Impact absorbing technology is a constant balancing act between competing factors.
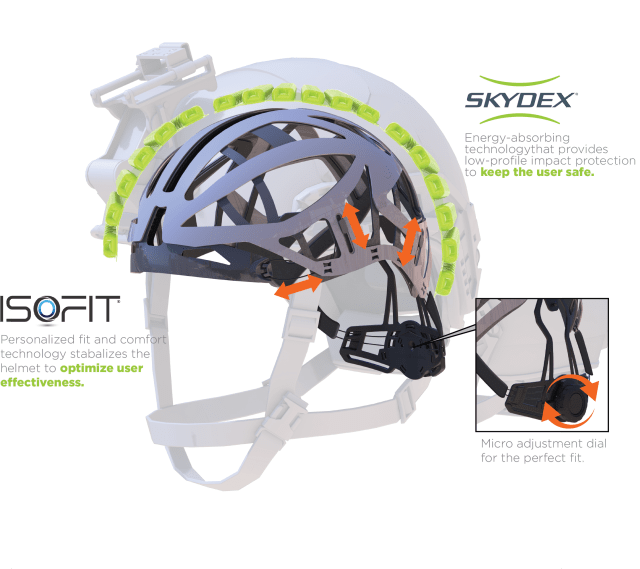
Traumatic brain injuries (TBIs) from high-impact sports like football have become a topic of great concern in recent years due to studies revealing their link to premature death. However, brain injuries incurred by military personnel are a longstanding problem that continues to affect vets long after they return to civilian life. It’s an issue that Denver-based SKYDEX has been working on for years by supplying shock-absorbing equipment to the U.S. military.
The company started 20 years ago, initially developing shock-absorbing material for Nike footwear before entering the combat supply field and developing products for U.S. Navy marine craft and blast mats for other military vehicles. From there, SKYDEX delved into helmets, bulletproof vests and bomb suits. With nearly 414,000 U.S. service members receiving a TBI diagnoses between 2000 and 2019, advancing helmet safety technology is receiving heightened focus.
The wars in Iraq and Afghanistan highlighted the need for more advanced protective equipment as troops were getting severely injured during vehicle bomb attacks. The U.S. military approached SKYDEX seeking blast mitigation technologies, and early product testing revealed an 80 percent improvement in injury rates. As a result, the government quickly became the company’s foremost customer with thousands of products supplied.
“Head injuries are very complex,” said Alvaro Vaselli, CEO and president of SKYDEX. “We need to continue to do more research and identify how different types of injuries occur and how to best protect against those injuries.”
Vaselli said the changing needs of military personnel and more complex combat technologies have also helped place the spotlight on helmet safety. For example, compared to the relatively simple helmets worn by soldiers in World War II and the Vietnam War, today’s troops need helmets equipped with night vision goggles, radio communication and other electronic devices that change the way helmets are worn and add considerable weight. That has warranted better impact materials, which are evolving alongside the other changes.
“The objective is to get troops to be ready for battle and perform at their best with all that equipment,” Vaselli said. “Weight is a big factor. Stability is very important in addition to protection, so that’s what we take into consideration when we work on different projects.”
He added that heat dissipation and comfort are other considerations that can’t be overlooked, noting, “It doesn’t really matter how protective a helmet is if the users don’t like it and won’t wear it.”
In addition to protection, SKYDEX helmets are geared to be low profile for absorbing more energy within less space, having an open airflow design for comfort, integrating with many helmet designs, and being antimicrobial, odor-free, flexible and durable.
Thermoplastic polyurethane, or TPU, is the basic building block that allows SKYDEX to develop helmet shock absorbers that balance all the factors that are frequently at odds with each other, most notably weight and volume. The key is manipulating the material into specific geometries that reflect the user’s need for impact dissipation, noise absorption, vibration attenuation and other specifications. The process begins with choosing among the hundreds of TPU family materials with varying degrees of hardness and density, then applying a target geometrical pattern to the material.
“The secret sauce of our company is the ability to translate the needs of a customer into a solution that is made with specific materials and geometries,” Vaselli said.
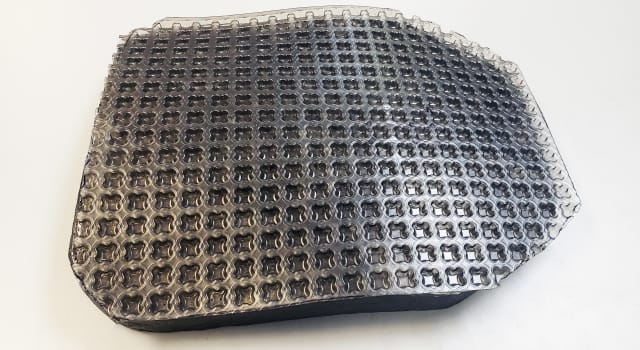
Although SKYDEX mainly works on custom projects, the work generally doesn’t start from scratch and follows its two decades of being in business. So, whether it’s vehicle blast mats, seats, marine craft decks, helmets, mattresses for barracks or ballistic protection, the company has sufficient institutional knowledge that can be slightly modified to suit users’ needs.
