Scenes from 3DEXPERIENCE World 2023, part 2.
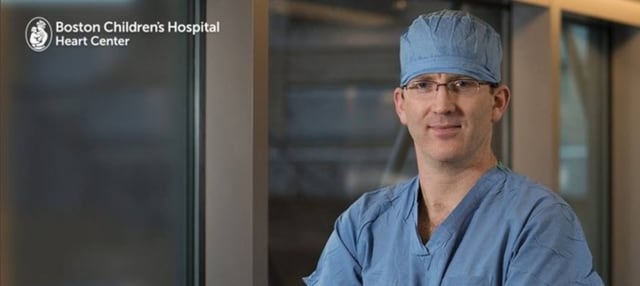
Dr. David Hoganson is a pediatric cardiac surgeon. This — and the fact that he wears a suit — sets him apart from every other attendee and presenter at 3DEXPERIENCE World 2023. His presence confirms Dassault SysteÌ€mes’ claim that making life is more important than making things — and what is more indispensable to our lives than a healthy, beating heart?
“Our heart beats without fail for a long time,” says Bernard Charlès, CEO of Dassault SysteÌ€mes, as he welcomes Dr. Hoganson to the main stage.
Dassault Systèmes has supported the Living Heart Project for some time. Dr. Hoganson is familiar with the Dassault Systèmes model of the heart as a teaching and learning model. But because his patients are children and each heart is unique, he relies on detailed patient-specific 3D models of their hearts created from CAD scans or MRIs that show the congenital defects and enable him to determine how to repair them.
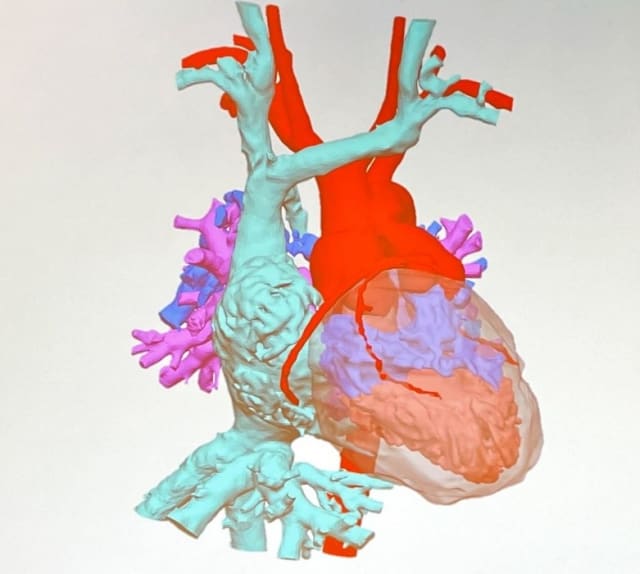
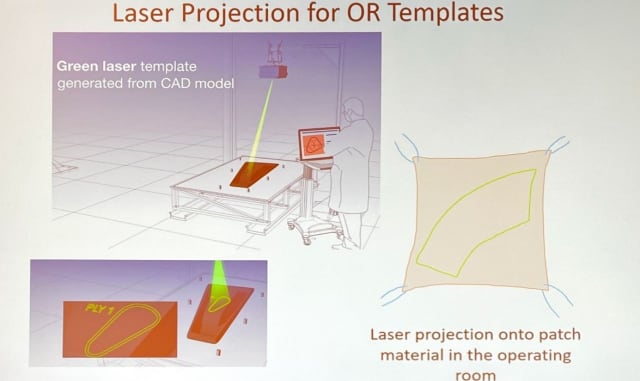
The pediatric heart surgeon faces unique challenges. They have to work on a heart that is depressurized, which means it is a different shape than the 3D model of the beating, pressurized heart they studied to prepare for the surgery. In addition, there is the matter of scale. The 3D model is conveniently colorized, with each color representing different functional and operating areas. The model is also studied at many times the heart’s actual size, but when it comes time to operate, the real heart can be quite tiny.
“There’s a triangular-shaped hole between the mitral valve, which is in purple, and the pulmonary valve, which is in red,” says Dr. Hoganson, pointing to the 3D model of a child’s heart. “On the other side is the electrical system. We have to work very hard to not injure it or the child will be dependent on a pacemaker for the rest of their life.”
Like real heart muscle, the patch material is anisotropic, with different properties along different directions. It operates similarly to carbon fiber in an epoxy matrix — a composite material that is the stuff of aircraft and race cars, and which Dassault SysteÌ€mes’ simulation tools (SIMULIA and ABAQUS) are all too familiar with.
Using ABAQUS, Dr. Hoganson was able to ensure that the heart patch material, cut in the flat, would be able to stretch to a 3D shape against the pressures of the flow of blood in a pumping heart.
“It’s a real challenge, right? It’s a three dimensional problem. The patches I showed were totally flat, or pretty flat. We worked hard to create a workflow to design patches to enlarge the aorta and in creating a really complex shape. It makes almost a 180-degree-turn one way, but the patch has to fold something like nine ways. We start with the flat patch; that patch is quite flexible. Because the patch is anisotropic, it can flex more in one direction than the other. Until now, we didn’t have any information the surgeon would need about how it flexes and how much it flexes. And so there’s been a lot of guesswork about trying to cut that patch. But now, the theory gets the curves correctly. The patch doesn’t buckle and it’s the right size. We were able to do that with a workflow that uses a number of very advanced aerospace tools within the 3DEXPERIENCE platform. We’re able to account for the mechanical properties, the pressure and the shape of the arteries pressurized, because that’s all we care about.”
“We’re so excited,” Dr Hoganson continues. “I can’t tell you about the challenging math it takes to do that in 3D space, used in the tools that repair airplane wings, with material that is anisotropic and complex 3D shapes. This is used by their aerospace group. They taught us how to use those tools. They are really powerful, but in another way, they are also the right tools for the right application. That is remarkable.”