Are large-scale 3D printers the gateway to additive manufacturing in volume production?
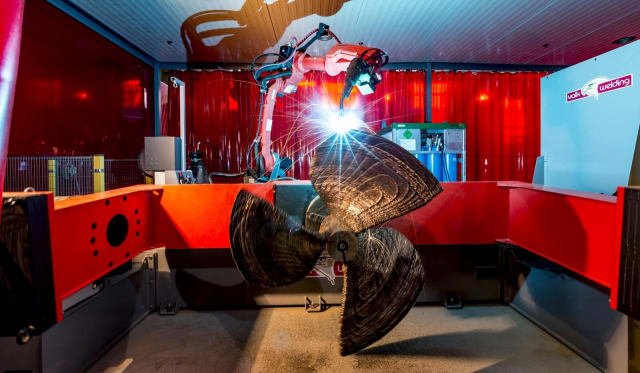
Wire arc additive manufacturing (WAAM) and big area additive manufacturing (BAAM) are two of the most common approaches for 3D printing at large scales, but they aren’t the only game in town.
In many ways, the state of large-scale additive manufacturing today resembles that of 3D printing more broadly at the turn of the millennium. In that bygone era, the excitement surrounding 3D printing as a production technology was almost palpable. The optimists dreamed of replacing turning centers, 5-axis machines—even whole factories—with nothing but 3D printers. As the fervor reached its peak, we seemed poised to enter a new age of additive manufacturing. Yet, despite all the enthusiasm, that revolution never came.
Now, you might claim that the fourth industrial revolution is still on its way, or that the use of 3D printing as a production technology is still growing, just not as quickly as initially expected. Hype is often the result of focusing on new technologies in the abstract without considering all the nuances involved, which naturally leads to overly inflated expectations. A better understanding of the underlying engineering tends to temper the hype.
Still, even if 3D printing isn’t going to supplant all of the more traditional manufacturing methods, it seems uncontroversial that additive manufacturing will continue to proliferate throughout the sector. Metal additive manufacturing has certainly made some serious leaps forward in the last few years, but rather than focusing specifically on materials, it’s worth considering an even more fundamental aspect of 3D printing: build volume.
Are large-scale 3D printers the gateway for additive manufacturing in production?
How Large Are the Largest 3D Printers?
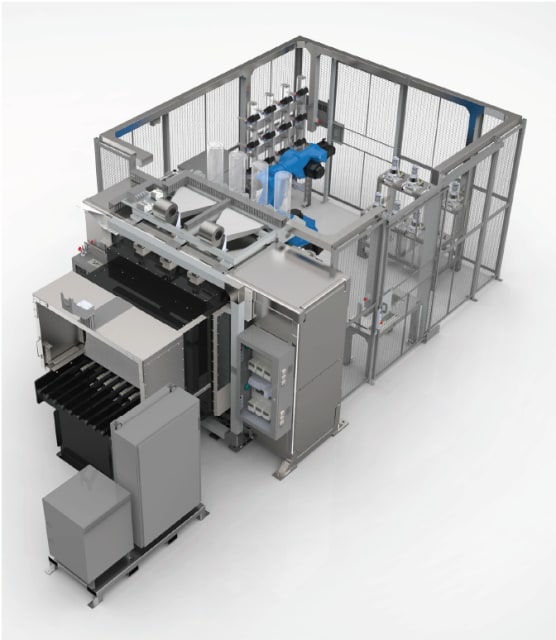
If we’re going to discuss large-scale additive manufacturing, we need to be clear on what that means. Stratasys’ H2000 was introduced at IMTS 2016 as the Infinite Build 3D Demonstrator. This machine holds the top spot for industrial 3D printers in terms of build volume, since it’s theoretically capable of producing parts with infinite lengths.
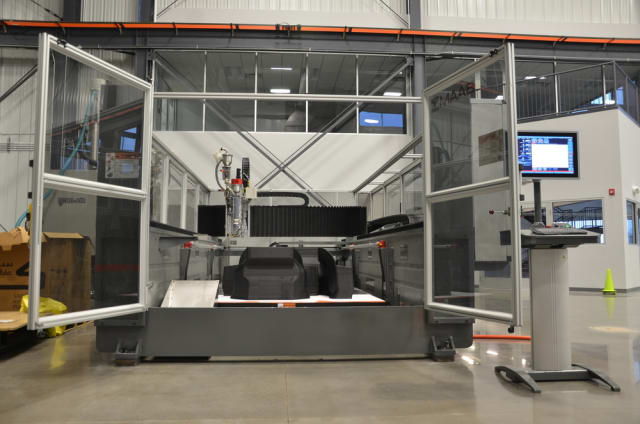
However, since you still won’t find it outside of a few pilot projects, a better candidate for defining the upper limit of large-scale additive manufacturing is the Cincinnati Incorporated BAAM system. BAAM systems are available in two sizes: 140 in x 65 in x 34 in and 240 in x 90 in x 72 in.

