Three factors for determining whether your wearable device needs a soft goods solution, plus three key development considerations.
This article was originally published on Medical Design & Outsourcing on July 25, 2024.
Wearable medical device developers are offering products similar in form and function to a FitBit, Whoop or a number of other wrist-worn devices.
However, a growing number of wearable technologies require placement on other parts of the body, with a great example being Avation Medical’s noninvasive ankle garment for treating overactive bladder by stimulating the tibial nerve.
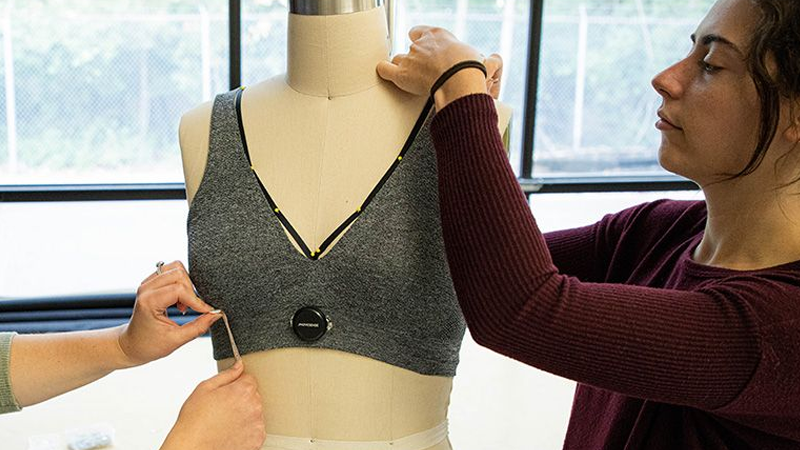
One challenge of these alternate placement requirements is attaching a wearable device to the body in a way that facilitates ease of use, while enabling the technology to live up to its full potential. Here are three factors to determine if a soft goods solution is appropriate for your wearable, and three key considerations during development.
Three wearable factors that call for a soft goods solution
1. When the device must be highly configurable
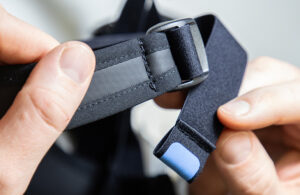
Whether your device has a wide range of wearing options, it’s worn somewhere other than the wrist like the neck, ankle, or torso, or it needs to fit 5%-95% of the population, a soft goods solution can go where traditional hard goods cannot.
Materials such as elastics, knit materials and stretch laminates are excellent for making comfortable, highly configurable devices. Apart from stretch and comfort, soft goods options include tens of thousands of off-the-shelf fabrics, buckles, d-rings and hook and loop parts.
These materials allow variable attachment methods to accommodate a wide range of body sizes and shapes. They also address problems around disposability and multi-patient use.
2. When close contact with the skin is a requirement
Close contact with the skin is a key functional requirement for many wearable technologies, but it can render adhesives or hard plastics inappropriate due to compromised skin or challenging locations like near a patient’s sacrum.
In a perfect world, you would be able to peel and stick the device directly to the skin and have it stay in place without any discomfort or skin irritation. When working with the infinite variability of placing a hard object on a soft human form, it becomes clear we do not live in such a perfect world.
Thankfully, soft goods provide unique strengths in these situations. Fabric has an unmatched ability to conform to a contoured form, allowing it to move and adapt to a body’s movement and provide comfort even with tight-fitting items.
Cleanability is a chief concern with any device in a clinical setting, and cleanable, durable textiles are important options as industry leaders look for opportunities to transition from disposables . While there is a spectrum of cleanability and durability, the ability to create custom textiles and narrow goods to target specific functionalities and requirements puts textile-based solutions in a class of their own.
3. When cost is a concern
Soft goods manufacturing is historically one of the more cost-effective ways to produce a product. It is not without its own unique challenges (more on that soon), but simple items like straps, harnesses and covers are excellent places to consider soft goods.
Many manufacturing facilities even have a wide range of line items that are customizable, allowing you to bypass development costs. Depending on the certifications needed for your device, you can expect a wide range of cost estimates and manufacturing lead times. Balancing a manufacturer’s skill with cost is an important consideration when evaluating potential MFG partners.
Key soft goods wearable development considerations
1. Material leads time and minimum order quantities
This is often the make-or-break point in soft goods development. Material development and purchasing can be subject to large minimum order quantities (MOQs) and 3X lead times, depending on what you are trying to source.
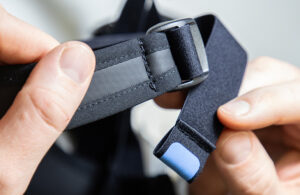
There are many off-the-shelf options, but they may not meet all of your requirements or have the traceability needed for FDA compliance. Developing a custom material gives you unrivaled control over the functionality and sourcing pipeline of your product, but requires additional time.
Whether you are purchasing existing material or developing your own, planning for additional soft goods development and sourcing time at the beginning will pay dividends on the back end. There is no Amazon or McMaster Carr for soft goods materials.
2. Know your testing requirements at the beginning of the design phase
Knowing whether your product needs to prioritize break and tear strength, material contents, wicking and other textile features — or a blend of many things — will help cut through the fog of product design.
And material selection often influences the design. If a material fails at the end of your development, you might need to halt development and restart from the beginning. Having clear constraints and documentation can help avoid this tragic but common pitfall.
Biocompatibility is a major concern, but there are innumerable ways to define, test and certify biocompatibility. Finding devices with similar FDA clearance/approval and functionality can you help you guide your testing and requirements strategy. A certified testing facility or reputable materials supplier can steer you toward the right set of tests.
3. Know your priorities
Soft goods are all about compromise. Your material might be aesthetically perfect, but have a poor hand feel. It may be extremely comfortable, but not pass the EU’s RoHS (Restriction of Hazardous Substances) or REACH (Registration, Evaluation, Authorization and Restriction of Chemicals) regulations or California’s Proposition 65.
Clearly define your priorities to save time trying to source a nonexistent material, cut down on overly burdensome assemblies, and make user needs easier to define. This will ultimately result in a cleaner design with better marketing clarity.
Parting thoughts
Soft goods design and development for medical wearables is not the same as design and development for consumer or retail. We have seen a number of clients make the mistake of working with a garment manufacturer to develop a medical device, and it has gone as well as you might expect. Because of regulatory rigors, medical wearable soft goods often begin by pushing multiple dominos at the same point. Design, material sourcing, manufacturing identification and documentation often start at the same time.
Soft goods is closer to an art than a science, especially when applying a hard wearable to a human form. Each user and use case is different. Adding to this complexity is the reality that each manufacturing partner has different capabilities, skill levels and standards. Knowing how to design to match your manufacturing, how to communicate key construction details, how to liaise with vendors and how materials work on the body are key to getting into production successfully.