When creating metal components, engineers should carefully weigh the pros and cons of these two manufacturing methods.
Xometry has sponsored this post.
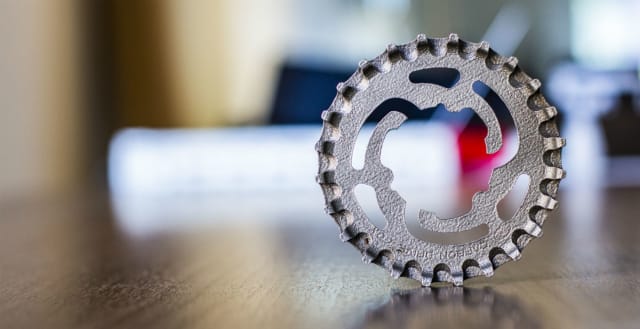
Choosing the right manufacturing method is essential to a product’s physical and economic performance.
Machining via computer numerical control (CNC) is the long-established standard, where a part is produced by removing metal from a workpiece according to a computer program. Metal 3D printing is the new technology on the block, where a machine builds up a part, layer by layer, using processes such as sintering, welding and melting.
While 3D printing is becoming increasingly popular, manufacturers need to consider carefully whether it offers sufficient advantages over conventional CNC production for their particular application.
Here are five things to keep in mind when deciding which process is right for you.
1) 3D Printing Is Not An “Easy Button”
“People think about metal 3D printing as that ‘easy’ button,” said Greg Paulsen, Director of Applications Engineering and Marketing at Xometry, a manufacturing-on-demand service provider. “That I used to get this component this way, and now maybe 3D printing is going to be cheaper or faster.”
Sometimes that’s a fair assessment, especially if the part has a lot of pocketing and is designed for 3D printing at its inception. If the component is designed to be produced via CNC, “you’re not getting the value add that metal 3D printing can really offer, where you’re designing with metal 3D printing in mind, which is a very different approach in manufacturing,” said Paulsen.
“Many people may not be aware that metal 3D printing comes with a number of challenges. This is because, unlike traditional machining methods where you carve out a piece from a larger block of material, metal 3D printing involves building a part from scratch, layer by layer, using a series of micro welds.” said Tommy Lynch, Senior Applications Engineer for additive at Xometry.
Parts built with metal 3D printing typically see a significant amount of internal stress after the metal powder melts and then resolidifies as it cools. The rapid change in temperature causes each layer to try to curl upward during build—which is why the build relies on support structures to keep the product anchored to the build plate. When the build is completed, those supports need to be removed, which comes with the risk of damaging critical features in the process.
It’s rarely as simple as pushing a button to start the printer and then unloading a completely finished part.
2) 3D Printing and CNC Machining Have Different Strengths and Weaknesses
Producing a part through CNC machining is a vastly different process than producing it with a 3D printer—and the nature of the part has a significant influence over which method is better for producing it.
CNC machining is a subtractive manufacturing method: material is removed from a solid block using a variety of cutting tools to produce the part based on a CAD model. The more complex the part, the more time it takes to produce: a shaft with threading can be created on a basic turning machine, while a blisk requires a full 5-axis mill. The material also makes a big difference, with harder metals requiring more specialized cutting tools.
In contrast, 3D printing involves “growing” a part on a blank baseplate, creating it by adding material one layer at a time. In this case, the complexity of the part and the material from which it’s made make much less of a difference to the cycle time.
“The second you have a profile that has a spline or keyway, or curvature—a manifold design, for example—3D printing becomes a lot more value added,” said Paulsen. “With additive manufacturing, less is more. With CNC machining, the work is removing the material, so you have different cost drivers on it.”
3) Designing for 3D Printing Requires Different Considerations
Just as these two manufacturing methods differ in process, they also differ in how engineers should approach part design.