voxeljet AG’s VX4000 is another contender for largest industrial 3D printer—the company billed it as the largest industrial 3D printer in North America when it was installed at voxeljet’s Canton, MI facility in 2016. With a build envelope measuring 157 in x 79 in x 39 in, the VX4000 was designed for printing sand molds used in the casting of large components.
(There are several other 3D printers with larger build volumes than the BAAM and voxeljet systems—such as those of D-Shape and XtreeE—but since these are intended for construction, they lie beyond the scope of this article.)
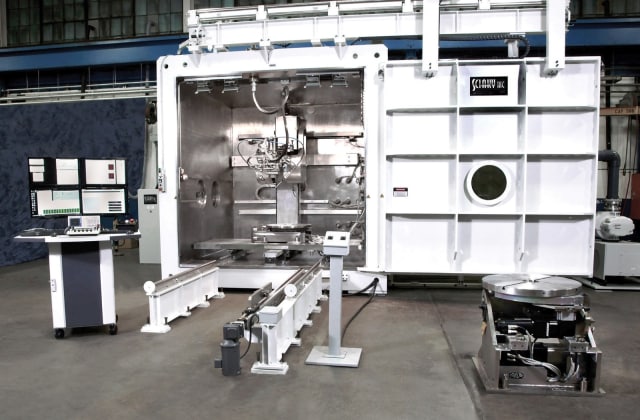
For metal 3D printing, the largest commercially available machine is Sciaky’s EBAM (electron beam additive manufacturing) 300 Series, with a build volume of 228 in x 48 in x 96 in. GE Additive’s Project ATLAS (additive technology large area system) is the largest powder bed fusion (PBF) system, at 43 in x 43 in x 12 in, but it’s still in beta testing. For the moment, the largest PBF machine is the Xline 2000R from Concept Laser, acquired by GE in 2016, at 31 in x 16 in x 20 in.
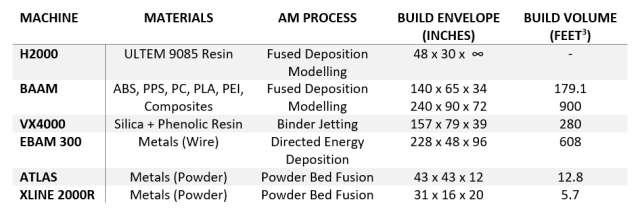
Setting a lower limit for large-scale 3D printing is more difficult. Desktop units—such as those from Ultimaker—obviously don’t count as large format, but what about HP’s Multi Jet Fusion series? Drawing a dividing line for metal 3D printing is even more challenging, since you don’t find the same radical differences in scale at the extremes—barring some unusual exceptions.
I suspect we have a bit of a sorites paradox on our hands. So, rather than setting an arbitrary lower limit on build volume, I propose to adopt the following 20-Questions-inspired convention: a 3D printer only counts as large-format if it can produce parts that are bigger than a breadbox.
This at least gives us a starting point from which to consider the focal question of this article: Are bigger 3D printers the way forward for additive manufacturing in production?
Types of Large-Scale Additive
There are several approaches to 3D printing at large scales, but they all involve either building bigger machines—such as the BAAM and EBAM systems—or mounting an industrial robot on a rail or gantry and equipping it with additive capabilities, as is often the case for WAAM.
WAAM
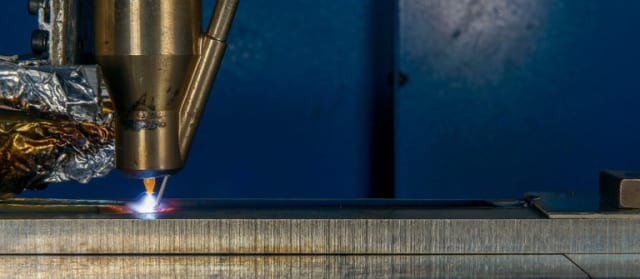
Wire arc additive manufacturing (WAAM) uses an electric arc as the heat source and wire—rather than powder—as feedstock. Peter Gratschmayr, senior sales engineer at Midwest Engineered Systems (MES), explained what distinguishes WAAM from other additive systems:
“This really doesn’t compete with other laser additive manufacturing technologies,” he said, “because those are meant for a higher definition, smaller component. It ends up costing somewhere between 12 and 25 dollars an ounce for the powder to be able to make the part, because there’s usually a 20 percent scrap rate that comes out of it, so not all the powder gets used.”
