3D printing obviates molds and shortens supply chains for custom part development.
At this year’s Tokyo Auto Salon, Subaru unveiled the latest concept of its Boost Gear package trim level for the Subaru Outback for customers who are enthusiastic about overlanding: going off the grid to travel to and camp in remote locations. Ironically, the package was enabled by advanced 3D printing technology in the form of HP’s Jet Fusion.
In developing parts for the new Boost Gear package, Subaru sought to overcome certain manufacturing challenges with automotive parts. Specifically, the company wanted to avoid using dedicated molds that would restrict design freedom by the direction of mold removal since this makes customization and low-volume, high-mix parts more difficult to develop. Subaru was also concerned about the logistical difficulties and increased emissions resulting from extended supply chains.
To these ends, HP’s Multi Jet Fusion technology was an ideal solution, balancing part strength requirements and mass production capabilities. Utilizing HP Jet Fusion eliminated the need for molds and enabled the automotive engineers to develop unique parts in a limited timeframe.
For materials, they used HP 3D High Reusability PA 12 (Nylon 12) to achieve the necessary part strength as well as heat and weather resistance. The HP Jet Fusion’s reported material recycling rate of up to 80%, in combination with 3D printing’s ability to shorten supply chains by sending bits instead of atoms helped Subaru achieve its environmental goals.
Concept car parts made with Multi Jet Fusion
“We automotive designers have always been constrained by molds, struggling with issues like part separation,” said Kanenori Susaki, Manager, Accessories Planning Department, Parts & Accessories Division at Subaru in a press release. “However, by using 3D printing, we are freed from all issues such as the angle of mold removal and the appearance of parting lines, significantly enhancing design freedom. We aim to actively adopt 3D printing, which is suitable for low-volume, high-mix production, to provide customers with more enjoyment.”
Using Multi Jet Fusion technology, engineers at Subaru and DMM.com LLC created four removable parts over the Outback’s fender:
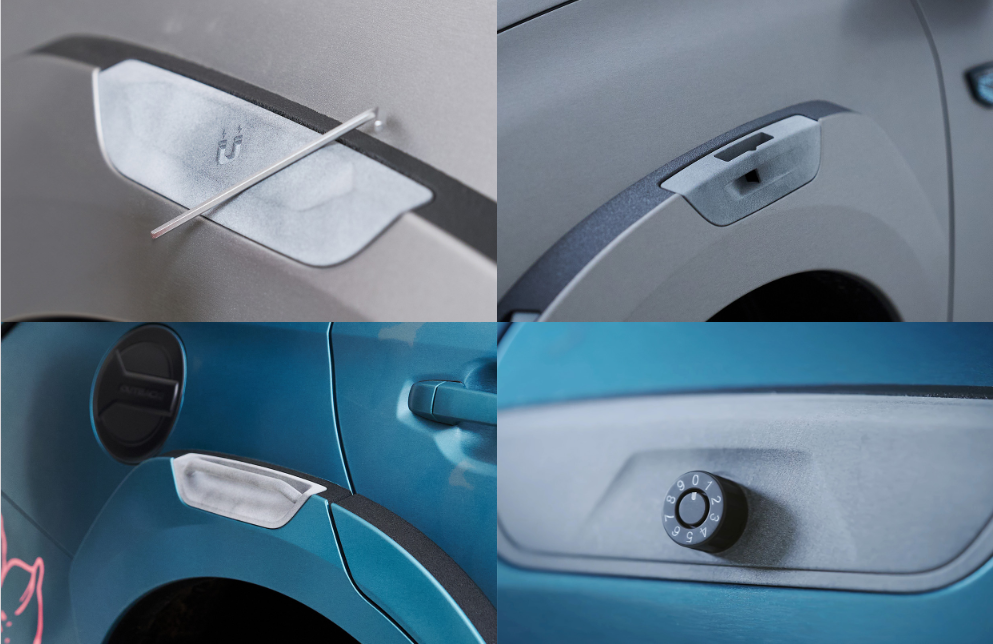
Top Right: A part that becomes a speaker when a user inserts a smartphone, allowing people to enjoy music outside the car
Bottom Left: A hangar with a shape that takes advantage of the unique features of 3D printing without restrictions like the direction of mold removal
Bottom Right: A lockable locker for temporary storage of car keys when surfing or enjoying other activities
(Image: HP)
“Around the world, a wide range of industries are utilizing the power of 3D modeling for flexible design, accelerated product development, and sustainable manufacturing,” said Nobuki Okado, Managing Director for HP Japan in the same release. “We are delighted that HP’s 3D printing technology, the Multi Jet Fusion platform, has been adopted for Subaru’s automotive parts. HP Japan will continue to collaborate with domestic partners and customers to provide the latest solutions that meet industry needs.”