A new Hexagon report highlights the irony that manufacturing invented the automation and agile practices that are driving business transformation in other industries, while manufacturing lags behind
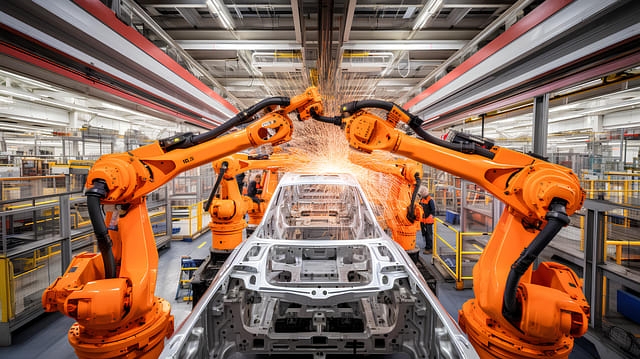
A new report from manufacturing technology company Hexagon underscores the critical importance of data management for manufacturers, revealing that 98% of industry leaders surveyed are grappling with various data issues.
The global survey, conducted by Forrester Consulting and commissioned by Hexagon, emphasizes that unresolved data challenges pose a significant threat to innovation and hinder the adoption of advanced manufacturing technologies.
The Advanced Manufacturing Report spotlights trends and sheds light on the challenges, successes and opportunities faced by manufacturing leaders across their entire value chain.
The majority of business leaders realise that better collaboration can improve product quality (88%), time-to-market (86%). Also, 82% of respondents believe better communication between design and manufacturing teams can significantly reduce material waste and emissions. Despite this, almost three-quarters (71%) of business leaders are concerned about the lack of synergy between their design and manufacturing teams.
A common challenge is the ineffective sharing of data and insights between teams, with 42% expressing concerns in this area. Data availability and quality also emerged as critical pain points.
Collaboration and employee productivity are also significant challenges, affecting 97% of manufacturers, hindering their ability to innovate and respond promptly to customer needs.
Major Impediments to Tech Adoption
The Advanced Manufacturing Report underscores that data availability and quality challenges are hindering the widespread adoption of advanced technologies such as digital twins, automation, and artificial intelligence (AI) in manufacturing. These challenges compound issues related to workplace collaboration, impacting overall productivity and time to market.
The report identifies almost half of manufacturers as “automation laggards,” at risk of being surpassed by rivals that are prioritizing data-driven productivity and automation.
The report reveals fundamental shifts in how high-value products are designed and manufactured, highlighting three key digital enablers: data quality and availability, workforce collaboration and empowerment, and automation.
Data Utilization and Collaboration Challenges:
The impact of data challenges on collaboration and productivity is high, with 97% of manufacturers facing difficulties. Improved collaboration is recognized as a potential remedy, offering benefits such as enhanced product quality (88%), reduced time to market (86%), and improved sustainability through reduced material waste and emissions (82%).
“It’s ironic that manufacturing invented the automation and agile practices that are driving business transformation in other industries and is now struggling to transform – but that’s because achieving digitalisation throughout manufacturing value chains is a very real, complex, and human challenge,” says Josh Weiss, President of Hexagon’s Manufacturing Intelligence division.
“Those that empower their organisation to use data right now can drive more efficient value creation and get products to market faster with the agility to adapt to market conditions. We saw it when consumer electronics led the shift to rapid product innovation, and now BYD has shaken the automotive sector by overtaking Tesla as the electric vehicle market leader, emphasising the need to transform productivity and innovation throughout the manufacturing value chain,” says Weiss.
Digitalization Leaders vs. Laggards:
Only 2% of manufacturers claim to be problem-free with their data practices, signaling a widespread risk of missing business goals. The report categorizes 37% of manufacturers as “laggards” who falling behind in automation efforts, while 25% are identified as “leaders” that have highly or fully automated at least two phases of their manufacturing processes.
Global Disparities and Future Investments:
While high-quality data access is a universal challenge, Asian manufacturers display more confidence in applying their data, leveraging simulation, virtual manufacturing and predictive maintenance. The study also reveals that 58% of Asian companies plan to invest in AI-powered automation over the next three years, outpacing counterparts in North America (45%) and EMEA (38%).