WAAM certainly qualifies as large scale; according to Gratschmayr, MES can make parts up to 42 m x 6 m x 2 m. It’s also useful for maintenance, repair and overhaul (MRO) operations, since it allows you to rebuild worn-out features on a damaged component by depositing new metal directly onto its surface.
One of the biggest advantages of WAAM is that it’s based on a manufacturing technology that’s been around for centuries: welding. In fact, WAAM hardware generally consists of standard, off-the-self welding equipment, including the power source, torches and wire feeding system. This makes it an appealing option for those who aren’t ready to invest in a standalone metal 3D printer, particularly if they already have experience with welding.
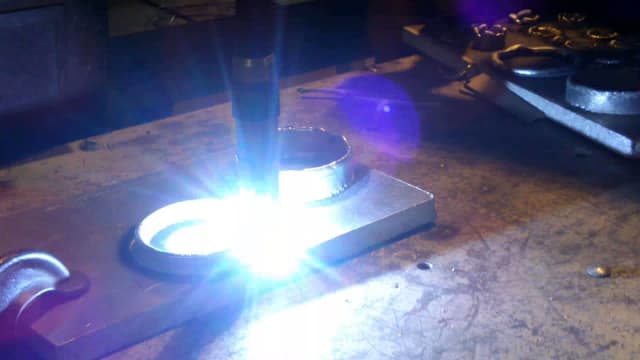
“WAAM is a different technology compared to other large-formats when it comes to materials (polymers vs. metals) and form (powder vs. wire),” said Vincent Wegener, managing director at RAMLAB, an additive manufacturing company focusing on WAAM in the marine market. “What [large-format 3D printers] have in common is the need to deposit a lot of kilograms per hour to be economically viable and most parts require post processing, in the form of grinding or milling, because you’re always depositing near net shape.”
BAAM
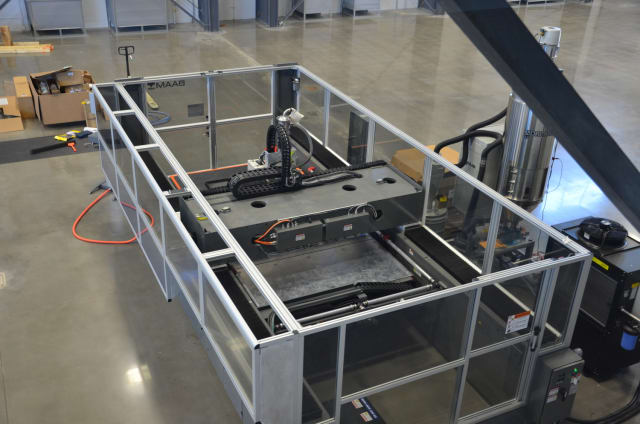
Perhaps the best-known example of large-format additive manufacturing, CI’s BAAM made a big splash at IMTS 2014, where it was used on-site to create the world’s first 3D-printed car in a joint effort between AMT, Cincinnati, Inc., Local Motors and Oak Ridge National Laboratory. In fact, the history of BAAM goes back further than that, as Rick Neff, additive manufacturing product and sales manager for Cincinnati Inc., explained:
“Lockheed Martin was trying to figure out how to make tooling out of plastics. They put an extruder on the end of a robot, but they were having trouble making that work. So, they went to the Oakridge manufacturing demonstration facility in Knoxville to work with Dr. Lonnie Love. They took the extruder off the robot and put it on a gantry they had at Oakridge that had been used for a couple of other projects previously—one was actually 3D printing concrete—and once they did, they were very quickly making pretty good parts.”
Despite this initial success—though perhaps not surprisingly—neither Oakridge nor Lockheed were interested in entering the 3D printer business, and so they needed a commercial partner. Cincinnati, Inc. was, in Neff’s words, “in the right place at the right time.” The company formed a cooperative R&D agreement with Oakridge to pursue BAAM technology, and that partnership is still ongoing today.
