Computer-aided engineering (CAE) software is a critical part of product design and development, and knowing how to use it can boost your engineering career.
Simulation is a critical part of product design and development, allowing engineers to test and validate designs at various stages in the process. It helps teams save time and costs, optimize physical prototyping and encourage innovation and more sustainable designs.
Engineers use simulation technology to evaluate a model in a virtual environment and predict how it will behave in the real world.
A model is a representation of an object, system or process, such as a bearing for an industrial robot, a landing gear system for commercial aircraft or a food packaging process. Engineers create 3D models of components, machines and structures using computer-aided design (CAD) software and then use computer-aided engineering (CAE) software to test and evaluate the models under defined conditions.
For example, an engineer may design a component in CAD and then use CAE software to simulate peak loading conditions to analyze the component’s response. If simulation results show that the component satisfies requirements, engineers may build a physical prototype to validate the part in the real world.
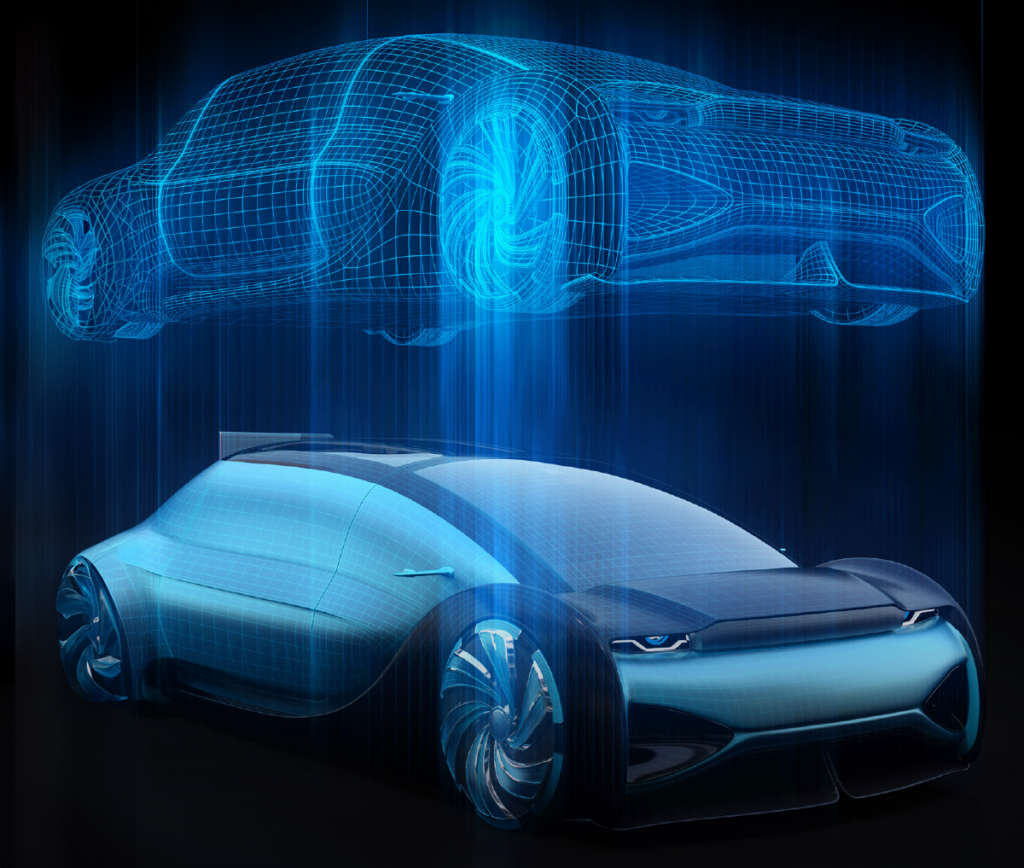
Additionally, engineers can use simulation software to explain why a component or structure failed. For example, if many customers report that a machine fails repeatedly at a particular connection, engineers can use simulation tools to understand the problem and improve the design. Thus, simulation can be used at numerous points in a product lifecycle.
Engineers also use process simulation software to model and analyze manufacturing processes, such as production lines, robot operations and automated warehouses. Others leverage physical simulators, such as flight or heavy equipment simulators, incorporating gaming software and even virtual reality (VR) or augmented reality (AR) to conduct human-in-the-loop testing. Physical simulators are often used for training and evaluating a system or process involving human decision-making.
For engineers who design products, components, machines and structures, there are three widely used simulation techniques: finite element analysis (FEA), computational fluid dynamics (CFD) and multibody dynamics (MBD).
How does simulation software work?
While CAD software creates 3D models representing real-world designs, CAE software creates mathematical models representing the designs based on physics equations. Physical conditions, such as forces and heat, applied to the designs are often described using partial differential equations (PDEs), which are continuous functions with infinite solutions. To compute and output discrete values from such equations, CAE software uses discretization methods that convert differential equations into solvable systems of algebraic equations.
Engineers choose a discretization method based on the design and what they want to analyze. Without getting into the mathematics, here is a simplistic overview of three commonly used methods:
Finite element method (FEM): This method divides a 3D model into many smaller finite elements, collectively called a mesh. The software discretizes the PDEs into algebraic equations for each element. It then solves the system of equations for the entire mesh. FEM solves a myriad of physics problems and is widely used for complex geometries in FEA tools.
Finite difference method (FDM): This method divides a 3D model into a finite grid with evenly spaced intervals and endpoints. The software discretizes the PDEs into algebraic equations at the endpoints and solves the system. FDM is typically reserved for simple geometries that can be divided into structured grids.
Finite volume method (FVM): This method divides a 3D model into many smaller finite volumes called cells. The software discretizes the PDEs by integrating over the cells, accounting for variations between them and balancing fluxes. FVM is often used to solve fluid flow and heat transfer problems in CFD tools.
Since discretization approximates algebraic equations, there are inherent errors in each method. Engineers must understand which method is most appropriate for their models and set up a quality mesh or grid to help minimize such errors.
How to switch to a simulation engineering career
Engineers interested in transitioning to simulation-based roles can start building skills with open-source software and tutorials. Many commercial platform providers also include trials and introductory courses. Consider looking at job postings from various companies to see what software they use and become familiar with those interfaces by building basic models and running simple studies.
Despite the effort to democratize simulation software and make it more accessible to non-experts, engineers should brush up on relevant physics, calculus and programming skills to understand the calculations and ensure results make sense. That might mean revisiting concepts and equations for structural mechanics, fluid dynamics and heat transfer to gauge whether a model accurately reflects a defined real-world problem. It might also mean practicing coding or learning a new scripting language.
Simulation engineers are highly sought after, and many companies are willing to pay top dollar for expertise. Job prospects are favorable in nearly every industry, including aerospace, automotive, construction, electronics, manufacturing, medical and telecommunications. Demand in such industries continues to grow as more organizations seek to improve efficiency, safety and performance while reducing costs and environmental impact.