With 3D printing, the part needs to be designed to factor in a set build orientation; ideally it would be designed to optimize and minimize the need to use supporting structures. “The role of the supporting structures is to win the battle of the part versus the build plate,” said Paulsen. “It’s like a tug of war…you start with about an inch and a half of a steel build plate, and you’re fusing your first layers down to that, and then every subsequent layer is fused on top of either the part structure itself or the supporting structures underneath.”
According to Paulsen, it is similar to coral on a reef: it’s mounted to a structure and grows out of it, and the shape of the organism (or part) depends on the support structures available to it. In any 3D printing process, the design needs to factor in the bottom-to-top fixed orientation as well as the intended function of the component itself. Because the supporting structures are also metal, they increase material consumption, build time and post-processing labor to remove.
“Ask yourself, how can I get my core functionality out of my design, and design it in a way where you either mitigate or remove the need for supports,” he said. “Designers have to really understand that process to unlock the true value of metal additive.”
Selective laser sintering in 3D printing. (Video courtesy of Xometry.)
4) Converting Parts from CNC to 3D Printing Can Be Challenging
Paulsen and his team at Xometry have found that companies exploring 3D printing as a replacement for CNC often look at the components they already produce using traditional manufacturing methods and study the costs of producing the same part with a printer. But this decision is more complex than just swapping out equipment.
CNC machining is an established method that has been around for decades, and the CNC-produced part has likely gone through many optimizations already. Many of the assumptions made in the CNC process are taken for granted because of years and years of best practices. “A lot of that has to be rediscovered or substituted and validated in a 3D printing world,” said Paulsen. These necessary steps tend to create more complexities in the product design and approvals processes. In some cases, it’s like reinventing the wheel.
“It doesn’t always make sense in terms of price because milling or turning could be cheaper,” said Lynch. “And if you’re really going to volume production into the hundreds, then traditional machining will almost always win.”
Cracking and warping are the most common problems encountered when trying to 3D print parts designed for CNC, particularly for pieces that are either chunky or very thin. When hundreds or thousands of welds are stacked on top of each other it generates a tremendous amount of stress, potentially to a point where the component will either crack, flex or break away from the build plate, resulting in build failure.
These technical challenges can engender a broader reluctance to adopt metal 3D printing, due to the cost of failed builds. Unlike 3D printing plastics, where the material costs are much lower, the stakes are higher in metal. With a premium on pricing, equipment and post-processing, a failed metal print could cost thousands of dollars in wasted powder and lost productivity. In many cases: it’s not always clear if a part is successful until the build is complete.
“The designer is at somewhat of a disadvantage because if the part is not designed within a certain level of confidence of build success, then most service bureaus are hesitant to take a risk on unproven designs with a high likelihood of failure,” said Lynch. “It is not beneficial to the customer or the manufacturer to push the limits of the technology only to demonstrate why parts need optimization. Metal printing can be highly collaborative, and we try to guide customers down the path of success on the first try.”
5) You Can Access 3D Printing Services Without a 3D Printer
Some companies may find that it is worth the price to incorporate 3D printing into their operations, but don’t have the budget to buy a metal 3D printer of their own. A viable option for them could be 3D printing service bureaus such as Xometry.
Xometry, for example, is a digital manufacturing marketplace that connects the people who need a part printed with the suppliers that make the part through an integrated platform. A company using Xometry could upload a file, get a price and lead time estimates from suppliers who have already been vetted by Xometry, and make their purchase decision then and there.
“A service like Xometry gives you access to millions of dollars of industrial equipment. You upload the 3D file and you’re essentially reserving and renting space on the machine just for that print,” said Paulsen. “You don’t just have a metal 3D printer, you have a machine shop beside you that’s supporting your needs.”
While metal 3D printing may not be the “easy” button manufacturers have been hoping for, it still has the potential to significantly increase productivity and help a company’s bottom line—as long as the engineers do their homework to determine whether it’s the right call over conventional CNC production.
Get an Instant Quote on 3D printing and more at Xometry.