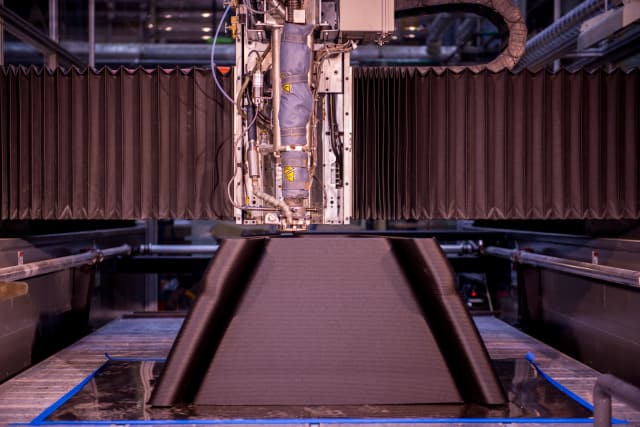
Given the use of robotics for WAAM, you might be wondering why Cincinnati and Oakridge opted for a gantry system instead. Neff explained that the decision was based on considerations of accuracy and simplicity:
“When you 3D print something, you slice it into horizontal layers and then deposit material in a plane to build those layers,” he said. “A robot’s first inclination isn’t necessarily to move in a plane; it’s really good at picking something up from one spot and putting it in another spot, but following an accurate path is more of a challenge. We need it follow that path at an exact speed to deposit the right amount of material, which adds another level of complexity to programming. Robots are really cool tools, but with an XY gantry, it’s a lot easier to move at an exact speed in an XY plane. We do that with laser cutting systems, for instance, and the BAAM is actually based off a laser cutting system.”
More Big 3D Printers
Although WAAM and BAAM are useful introductions to large-format additive manufacturing for metals and plastics, respectively, there are many other large-format systems and processes out there. For example, the Xline 2000R and the ATLAS both employ PBF, which is a common approach to 3D printing both plastics and metals. From a process standpoint, both machines are similar to Concept Laser’s other, smaller systems.
Some other large-format systems differ from their desktop counterparts not only in size, but technique. Three in particular are worth noting.
EBAM
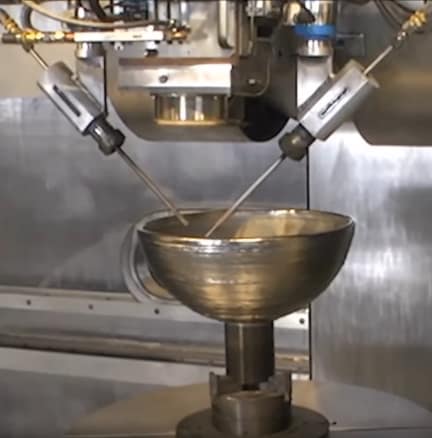
Despite becoming commercially available almost four years ago, Sciaky’s EBAM still holds the top spot for large-format metal additive manufacturing. Since then, EBAM systems have been utilized or purchased by major players in the aerospace and maritime industries, among others.
EBAM uses wire as its feedstock, making it more similar to WAAM than to PBF. However, whereas WAAM is most comparable to MIG welding, EBAM is closer to TIG welding, since the wire feedstock is combined with a separate heat source (in this case, an electron beam), rather than acting as an electrode itself. This process is more generally known as directed energy deposition (DED).
VX4000
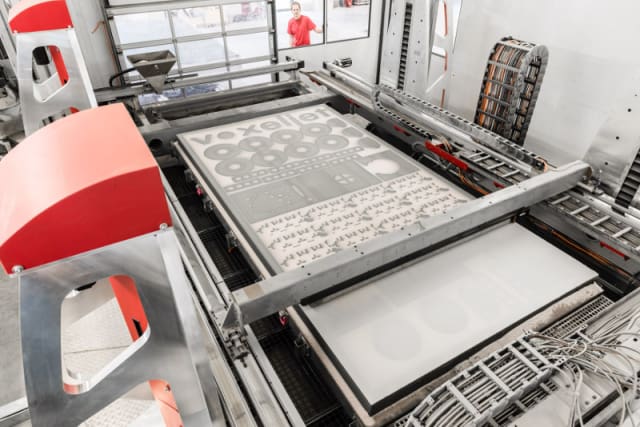
The VX4000 may not be the world’s largest industrial 3D printer per se, but it is the largest industrial 3D printer for sand molds. While it can be used to produce multiple molds for series components, the VX4000 was clearly designed with the production of large individual molds in mind. Rather than lowering the build platform with each new layer of the printer process—as is common in PBF—the print head and coater on the VX4000 are raised. This allows the machine to bear significantly more weight.
The printing process on the VX4000 falls under the category of binder jetting, in which a liquid binding agent is selectively deposited on a substrate in order to join the individual particles. In this case, the binding agent is a phenolic resin deposited by the print head and the substrate is raw silica deposited by the coater. According to voxeljet, the print head on the VX4000 is wide enough to print a complete layer in just two passes.
