
Continuous data from sensors allows for early detection of wear and tear or impending failures, reducing the need for reactive maintenance and minimizing unexpected breakdowns. Actuators can automatically adjust processes to prevent equipment damage.
Improved Quality Control:
Sensors track key quality metrics, and actuators can adjust the process instantly to ensure product quality remains consistent, reducing waste and scrap.
Operational Flexibility:
Sensors and actuators provide greater control over manufacturing systems, enabling them to respond flexibly to changes in production schedules, environmental factors, or even supply chain disruptions.
Cost Reduction:
Automation through sensors and actuators can lower labor costs and reduce human error. Moreover, optimized processes lead to less material waste, contributing to overall cost savings.
Data-Driven Decision Making:
By integrating sensors and actuators with a central data system (cloud or edge-based), manufacturers can leverage real-time analytics to gain actionable insights and make informed decisions to improve efficiency and productivity.
Common challenges
Let’s face it, maintaining a network of sensors and actuators and similar technology in a manufacturing environment can be tricky. Many environmental and workflow factors can result in degraded performance, even if they aren’t integrated into a broader IIoT implementation.
However, in IIoT manufacturing systems, several challenges are directly related to the integration of sensors and actuators into the broader industrial network. One key issue is communication latency and bandwidth limitations. IIoT systems rely heavily on real-time data transfer between sensors, actuators and control systems. Latency or insufficient bandwidth can delay data transmission or actuator responses, which is particularly troublesome in time-sensitive applications where quick reactions are essential.
Another challenge is connectivity and reliability issues. Since IIoT systems often involve wireless communication (e.g., Wi-Fi, LPWAN, or other IoT protocols), connectivity problems like signal dropouts, weak coverage or protocol incompatibility can disrupt the flow of critical data. In a networked environment, these disruptions can lead to missed sensor readings or commands not reaching actuators, causing downtime or unsafe conditions.
The sheer volume of data generated by IIoT devices can also lead to data overload and management challenges. With sensors constantly transmitting data, storage and processing systems can quickly become overwhelmed, making it difficult to extract actionable insights or react quickly to system needs. This can hinder operational efficiency, slow decision-making, and complicate data analysis.
Security vulnerabilities are another significant concern in IIoT systems. As sensors and actuators become more interconnected, they are exposed to potential cyber threats. Hackers could access the network to manipulate sensor data or control actuators, posing serious risks to both data integrity and physical safety.
Lastly, sensor and actuator compatibility can be an issue when integrating devices from different manufacturers or upgrading legacy systems. IIoT environments require seamless communication between different components, and incompatible sensors, actuators or communication protocols can lead to integration problems, system inefficiencies or even failures in real-time operations.
To address these challenges, best practices include using real-time networking protocols, implementing strong cybersecurity measures, employing edge computing to process data closer to the source, and ensuring that systems are compatible and interoperable across the IIoT network. These steps help ensure that the IIoT infrastructure operates reliably and efficiently.