Discussing the basics of how this production-scale technology is used to manufacture aerospace parts out of both plastic and metal.
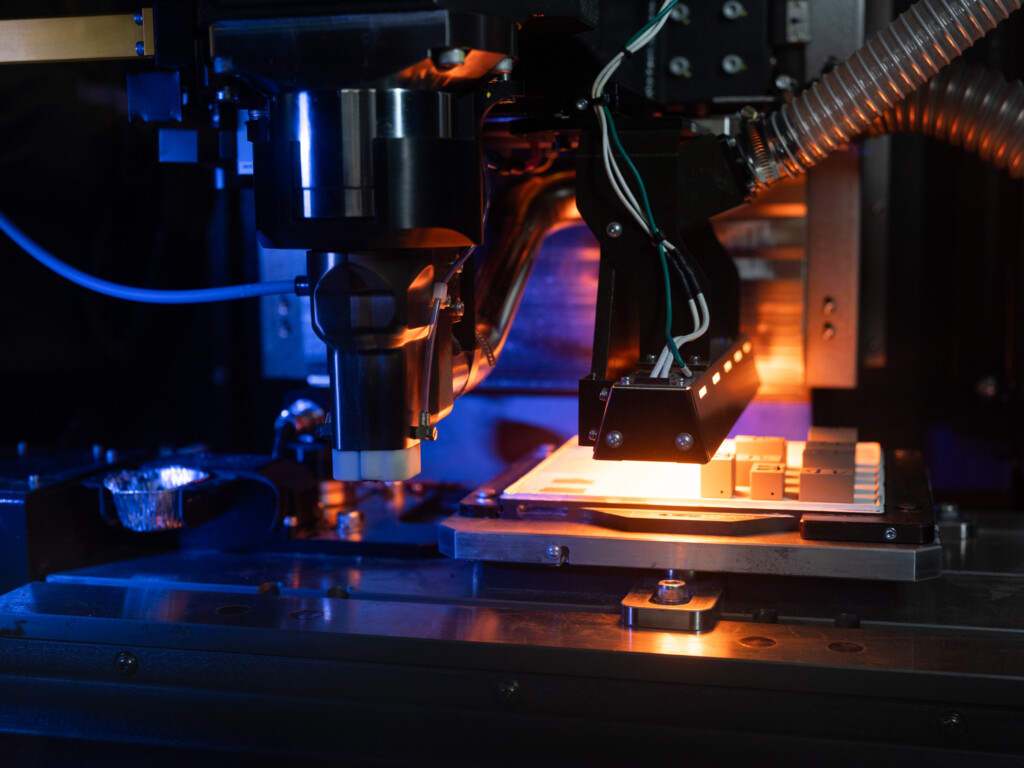
Additive manufacturing (AM), often referred to as 3D printing, has developed into a transformative technology in digital manufacturing and is especially applicable in the aerospace sector. Gone are the days when this technology was reserved for producing physical models during the prototyping phase of product development. It has now become a production-scale technology used to manufacture parts out of both plastic and metal.
Complex design
What makes additive manufacturing such an important piece of the digital manufacturing puzzle is its ability to produce highly complex geometries—including moving parts— that are impossible to achieve using traditional subtractive technologies such as machining, joining and forming.
This is a perfect fit for the aerospace sector, where components often benefit from intricate internal structures, lightweight designs and optimized shapes that enhance performance and efficiency. This “lightweighting” is crucial in aerospace to improve fuel efficiency and increase payload capacity.
AM allows engineers to design and fabricate parts with optimized geometries and material distributions, reducing overall weight while maintaining or even improving structural integrity and performance. It supports a wide range of materials, including metals, polymers, composites and ceramics, which aerospace manufacturers select for specific properties, such as high strength-to-weight ratios, heat resistance and conductivity, which are tailored to meet requirements of each component.
Integration with smart manufacturing
Unlike its traditional manufacturing counterparts, which are built on fundamentals developed more than 200 years ago, additive manufacturing is a relatively recent technology which was developed in tandem with the digital technology boom of the past two decades. Because of this, it integrates nicely with technologies that make up Industry 4.0 and smart manufacturing. This fosters a more interconnected, efficient and data-driven manufacturing environment.
AM supports agile manufacturing by enabling on-demand production of customized parts and reducing lead times compared to traditional manufacturing methods. Smart manufacturing systems can dynamically adjust production schedules and allocate resources based on real-time demand signals and production data.
Additive also minimizes material waste by only using the necessary amount of material required for each part, contributing to sustainability goals by optimizing energy usage and operational efficiency, reducing environmental impact and operational costs.
AM reduces dependency on traditional supply chains by enabling on-demand production of parts and components. It supports customization and rapid prototyping, allowing for iterative design improvements and faster development cycles.
Repair and Maintenance
AM is increasingly used for repair and maintenance operations in aerospace because it allows for the manufacturing of replacement parts on-site or on-demand, reducing downtime and logistics costs associated with spare parts inventory.
Although it has taken a long time, additive manufacturing now represents the paradigm shift industry was always told it could be. It offers unprecedented design flexibility, efficiency gains and performance enhancements. As technology continues to advance, additive manufacturing is poised to play an even more significant role in shaping the future of aerospace production and innovation.
Key terminology for additive manufacturing
STL file: A file format used in additive manufacturing to represent surface geometry of a 3D object. It stands for Stereolithography.
Slicing: The process of dividing a digital 3D model into thin horizontal layers for the additive manufacturing process.
Build plate: The surface upon which objects are 3D printed or built during additive manufacturing.
Fused deposition modeling (FDM): An additive manufacturing technology where a thermoplastic filament is extruded layer by layer to build objects.
Stereolithography (SLA): An additive manufacturing process that uses a UV laser to solidify layers of liquid resin to build 3D objects.
Powder bed fusion: A category of additive manufacturing technologies where layers of powdered material are selectively fused together using a heat source (e.g., laser or electron beam).
Support structures: Temporary structures added to 3D models during printing to support overhanging features and ensure successful printing.
Build volume: The maximum size of an object that can be printed within a particular 3D printer.
Post-processing: Additional steps taken after printing to improve the appearance or functionality of the printed object (e.g., cleaning, curing, polishing).
Selective laser sintering (SLS): An additive manufacturing process that uses a high-powered laser to selectively fuse powdered materials (such as plastics, metals, or ceramics) into a solid 3D structure.
Electron beam melting (EBM): An additive manufacturing process where a high-energy electron beam selectively melts and fuses metal powder particles to build up a 3D object layer by layer.
Direct metal laser sintering (DMLS): A variation of SLS specifically for metal powders, where a laser fuses metal powder particles together to create a metal part.
Binder jetting: An additive manufacturing process where a liquid binding agent is selectively deposited onto powder bed layers to bind them together, forming a solid object.
Material extrusion: A category of additive manufacturing processes where material is selectively deposited through a nozzle or orifice. Includes FDM and similar technologies. Infill: The internal structure of a 3D printed object, which can vary in density and pattern to achieve different mechanical properties and reduce material usage.