KRAKEN
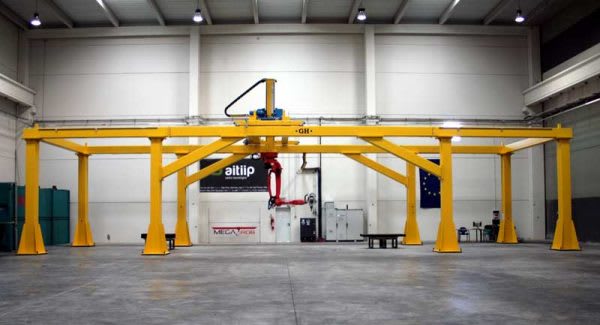
The KRAKEN project is probably one of the most exciting, yet least known developments in the realm of large-format additive manufacturing. Started in 2016, the project is a collaboration between six large companies, five SMEs, three research organizations and one industry association. Together, these groups are developing a large-format robotic cell that combines additive and subtractive technologies into a hybrid, multi-material system capable of producing parts up to 67 feet long.
Although the KRAKEN has already seen some use in production—including making a body-in-white for the Alfa Romeo 4C—the goal of the KRAKEN project is to use the platform to address a number of engineering challenges more broadly. For example, the KRAKEN currently utilizes an epoxy- or polyurethane-based thermoset resin, which the project researchers have learned to tune for ease of dispensing, sag resistance and other desirable properties. You may not find a KRAKEN on the average shop floor anytime soon, but as an exemplar of the capabilities and challenges of large-format additive manufacturing, it’s certainly noteworthy.
Large-Scale Additive Materials
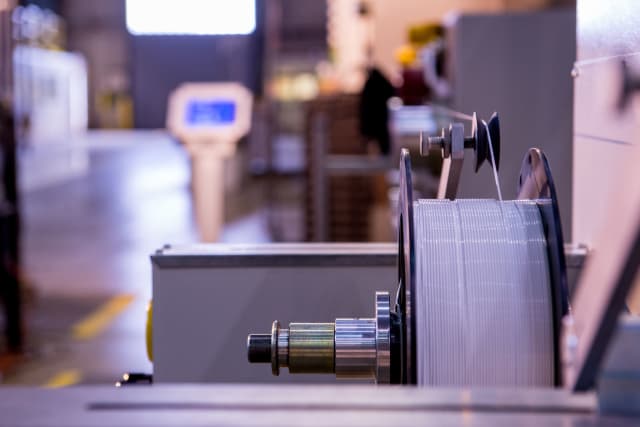
Thus far, this article has been essentially agnostic on additive materials—there are large-format 3D printers for metal, plastic, sand and other materials as well. In the case of powder bed fusion in metal additive manufacturing, the same feedstocks that run on Concept Laser’s smallest machine—the Mlab Cusing, with a build volume of 1 ft3—also run on the Xline 2000R. This is due to the strict environmental controls involved, and the relatively small difference in build volume.
Controlling the material properties for WAAM presents a significant challenge, as Wegener noted. “It comes down to controlling the heat input in your material,” he said. “We are tackling this problem at the moment in our lab.”
For plastics, the material differences between large-format 3D printers and desktop 3D printers are considerably larger. Both the Monoprice Select Mini sitting on my desk at home and BAAM are capable of printing ABS, but it should come as no surprise that the requirements for each machine are radically different.
As senior business manager, additive manufacturing for SABIC’s Specialities business, Keith Cox is well acquainted with the nuances of large-format additive materials. It might seem as though large-format machines would be able to use the same resins as smaller 3D printers, or even those used in injection molding. However, as Cox explained, there are good reasons to avoid doing so:
“In general, the highest level of part performance is achieved when the material formulation is optimized for the unique characteristics of a specific conversion process,” he said. “For example, injection molding is a high temperature, high pressure, low residence time process. By comparison, industrial fused deposition modeling in an enclosed build chamber may process at similar temperatures as injection molding, but the residence time can be much longer and there is relatively little pressure applied to form the part.”
“Large-format additive manufacturing processes operate at high temperatures but print in near ambient conditions, effectively resulting in short exposure to high temperatures and relatively fast cooling rates,” Cox continued. “To optimize part performance, the material should be formulated to withstand the unique environment of each process. This may require changes to material composition, rheology, reinforcements, or other characteristics that influence flow, inter-layer adhesion, shrinkage, etc.”
