Nanjing University of Aeronautics and Astronautics engineers identify factors that influence microstructure in wire arc process.
In metal additive manufacturing (AM), direct energy deposition (DED) offers several advantages over laser powder bed fusion (L-PBF), primarily speed and material cost. However, these benefits tend to be offset by greater variability in surface quality and mechanical properties, as well as a greater propensity for distortions and residual stresses.
That’s why a team of engineers and materials scientists at Nanjing University of Aeronautics and Astronautics (NUAA) in China conducted a literature review to identify the factors with the greatest influence on the microstructural properties of materials which undergo the DED process.
The team employed the principle of dynamic recrystallisation to investigate the influence of heat input during the deposition process and to delineate methods for controlling heat input and its operating mechanisms. Following a comprehensive analysis of the impact of diverse process parameters on melt pool behavior and microstructure during the deposition process, the researchers evaluated various supplementary techniques and treatments for optimizing DED material characteristics, such as interlayer forging and ultrasonic impact.
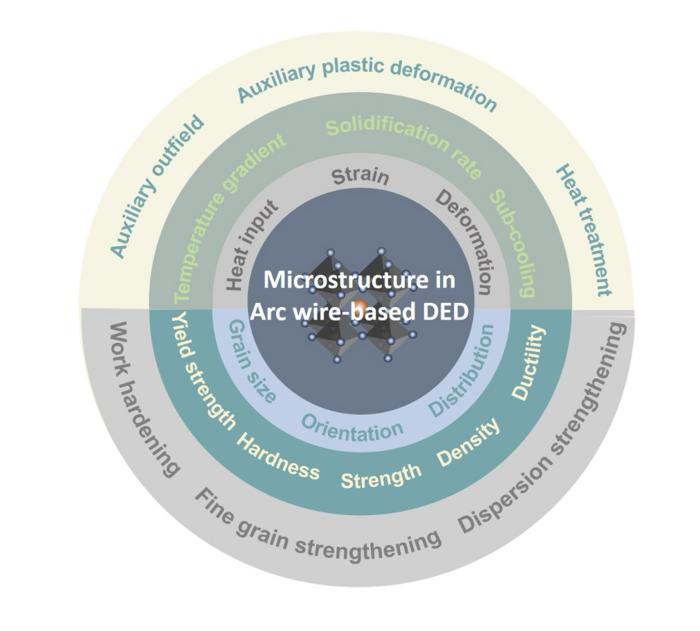
“[Our report] summarizes methods to control the heat input during deposition and highlights various heat treatment techniques to reduce defects and improve the microstructure and properties of the deposited parts,” said Ning Qian, an associate professor at NUAA who contributed to the research. “These techniques include pre-deposition, process, and post-deposition treatments. The study also investigates methods for introducing deformation strengthening and briefly reviews their advantages and disadvantages. Lastly, the manuscript presents the future development direction and research focus of Arc wire-based DED.”
According to the team, the study provides a comprehensive understanding of methods for enhancing the microstructure and material properties of wire-based DED. More specifically, they highlight four key aspects to improving the mechanical properties of wire-based DED parts:
- Controlling heat input
- Controlling solidification behavior
- Controlling the dynamic recrystallization process
- Controlling deleterious phases and defects
The paper is published in the open-access Journal of Advanced Manufacturing Science and Technology.