Large companies can make huge gains from a solid AI implementation, but smaller firms can make an impact faster.
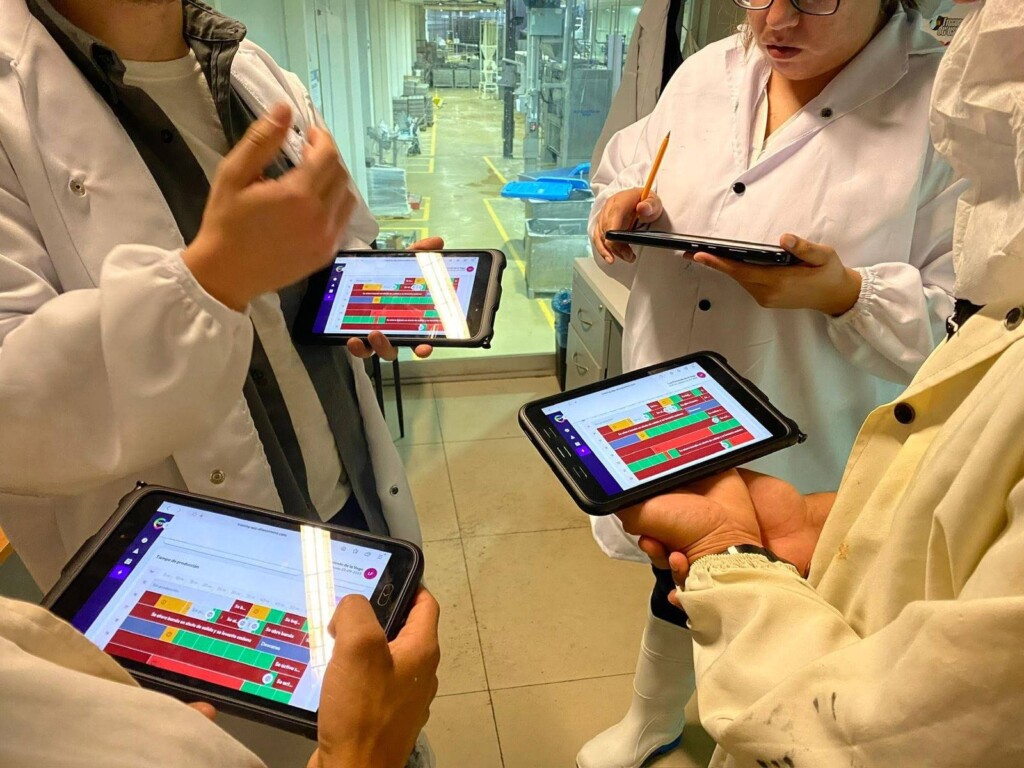
This scene plays out every day across American manufacturing: in a sprawling factory, the hum of machinery produces a metallic symphony that can only be created by the tools of advanced industrial progress. Yet, amid the whir of automated systems, state-of-the-art robots and small autonomous vehicles gliding across the floor to their intended destination, a surprising scene unfolds: a worker stationed in the middle of the shop floor diligently recording real time production data on a chalkboard.
This paradox—a high-tech factory still reliant on humanity’s oldest method of data recording—illustrates a broader issue within the manufacturing sector. Despite substantial investments in advanced software, machinery and automation, many factories lag in digitalization, missing out on the efficiencies that digital transformation and the latest AI technology are poised to deliver.
Alex Sandoval, founder and CEO of Allie Systems, a manufacturing AI developer based in Mexico, has witnessed this scenario numerous times. His company specializes in developing autonomous manufacturing AI agents and aims to redefine how enterprise-scale manufacturers interact with the latest technology. The mission is to bridge the gap between high-tech machinery and the outdated data practices still in use, even in many factories that would rightfully be considered smart manufacturing facilities.
Decoding manufacturing AI
Allie’s AI approach is to inject another dose of intelligence into that already smart manufacturing environment.
“Manufacturing involves numerous machines and computers generating vast amounts of data,” Sandoval explains. “Our role is to tap into that data, which is often underutilized, and turn it into actionable insights.”
Allie AI connects to the various machines within a production facility, gathering data on production quality, process variables and machine health. This data is then used to train an AI agent—essentially a highly specialized software system that becomes an expert in the specific operations of a factory. This AI agent can predict and identify issues, suggest improvements and even take action autonomously.
The challenge of digitalization
Despite the allure of advanced technology, the manufacturing sector faces significant hurdles. Sandoval highlights the irony of modern factories with cutting-edge robotics still relying on outdated methods of data collection. “I visited a top beverage manufacturer, and while their production line was fully automated, they had workers manually recording data,” he says. “It’s a stark reminder that automation does not automatically equal digitalization.”
This disconnect between sophisticated equipment and data management systems creates inefficiencies. The promise of AI in manufacturing lies in its ability to analyze vast amounts of data and provide real-time solutions, but many companies have yet to implement the type of cohesive digital strategy required to effectively train an AI agent.
Big versus small
Allie AI’s clients are predominantly large, enterprise-scale companies across the Americas. These are giants in industries like food and beverage, where the cost of inefficiency can be astronomical. Sandoval’s company has 35 full-time employees and an additional 40 implementation engineers who visit factories to physically install and connect the data gathering systems. This on-the-ground approach is crucial for understanding and optimizing complex manufacturing processes.
However, smaller companies also stand to benefit from AI. According to Sandoval, mid-sized firms have the advantage of agility while potentially valuable projects could lie dormant for months at large enterprises. “While large companies can leverage more data, they often face bureaucratic delays,” he explains. “Smaller firms can move quickly, implementing solutions with fewer obstacles and adapting faster.”
Hype or reality
The promise of AI has faced it’s fair share of skepticism, with some arguing that it has yet to deliver significant value. Sandoval counters this view by pointing to the enormous potential for AI in manufacturing. “Globally, the manufacturing sector wastes trillions of dollars due to inefficiencies,” he notes. “AI can address these issues, but only if applied to the right problems.”
He highlights a real-world example from a cement company in Mexico, where downtime of a single oven can cost $550,000 per hour. By using AI to predict and prevent such issues, companies can achieve substantial cost savings and operational improvements.
It’s unlikely the benefits for smaller organizations will carry a similar dollar value. But the speed of implementation combined with a flatter organizational structure means the benefits, though smaller, will likely be realized much faster and with just as great an impact.
Looking ahead, Sandoval joins the chorus of voices that envision a future where AI becomes integral to manufacturing. “We’re moving towards a time where factories will be managed by AI agents that handle the bulk of operational decisions,” he says. “These agents will analyze data, suggest optimizations and even implement changes autonomously.” Sandoval also acknowledges the human element in this technological shift. The success of AI in manufacturing depends on upskilling the workforce and overcoming resistance to new technologies. “Training and adapting are crucial,” Sandoval emphasizes. “As AI evolves, so must our approach to managing and integrating it into our systems.”