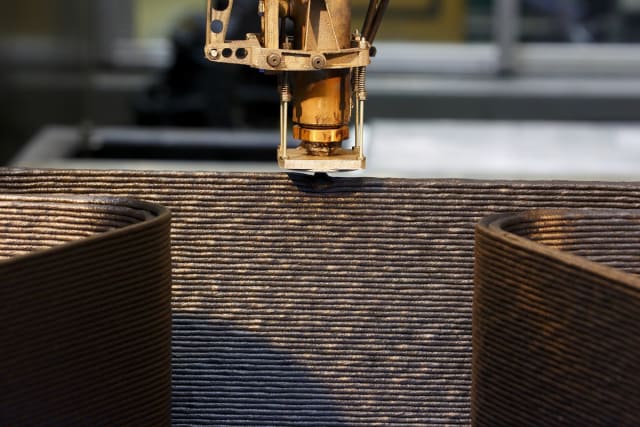
The material challenges of large-format additive manufacturing are the logical consequences of it being large format, i.e., printing in ambient conditions, high rates of material deposition, managing cooling across comparatively long distances and, often, producing parts with no support structure. For this reason, feedstocks that have been specifically designed for large-format—such as SABIC’s THERMOCOMP compounds—are becoming more common.
Large-Scale 3D Printing Applications
We can discuss specs and materials until the cows come home, but to really get a sense of what large-format additive manufacturing is capable of, you need to look at the applications. There are many use cases for large-format 3D printers, but even a few should be sufficient to illustrate their capabilities.
Local Motors
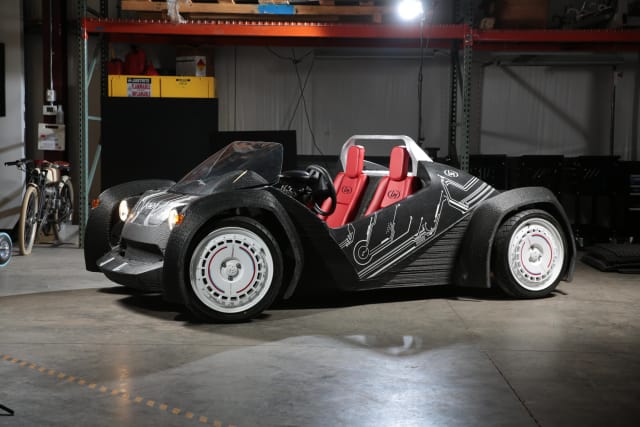
“Our first commercialized vehicle that’s using large-scale additive parts is Olli,” said Gregory Haye, general manager of LM Industries, Inc. “Some of those parts are performing structural duties, while the majority are providing a combination of cosmetic and structural combined. They’re carbon-fibre-reinforced ABS plastic.”
In total, additive parts account for 30 percent of the weight of the vehicles deployed in Local Motors’ pilot programs, but the contributions from its two BAAM systems don’t stop there.
“In the same vehicle program, we’ve also demonstrated 3D-printed tools for molds for thermoforming plastic body panels for the vehicle’s interior,” Haye said. “And if it’s going to be for a short run or we need to make the next iteration of it, that tool can be ground up, recycled and printed again.”
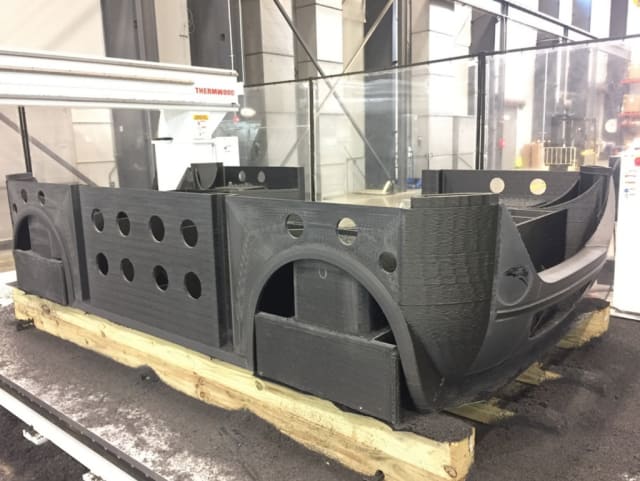
In comparing BAAM to other, more conventional manufacturing processes—such as machining and injection molding—Haye emphasized the design and iteration flexibility that comes with using large-format additive manufacturing. “With every other process there’s the required design and tooling manufacturing, as well as a pretty extensive lead time. To produce your first article, you might have a design and manufacturing process that takes four to eight weeks to get your first mold and be able to pull a part. We can design a part in CAD, print it and have that first article in two days with some finish.”
Compared to other additive processes, Haye noted the high deposition rate as the principal advantage of large-scale 3D printers. “When you compare it to a desktop unit or any of the powder bed variants, the cost of the commodity itself is higher and the process time is so much higher by comparison of throughput per hour. If you get to deposition rates of 200 pounds per hour, you can print a vehicle chassis in half a day.”
