For choosing the right combination of hardware and software, order matters.
Verisurf has sponsored this post.

There are best practices for selecting software, and that includes measurement and inspection solutions for manufacturing enterprises. Too often, manufacturing companies either minimize the importance of measurement and inspection software or, worse, they make purchase decisions based on hardware features that may or may not provide the results they need.
Only after taking delivery and using the equipment do they realize they have purchased software that is not up to the task, or the wrong type of coordinate measuring machine (CMM) for their workflow and the results they require.
The goal of this article is to help you avoid making the same mistake, through a comprehensive approach to software selection with critical consideration given to needs assessment, compatibility and extensibility. If you have a clear perspective of your needs and a better understanding of what questions to ask and what features to insist upon, the result will be a grounded solution that provides results, enhanced workflow and added value across your manufacturing enterprise.
Assessing Needs and Communicating
You have probably heard it said that if you don’t know where you’re going, any road will take you there. This holds true for selecting the right measurement and inspection software for your business, as well. Before purchasing any software, regardless of application, you need a clear assessment:
- What problem or opportunity are you addressing with technology?
- How are you getting the data you need, today?
- What is your workflow?
- What benefits will be expected from your new software?
- Most importantly: Who else in the organization will be affected?
When it comes to measurement and inspection, there are a few considerations that are overlooked surprisingly often. These include identifying the maximum part volume to be measured, understanding the number of measurement points needed to calculate results and the speed required to complete the measurement process. Failure to consider these points may lead to a solution that is inefficient or, worse, one that does not support a critical workflow.
Here’s what you don’t want to do: see an impressive CMM and buy it based on a demo, possibly unrelated to your workflow or measurement objectives, then try to justify why it is the best solution for your organization.
That’s putting the cart before the horse.
This is why clear communications should start with your assessment and carry through the balance of your technology acquisition and implementation. You might be surprised how many people in your organization can be positively impacted by data gleaned from measurement and inspection software.
Investing in the right set of tools can mean using that data for quality inspections, reverse engineering, recreating data for missing features, support for tool making, and guided assembly of components, fixtures and weldments. Collected data can feed downstream applications, such as Product Lifecycle Management (PLM) or Statistical Process Control (SPC) databases. Understanding who the stakeholders are and keeping them in the loop can add a great deal of value to your software.
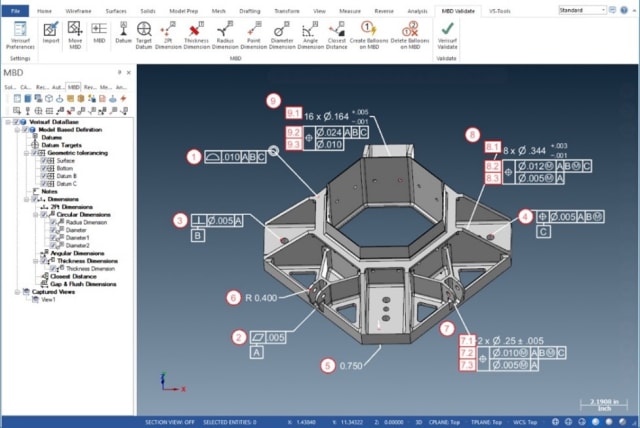
Tip #1 – Make a CAD Connection
In today’s business environment, every software platform must play well in the sandbox with already-established enterprise software or protocols. For business intelligence, this may be enterprise resource planning (ERP) software. For business communications, it might be Microsoft. Within the manufacturing enterprise, the standard is CAD.
Finished products and components are typically conceived in a CAD environment and, for most manufacturers, they remain in this virtual state throughout the design-build process. Data continues to be added to the file and its digital references throughout the lifespan of the product.
Model-Based Definition (MBD) is the term given to this commitment to an intelligent CAD model. The central concept embodied in MBD is that the 3D model provides all the detailed product information necessary for all aspects of the product life cycle. In the example of a machined component, this would include intelligent Geometric Dimensioning and Tolerancing (GD&T) annotations.
This removes the ambiguity, conflict and doubt that arises when drawings and models co-exist. By bestowing authority on the model, MBD eliminates errors that result from referencing an incorrect source and makes processes more efficient—no more searching to determine correct revision levels.
When selecting measurement and inspection software, make sure that it not only is compatible with CAD but is CAD-based at its core. A good question to ask is, “Does this software include intelligent 3D CAD modeling capabilities?”
A truly CAD-based platform is the best way to ensure data continuity (digital thread) and maximize model-based measurement and inspection applications across your manufacturing enterprise. Even if your organization is not at the point of fully embracing MBD, you want software extensibility and room to grow.
