CAD and CAE software are two advanced design tools that have become indispensable in aerospace manufacturing.
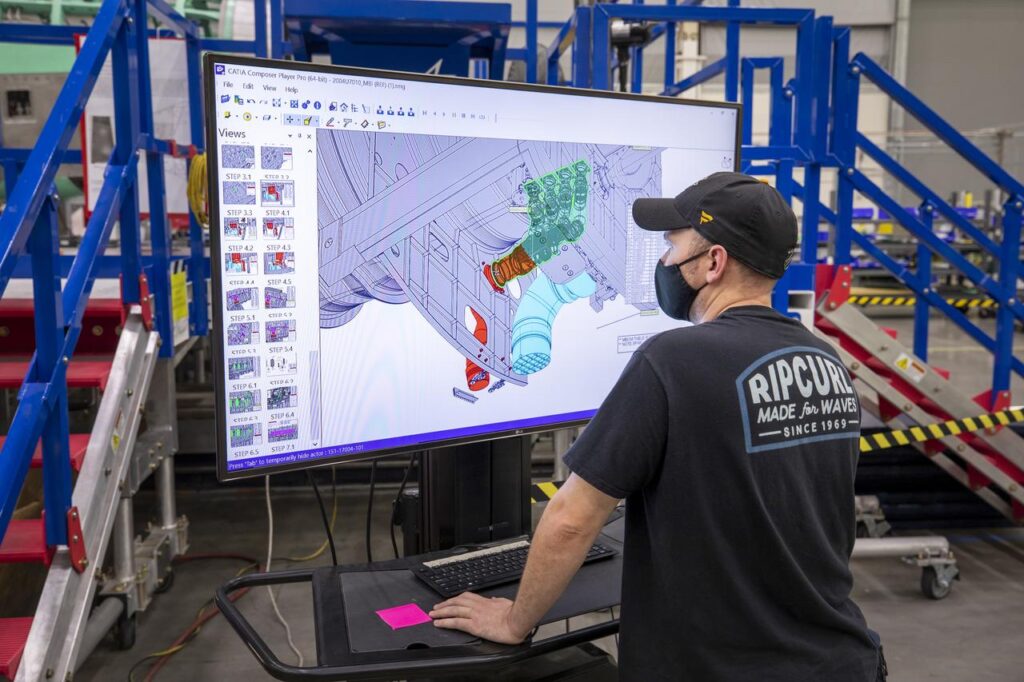
In aerospace manufacturing, several advanced design tools play crucial roles in ensuring efficiency, safety, and performance.
Computer-Aided Design (CAD) software has played a crucial role in aerospace manufacturing for many years. It has evolved to enable more than just design, growing to empower simulation and optimization of components and systems.
CAD software allows engineers to create detailed 2D drawings and 3D models of aircraft components, such as wings, fuselage, landing gear and interiors. Engineers can visualize designs from different angles, zoom in for detailed views and rotate components to examine them thoroughly for performance, weight reduction and manufacturability.
Parametric modeling in CAD enables engineers to define the dimensions, relationships, and constraints of each part within a design. Changes made to one part automatically update related components and assemblies, ensuring consistency and reducing errors.
CAD software also facilitates the assembly of multiple components into a complete assembly and even a full aircraft or spacecraft. Engineers simulate the fitting of parts, check for interferences and ensure that all components align correctly within the assembly.
CAD systems facilitate collaboration among multidisciplinary teams, allowing engineers, designers and analysts to work together on a single digital platform. The software generates detailed documentation, including engineering drawings, bill of materials (BOM) and manufacturing instructions.
Models developed in CAD software serve as a basis for computer-aided manufacturing (CAM) processes, where they are used to generate toolpaths for machining, additive manufacturing or composite layup. Simulation of toolpaths ensure the machinability of manufactured parts.
The CAD software integrates with product lifecycle management (PLM) systems to manage the entire lifecycle of aerospace products, from initial concept through design, manufacturing, operations, maintenance and eventual retirement.
CAD software is indispensable in aerospace manufacturing for its ability to streamline design processes, improve accuracy, optimize performance, and support collaborative efforts across the entire product lifecycle. Its integration with other advanced tools and technologies further enhances its utility in creating safe, efficient and innovative aerospace solutions.
Computer-aided engineering
Where CAD is primarily focused on creating detailed 2D and 3D models of components and assemblies, Computer-aided engineering (CAE) software is used for simulation, analysis and optimization of designs to evaluate their performance under various conditions such as stress, heat, fluid dynamics, and vibrations. CAE software helps engineers predict how products will behave in real-world scenarios, aiding in design validation and performance enhancement. Here are the key details of how CAE software is used in this industry:
Finite element analysis
CAE software allows engineers to simulate how aircraft structures will behave under different loading conditions, such as aerodynamic forces, landing impacts, and vibrations during flight. Engineers define material properties, boundary conditions and loads in the software. Finite element analysis (FEA) calculates stresses, strains, deformations, and factor of safety to ensure that structural components meet safety and performance requirements. It helps optimize designs by identifying areas of high stress or deformation that may need reinforcement or redesign.
Aerodynamics
Computational Fluid Dynamics (CFD) simulates the flow of air around aircraft surfaces and through internal systems. CFD predicts aerodynamic forces, such as lift and drag, which are crucial for optimizing aircraft performance and fuel efficiency. It allows engineers to evaluate different wing designs, control surface configurations, and engine placements to achieve desired flight characteristics.
Thermal analysis
CAE tools simulate thermal behavior within aircraft components and systems. They predict temperatures across surfaces and within structures under varying environmental conditions, such as high-altitude flight or engine operation. Thermal analysis ensures that components remain within safe operating temperatures and allow heat to be managed to prevent thermal stresses and failures.
Multi-physics simulations
Some CAE software platforms integrate multiple physics simulations, such as coupling structural, thermal, and fluid dynamics analyses. This capability is essential for evaluating complex interactions between different physical phenomena within aerospace systems, such as heat transfer in engine components or structural deformation under fluid pressure.
Vibration and acoustics
CAE software models and predicts vibrations and acoustics of aircraft structures and within cabins. Engineers use these simulations to reduce noise levels, ensure passenger comfort, and prevent structural fatigue caused by resonance or excessive vibration.
Impact and crashworthiness:
CAE tools simulate impact scenarios, such as bird strikes or emergency landings, to assess crashworthiness and occupant safety. They predict the behavior of aircraft structures and materials under sudden loads to optimize designs for survivability and structural integrity.
Optimization and design iteration:
CAE software facilitates design optimization by analyzing multiple design iterations quickly and efficiently. Engineers can evaluate different materials, geometries, and configurations to achieve optimal performance, weight savings, and cost-effectiveness.
Certification and compliance:
CAE simulations contribute to the certification process by providing data and analyses that demonstrate compliance with regulatory requirements and safety standards. They help validate designs before physical testing, reducing time and costs associated with certification efforts.
CAE software enables aerospace engineers to simulate, analyze, and optimize complex systems and components throughout the design and development process. By providing insights into structural integrity, aerodynamic performance, thermal behavior, and more, CAE tools support the creation of safe, efficient, and innovative aerospace solutions. Structural analysis, computational fluid dynamics and thermal analysis are essential in aerospace to ensure components meet performance requirements and safety standards.