The U.S. military also has its institutional knowledge, and it’s currently being utilized by the Army Research Laboratory, which recently developed a rate-activated tether or RAT webbing system that suspends the helmet on the head.
“When you pull it slowly, it stretches and relaxes easily, like a rubber band,” Eric Wetzel, the technology’s lead inventor, told TechLink. “When you pull the RAT faster, however, it requires significantly more force to pull. The result is that a RAT-based suspension is forgiving under low-energy impacts, highly dissipative under high-energy impacts, and very efficiently uses the limited space between the head and the helmet shell.”
The technology is currently in the testing phase for potential use by soldiers, athletes, and construction and public safety workers. So far, it’s more effective than existing football helmets, reducing the risk of concussions from 0.66 percent to 0.11 percent. It was also used in parachute jump tests at Fort Brag in September 2021.
As the RAT system is very new, it’s unclear how it compares to SKYDEX’s helmet products or if the two could be used in conjunction. “It’s a very interesting innovation, but with all these types of new technologies, it comes down to how it’s integrated into the final product,” Vaselli commented. “It comes down to how you put it together with all the other components that need to work with each other.”
SKYDEX is beginning to venture further into the commercial market with its products in Timberland boots, sports equipment and consumer mattresses, where innovation is often needed. For example, SKYDEX spent nine months developing a protective case for a client’s expensive headphone product with a retail price of over $1,000. Given the project’s unique nature, the company did have to start from scratch in this case, Vaselli said.
Anything that needs impact protection is fair game for SKYDEX, with its motto of protecting people and things that matter.
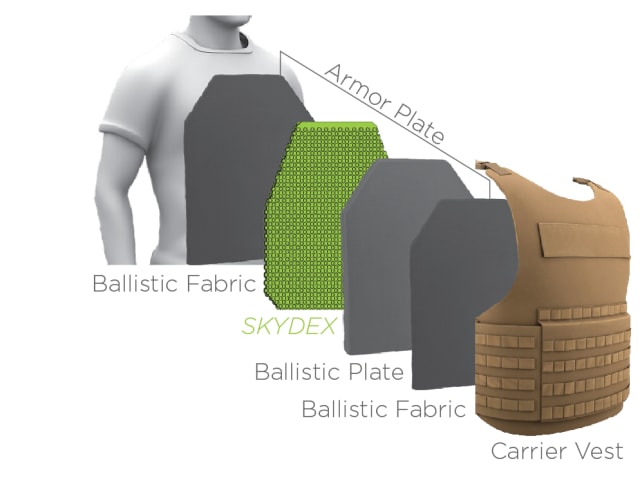
Generally, the company’s process involves a combination of computer modeling using historical data and trial and error. In addition, SKYDEX’s extensive lab facility allows for an iterative prototyping process that involves client feedback and performance testing. An array of products means that a multitude of regulatory standards must be met, including AR/PD 10-02 for combat helmets, AR/PD 14-01 for advanced combat helmets, EN 397 for industrial safety helmets, ECE 22 for motorcycle helmets, and ASTM F2040 for recreational snow sports.
“The data sets we work with are always related to some type of standard,” Vaselli explained. “We have to at least meet the minimum requirements, and we typically outperform the standards with materials using less space.”
SKYDEX’s impact mitigation technologies are continually evolving because every project requires some degree of innovation as different materials are combined with varying geometries. With patents on over 100 of SKYDEX’s original portfolio expiring, a new wave of another 100+ patents has been created in recent years that won’t expire until 2035 to 2037.
“We’re always evolving,” Vaselli said. “Data collection is important; monitoring of users is important. I think technology is helping with that now. We anticipate bringing together different types of technologies and materials to optimize the system. So, it’s really about working together—no one has every answer, so we need to integrate and evolve together.”
This fall, SKYDEX partnered with ArmorSource to enhance the company’s combat helmets with the SKYDEX IsoFit Helmet Protection System. The system features a micro-adjustment dial connected to a custom liner to better fit individual military and law enforcement personnel, impact protection using an energy-absorbing pad and open airflow.
“As a leading manufacturer of helmets, our mission is rooted in improving the survivability of military troops and law enforcement officers and ensuring our products represent the latest innovations for protection,” said Brad Grunden, president at ArmorSource. “By teaming up with the design experts at SKYDEX, we’re confident that this unique collaboration will elevate our company’s ability to leverage the most advanced technology for military and law enforcement organizations and help grow the business substantially.”