Tip #2 – Ensure Software Compatibility
If you make CAD-based measurement and inspection a requirement and do your homework, you’re already halfway covered with respect to compatibility. The CAD connection will allow you to import, edit, save and export to and from virtually any CAD software.
This is important when it comes to creating inspection plans that might have missing GD&T data that needs to be added, or when using reverse engineering to fill in missing features.
Having an open CAD platform from which to operate and manage your measurement and inspection applications makes downstream integration and data sharing much easier with common file types and established transfer protocols.
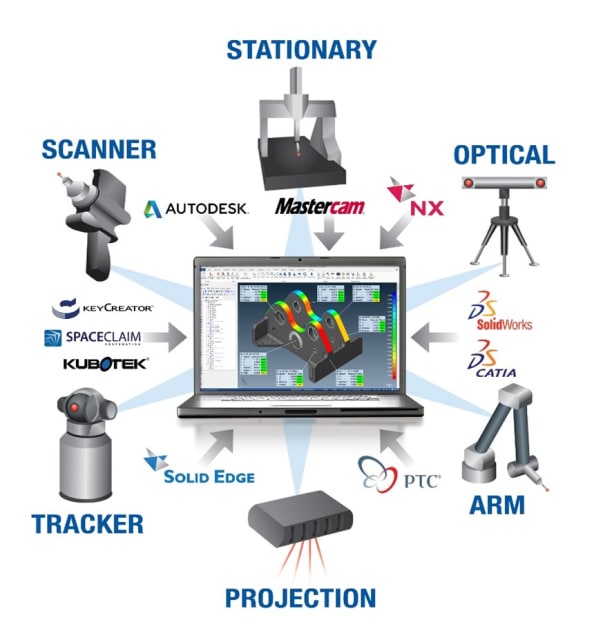
Tip #3 – Don’t Forget About Hardware Compatibility
There are many types and brands of CMMs available on the market and if you remove the software from the equation, they all do one thing very well: collecting precision measurement points.
The power behind all CMMs—contact and non-contact, fixed and CNC-type, portable arms, trackers and more—is the applications and workflow provided by the supporting software. Most CMMs come with some sort of measurement and inspection software, but these are by CMM manufacturers, not software developers.
CMM manufacturers tend to be product-centric when it comes to software, focusing only on their machines. It is for this reason that you need to keep your evaluation of software and hardware separate and stay true to your assessment plan.
Consider your workflow and corresponding software applications first. This will lead you to the correct type of CMM you need before deciding on a brand of CMM.
When looking at measurement and inspection software from a hardware compatibility standpoint, it is important that the software can drive all CMMs and import measurement points in real-time. This is especially significant when collecting and processing very large measurement sets encompassing millions of measurement points, typically associated with non-contact scanning of large complex surface profiles. The software must be able to keep up with that influx of data or your productivity will grind to a crawl.
Universal device compatibility is critical when it comes to measurement and inspection solutions for a manufacturing enterprise. In the case of inspection, workflow routines should be able to be programmed once and then executed using any available CMM. This provides flexibility and consistency among operators and ensures repeatable process control is maintained, which is a key tenant of quality management.
Tip #4 – Ask About SDKs for Integration
Selecting a measurement and inspection software that is based on an open platform with built-in compatibility and interoperability is critical to advancing the concept of the digital thread.
To be effective, each step of the design/build process must play its part to stay connected. Data in, data out, and the ability to pass information across all manufacturing applications and databases are important. A good question that will confirm a software’s commitment to interoperability is, “Do you offer a Software Development Kit (SDK).”
If the answer is no, integration might be harder than you think.
Tip #5 – Remember Training and Maintenance
Training and compatibility go together.
Over the last 10 years, there has been a surge of shops adding portable measurement and inspection assets. These newer devices are based on open software compatibility, but many of the legacy CMMs that are still in use are based on closed systems and require dedicated software to run them.
This has created a dichotomy in some shops between new and legacy systems. Certain quality inspectors are trained to operate legacy machines and others are versed in newer equipment. This causes bottlenecks due to inefficient resource utilization.
Your software selection should be enterprise-based: one software to drive all your CMMs (regardless of type or age), manage workflow and provide your desired application results. This will help with resource utilization, reduce bottlenecks and lower software training and maintenance costs, since you don’t have to support more than one platform.
Bonus Tip – Ask for Help
When it comes to selecting inspection and measurement software, getting it right is important, so don’t be hesitant to ask for help.
Software and hardware providers alike should be willing to take an interest in your business and help you put together the right recommendation for your unique application. Just try to remain objective and stick to your goals.
There are many measurement and inspection solutions available, so hold out for the one that fits your needs.
Learn more at Verisurf Software.
About the Author
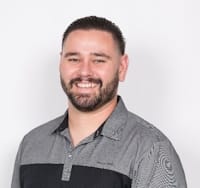