RAMLAB
Based in the bustling port city of Rotterdam, RAMLAB is working on a better way to source large, expensive marine parts, such as propellers. “Often you have to order more than one part,” said Wegener. “You have a large batch that you keep in stock. Warehouses in port at Rotterdam are filled with parts that are sometimes never used. This is a waste of energy and resources.”
RAMLAB worked as part of a consortium to develop a large, bronze propeller using WAAM. You can learn more about the project in the video below:
Wegener agreed with Haye on the benefits of added design flexibility that come with large-scale additive manufacturing. “You have to rethink the actual function of the part. Most of the time it’s optimised for instance for casting, which means concessions have been made on the design of the part,” Wegener said. “For example, we are now working on a hoisting hook, which is normally casted and fully solid. With WAAM, we can make the prongs of the hook hollow, reducing production time as well as weight.”
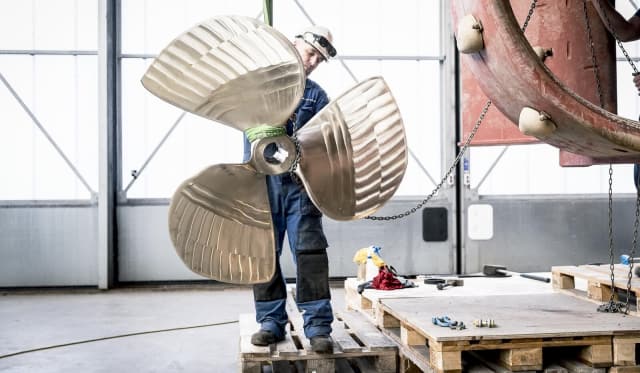
Certification is a major hurdle for any new production method, including large-scale additive manufacturing. That’s part of what makes the WAAMpeller project significant: “We have already proven with our WAAMpeller that certification of parts made with WAAM is possible,” said Wegener.
Roush
Roush, which engineers high-performance automotive components, recently purchased an Xline 2000R. “We’ve been providing 3D printing services for over 15 years, mainly in plastics—stereolithography, optometric laser sintering, Objet printing, fused deposition modelling—but we’ve also had an EOS M 290 for about a year and a half,” said Brandy Badami, business development director for additive manufacturing at Roush. “We had experience with additive, just not on such a large scale for production applications.”
The company’s previous experience with additive—combined with aid from GE Additive—made the installation relatively straightforward. However, it did take time to adjust to the difference in build volume, as Badami explained. “The most time-consuming part of the process was parameter development of the mechanical and metallurgical properties that went along with a new large-format machine.”
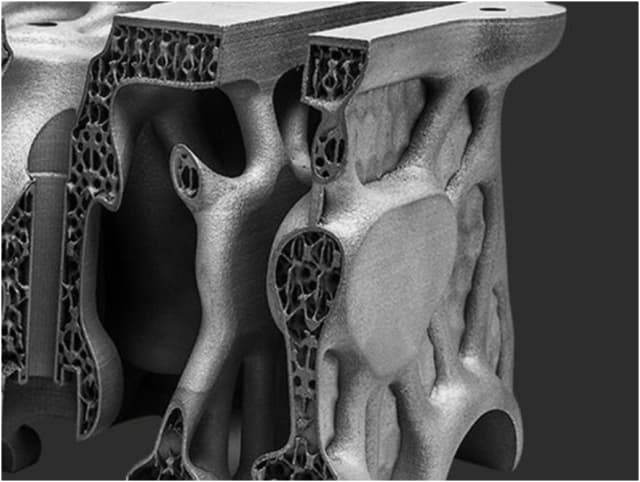
In Roush’s case, it was worth it. “We needed to print big parts, and this was the only machine on the market that was large enough to print the components that we needed,” said Badami. “We had a few specific applications in mind, such as cryogenic propulsion systems, lightweight vehicle structures and complex components. Once we became familiar with the equipment, we recognized that it would open doors for other opportunities in applications for 3D printing.”
For Roush, the biggest advantage of having a large-format 3D printer is being able to deliver parts faster, and at lower cost than their competitors. “Time is definitely of the essence when it comes to product development. Having these additive manufacturing capabilities—especially when the components are designed with additive in mind—can greatly reduce cost and lead time,” said Badami.
Large Scale Additive vs. Desktop 3D Printing
It should come as no surprise that large-scale 3D printers have many of the same advantages as their desktop counterparts, such as greater design flexibility and shorter lead times. But how do these additive behemoths compare to their diminutive predecessors? If we accept that 3D printing is not only here to stay, but also still growing, the question is whether the proliferation of additive manufacturing for production is more likely to come in the form of individual large-scale machines, or collectives of smaller, even desktop-sized 3D printers.
