The industrial Internet of Things is playing a pivotal role in shaping the future of manufacturing. Here we explore what it is and how it all started.
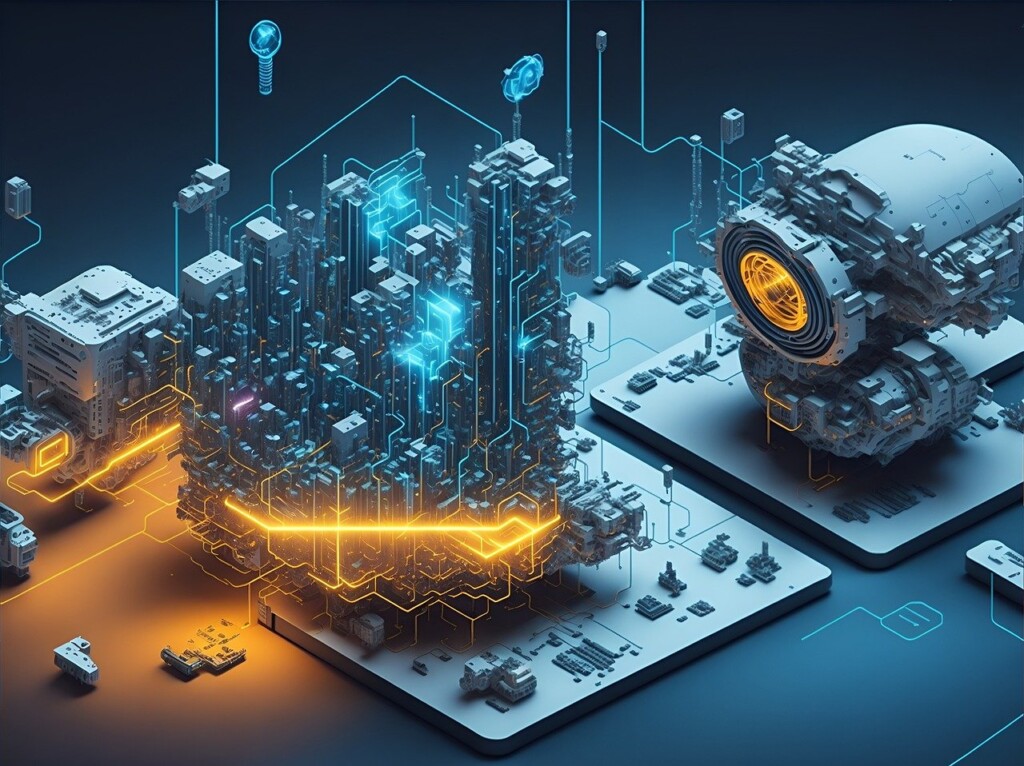
At its core, the industrial Internet of Things (IIoT) is about infusing traditional industrial environments with advanced digital technology. Sensors and smart devices are embedded in machinery to continuously collect data on everything from temperature to vibration. These sensors actively monitor and report on the performance and condition of equipment in real-time.
This data may seem like just a flood of numbers, but with the right mindset it’s a treasure trove of potentially actionable insights. In a well thought out implementation, advanced analytics and machine learning algorithms sift through this data, uncovering patterns and trends that were previously hidden. This means that rather than waiting for a machine to break down, manufacturers can now predict when a failure might occur and address it before any disruption. This proactive approach helps to reduce unexpected downtime and extend the lifespan of equipment.
The connectivity that IIoT brings means managers can adjust processes on the fly, optimize resource use and even automate many aspects of production. This level of automation boosts efficiency and enhances productivity, allowing for more streamlined operations and higher output.
Cost savings are another significant benefit of IIoT. By minimizing unplanned maintenance and optimizing energy consumption, manufacturers can reduce their operational expenses. Predictive maintenance, for example, ensures that equipment is serviced only when needed, rather than on a fixed schedule or after a failure.
Moreover, IIoT introduces a new level of flexibility into manufacturing. Factories equipped with IIoT technology can adapt more easily to changes in designs, demand or shifts in production requirements. Ideally, manufacturers can quickly reconfigure their operations or scale them up or down based on real-time needs, making them more responsive to market fluctuations.
Safety and regulatory compliance are also enhanced through IIoT. The continuous monitoring of equipment helps identify potential hazards before they become serious issues, creating a safer working environment. Additionally, accurate data collection supports compliance reporting with safety standards and regulations.
Additionally, wider supply chains benefit from the integration of IIoT. With better tracking and management capabilities, manufacturers can improve logistics decisions and inventory management, ensuring that materials and products move seamlessly through the supply chain.
In essence, IIoT has the potential to transform traditional manufacturing into a dynamic, data-driven environment. It’s turning factories into smart, connected ecosystems where every machine and process is in constant communication, leading to smarter decisions, greater efficiency, and a more agile and responsive production environment.
Evolution of IIoT: PLCs set the stage
The roots of IIoT can be traced back to the mid-20th century when electronic controls and automation began to take shape. The introduction of programmable logic controllers (PLCs) in the 1960s marked a significant leap forward, allowing machines to be controlled with greater precision and flexibility.
The 1980s and 1990s saw the integration of computer technology into industrial environments. The advent of personal computers and advancements in software led to the development of more sophisticated control systems. Manufacturing Execution Systems (MES) emerged, providing real-time data on production processes and improving operational efficiency. However, these systems were often isolated and lacked the connectivity seen in modern systems.
Enter IoT
The concept of the Internet of Things (IoT) began to take shape in the early 2000s, thanks to the proliferation of internet connectivity and sensor technology. Kevin Ashton coined the term “Internet of Things” in 1999 while working at Procter & Gamble, envisioning a future where everyday objects could communicate over the internet. This concept initially focused on consumer applications but laid the groundwork for what would become IIoT.
The early 2010s marked the formal emergence of IIoT as a distinct concept. As broadband internet and wireless technologies matured, Machine builders began to integrate internet connectivity into industrial machinery and processes. The introduction of smart sensors, which collected and transmitted data about various operational parameters, was a game-changer. These sensors, coupled with advances in cloud computing and big data analytics, enabled real-time monitoring and analysis of industrial processes on an unprecedented scale.
Advancements and adoption
By the mid-2010s, IIoT had gained substantial traction across various sectors. The integration of advanced analytics and machine learning allowed for deeper insights and predictive capabilities. Industries from manufacturing to energy and transportation embraced IIoT to enhance efficiency, reduce downtime and optimize operations. The development of edge computing, which processes data closer to the source rather than relying solely on centralized cloud servers, further accelerated IIoT adoption by reducing latency and improving responsiveness.
Current state and future developments
Today, IIoT is a cornerstone of Industry 4.0, the fourth industrial revolution characterized by digital transformation and smart technologies. Modern IIoT systems leverage a combination of sophisticated sensors, advanced analytics and interoperable platforms to create highly efficient and adaptive industrial environments. Innovations such as digital twins—virtual replicas of physical systems—allow for simulation and optimization of industrial processes in real-time.
Looking ahead, the evolution of IIoT continues with advancements in AI and 5G connectivity, which promises even faster data transmission and more nuanced, automated analysis. As industries strive for greater automation, efficiency and sustainability, IIoT is expected to play an increasingly pivotal role in shaping the future of manufacturing and beyond.