Exploring the benefits, challenges and future potential of generative design in aerospace.
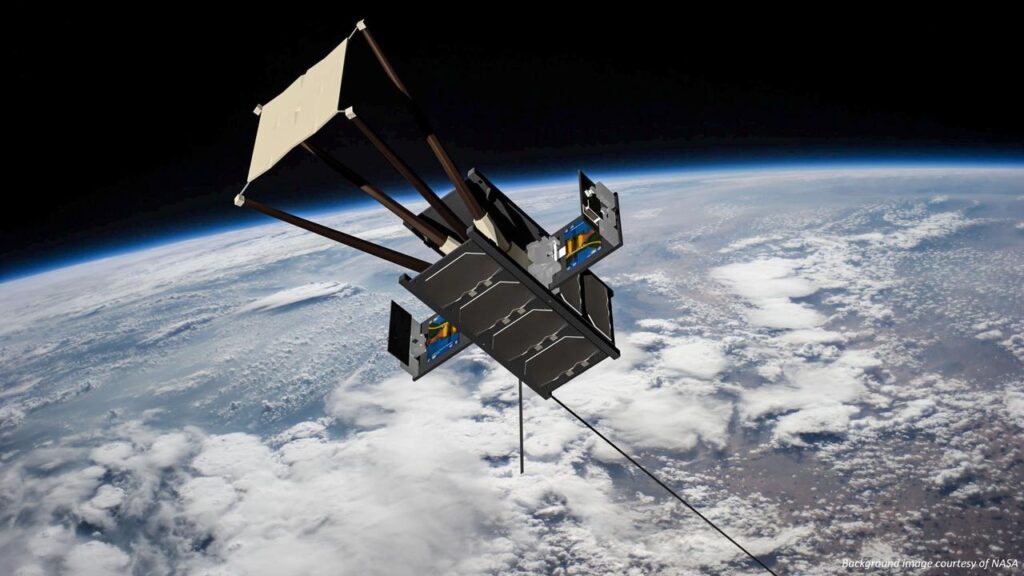
Generative design represents a transformative approach to engineering and manufacturing, particularly for aerospace manufacturers, which face stringent performance, weight and efficiency requirements.
This method leverages advanced computational algorithms to explore and generate optimized designs based on specified parameters and constraints. In aerospace, generative design offers significant advantages by producing innovative, lightweight and highly efficient parts tailored to meet specific needs such as aerodynamics, structural integrity and fuel efficiency.
Principles of generative design
Generative design harnesses the power of algorithms and computational simulations to explore a vast range of potential design configurations at a speed no human would be capable of matching.
Unlike traditional design methods that rely heavily on human intuition and experience, generative design starts with defining design goals, constraints and performance criteria. These could include factors such as load requirements, material properties, manufacturing constraints, and operational conditions.
Generative design algorithms explore numerous design iterations automatically, considering various combinations of shapes, materials and structural arrangements. Many fundamental algorithms and theoretical frameworks behind generative design are developed in universities and research institutions where academic researchers focus on the mathematical and computational aspects of design algorithms. Companies specializing in design and engineering software also create and implement generative design algorithms within their tools. These companies employ teams of engineers and data scientists who develop and refine the algorithms for practical applications based on advances in computational technology and design theory.
Generative design often integrates with advanced simulation tools such as finite element analysis (FEA) and computational fluid dynamics (CFD) to evaluate and validate the performance of generated designs under real-world conditions. Another common technique in generative design is topology optimization, which minimizes material usage while maximizing structural performance by iteratively removing material from less critical areas and reinforcing areas subject to higher stress loads.
By exploring unconventional shapes and configurations that might not be intuitively obvious to human designers, generative design can uncover solutions that optimize weight, strength and performance.
Benefits of generative design in aerospace
Generative design offers several compelling benefits critical to aerospace applications. Here are a few:
Weight Reduction and Optimization: Generative design can produce lightweight structures by removing excess material while maintaining or enhancing structural integrity.
Performance Enhancement: Aerospace components designed using generative techniques can be optimized for specific performance criteria such as aerodynamics, thermal management, and acoustic properties.
Complex Geometry Handling: Aerospace parts often require complex geometries to meet functional and aerodynamic requirements. Generative design excels in handling such complexities by creating organic and efficient shapes that traditional manufacturing methods may find challenging to produce.
Manufacturability and Cost Efficiency: While generative designs can be highly complex, advancements in additive manufacturing (AM) technologies facilitate the production of intricate geometries with minimal waste. This enhances manufacturability and reduces material costs over traditional machining methods.
Innovation and Rapid Iteration: Generative design fosters innovation by allowing engineers to explore a broader design space and quickly iterate through potential solutions. This agility is crucial in adapting to evolving aerospace requirements and technological advancements.
Challenges and considerations
Despite its transformative potential, generative design in aerospace faces several challenges. The computational resources required for generative design can be substantial, particularly for complex aerospace components. High-performance computing infrastructure and efficient algorithms are essential to manage this complexity effectively, and neither come cheap. It’s not just required for the design phase of any product—validating generatively designed parts for performance under various operating conditions is crucial but is also resource-intensive.
Even with the required computational horsepower, integrating generative design into existing engineering workflows and CAD systems isn’t easy. Ensuring compatibility, data interoperability and seamless transition from design to manufacturing are critical considerations. Many software companies are developing solutions to this compatibility
Optimal designs generated by algorithms may require materials with specific properties that traditional materials may not readily offer. Identifying suitable materials and qualifying them for aerospace use are ongoing challenges and exotic materials are always more expensive.
While generative design automates much of the design exploration process, human expertise remains essential for interpreting results, refining designs based on engineering judgment and ensuring the feasibility of manufacturing and operational requirements. This requires highly skilled engineers with a strong understanding of how generative design works and how to use it properly.
Future implications of generative design
The future of generative design in aerospace boasts of some exciting developments. Integrating artificial intelligence (AI) and machine learning (ML) with generative design could enable systems to learn from past designs, predict performance outcomes and suggest novel solutions that continuously improve over time without human intervention.
As computing power and simulation capabilities continue to advance, generative design will expand its scope to explore more complex and multidisciplinary design spaces. Connecting generative design with digital twin technologies will produce real-time monitoring and optimization of aerospace components throughout their lifecycle, from design and manufacturing to operation and maintenance. All of this data will be shared via cloud-based platforms and collaboration tools to facilitate global teamwork and knowledge sharing among engineers, accelerating innovation cycles and enabling faster deployment of optimized designs.