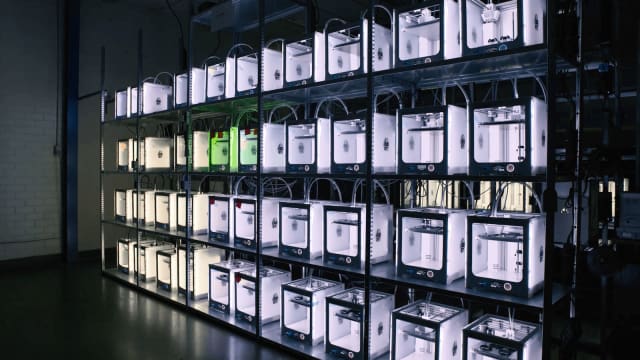
The latter option has certainly been popular with the rise of on-demand manufacturing. Of course, large-scale 3D printers could find a home in this niche as well—Local Motors is essentially an on-demand automaker. John Kawola, president of Ultimaker, North America, had the following suggestion for understanding the relationship between large-scale and desktop 3D printers:
“Sometimes people in this industry draw an analogy between 2D printing and 3D printing. People have 2D printers on their desks that print letter-sized sheets of paper. Large-format 2D printers don’t print lots of letter-sized sheets, they print large posters, banners, maps and drawings, so you need them to be that big. It’s interesting to think about large-format and standard 3D printers in this way.”
In other words, if you need to print large parts, then you need a large-scale 3D printer. “Piecing things together, gluing them together—it’s not really practical in prototyping, so it’s definitely not going to be practical in production,” Kawola said.
Of course, large-format 2D printers aren’t designed to print multiple letter-sized sheets of paper, whereas large-scale 3D printers are more than capable of printing multiple smaller parts simultaneously. That option is explicitly cited for the VX4000, and some metal 3D printers already offer dual laser setups that allow two parts to be printed simultaneously. Could this approach—coupled with the high deposition rates of large-scale 3D printers—give additive manufacturing a way to produce parts at rates comparable to more conventional processes?
Kawola was skeptical, at least for some additive processes.
“Let’s say you have 20 Ultimakers vs. one large machine. The 20 Ultimakers will be faster, especially the way FDM fundamentally works. Because you’re extruding material through a nozzle, producing two parts on a machine will take roughly twice as long as producing one part. So, you’re better off having multiple small machines because that essentially gives you multiple nozzles, and you also have the benefit of redundancy.”
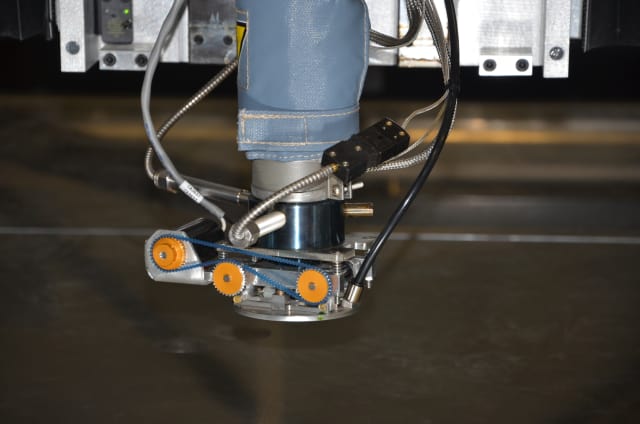
Nevertheless, there are some applications where large-scale 3D printers edge out their smaller competition—not just for end-use products, but in production as well. “Large format additive manufacturing is truly a nascent industry, but it may have already identified its first ‘killer application’ in printed tooling,” said Cox. “In markets where small unit builds have typically made traditional tooling construction cost prohibitive, LFAM has demonstrated the ability to deliver value to customers by balancing system cost and production speed.”
Large-Format Additive Manufacturing
Despite what fast food franchises, HD TV retailers and Hummer salesmen would have you believe, bigger isn’t always better. The answer to the question of whether large-scale additive manufacturing is right for your application depends on your answers to a host of other questions.
Many of these are the same ones that anyone interested in 3D printing should ask, but a difference in size also makes a material difference to how you should approach this emerging technology. A large-scale 3D printer may not be your best option for making end-use parts, but it could be a good way to improving your tooling efficiency.
If you are considering large-scale additive manufacturing, Badami had a key piece of advice:
“Make sure the machine will fit through the door.”
Do you believe large-scale 3D printing will disrupt manufacturing or remain a niche technology?
Comment below.