From a PLM standpoint, shipyards require a combination of enterprise capabilities to support product development, material handling, inventory management, process coordination and scheduling.
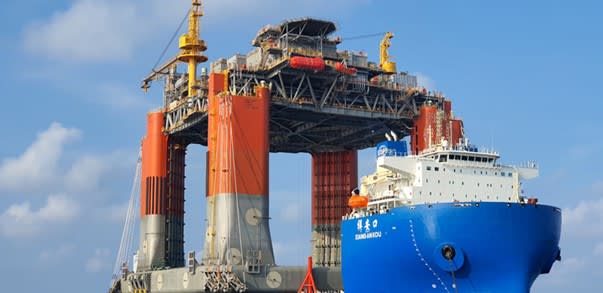
As announced in April 2024, Dassault Systèmes, HD Hyundai Heavy Industries Co., Ltd. and HD Korea Shipbuilding & Offshore Engineering signed a memorandum of understanding (MoU) for HD Hyundai’s Integrated design-production platform. The three organizations aim to “establish an integrated platform for design-production based on virtual twin technology, enhancing production efficiency, and fostering innovation.” With a total workforce of about 14,000 people, HHI operates globally across three business units: shipbuilding & offshore, naval & special ships, and engine & machinery.
“We aim to firmly establish the foundation of a Smart Shipyard by building and operating a digital twin based on 3D and digital assets, rather than past design methods,” said Seungho Jeon, Chief Technology Officer of HD Hyundai Heavy Industries. Taejin Lee, Director of Digital Transformation Innovation at HD Korea Shipbuilding & Offshore Engineering, said the shipbuilding production site, where every vessel is custom produced according to customer orders, is the optimal place where the ultimate goal of the fourth industrial revolution, mass customization, should be realized.
The marine and offshore industry is composed of multiple interrelated sea-related segments, bringing together multiple trades and supply chains. This post elaborates on how product lifecycle management (PLM) and related digital solutions, such as Dassault’s 3DEXPERIENCE, support the drive towards smarter shipyards.
How digitalization enables the future of shipyards
By design, shipyards are heavy industry building sites combining multiple trades and contractors. They are constructed near the open sea or rivers to allow for easy access and sea transportation of supply and final finished good delivery. The shipbuilding, marine and offshore industry is very global and competitive, addressing very niche demands and markets. The effectiveness of a shipyard, particularly in terms of material flow from the stockyard to the building berth, is a critical factor in overall productivity and efficiency. Shipyards are typically tailored to the ship size, ranging from small vessels to large super-tankers, from commercial vessel series to one-off military frigates, each with unique requirements and facilities.
The potential for digitalization and smart automation for maritime companies is significant. The shipbuilding sector remains to-date very document-driven with a lot of information being created and managed across product development and production stages, and shared across suppliers, owners and operators. Digital Twins, or “virtual twins” as Dassault Systèmes like to refer to them, have a great potential to augment master digital data models to combine mechanical/electrical hardware and software with other cyber-physical systems such as propulsion control, heavy duty equipments, or dynamic positioning of the ship.
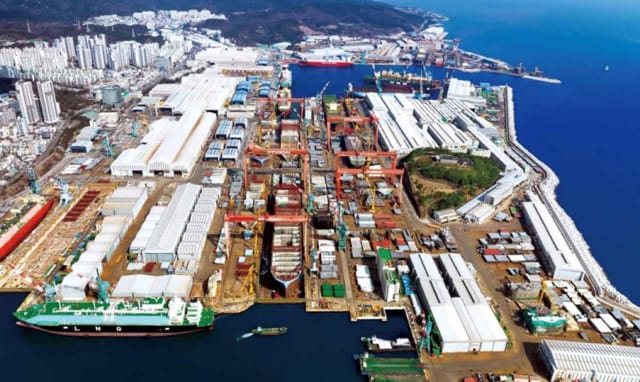
A vision for the “future of shipyards” has been elaborated in a 2020 research report published by EcoProdigi as the road to shipyard 4.0, promoting a policy-innovation roadmap for digitalising eco-efficiency shipbuilding operations. The roadmap was composed of 20 elements, from real-time digital planning to welding simulation and real-time monitoring, smart processes and documentation, contractor management, ship hull coating paint optimization, task management improved by augmented and virtual reality, 3D simulations and digital asset-driven inspection, AI-driven warehouse inventory control, additive manufacturing for spare part 3D printing, etc.
Why Digital Twins in the shipbuilding industry
More specifically, the EcoProdigi report discussed why Digital Twins and 3D imaging technologies can drive value when used for virtual inspections, both at the time a ship is delivered, as well as during retrofitting and maintenance: “Many modifications to- and deviations from- a ship’s original design are made during construction. This results in the reality that a delivered ship never has the exact specifications as initially planned. […] In such instances, shipyards are required to re-work the plan and begin producing the parts when the actual ship comes into the yard, resulting in expensive delays. Creating a Digital Twin of the ship as it is being constructed would give shipowners and yards better starting points for planning retrofits and rebuilds.”
From a PLM standpoint, shipyards require a combination of enterprise capabilities to support product development, material handling, inventory management, process coordination and scheduling, component tracking, workflow integration across supply chains and partners, stockyard layout management, path optimization, waste identification and reduction, and cross-functional data analytics. Leveraging smart automations requires a solid data backbone for product visualization, virtual vessel building and operations, democratizing cross-functional data analytics—including leveraging new technologies like Artificial Intelligence (AI).
Digital Twins can help drive green innovation and sustainability, with for instance electric propulsion systems, low emission fuels, autonomous ships, connected fleet management systems, advanced material utilization to enhance product performance and efficiency. Digital Twins and BOM modularity can facilitate organizations to become product-driven rather than document-based, leveraging integrated change management, product platforms and variants, facilitating template-based personalization—from customized vessels to specialized offshore solutions such as wind farms or mining platforms.
What can HHI expect from 3DEXPERIENCE
Over the years, Dassault Systèmes developed a range of industry-specific best practices that helps manufacturers becoming data-driven—leveraging learning across industries. The French software editor supported the NAVIAS project (New, Advanced and Value-added Innovative Ships) which initiated in 2018 and completed in 2022. The European research initiative brought together 18 organizations around the “challenge of developing a platform-based modular product family approach for shipbuilding.” It mobilized shipbuilding manufacturers like Damen Shipyards, universities and research institutes, technology and engineering suppliers, marine and offshore associations took part in the initiative.
The 3DEXPERIENCE platform was used in the co-development of modular solutions to facilitate ship design and manufacture. “The project aimed to improve the design standardization and the design reuse capability focusing on ship energy efficiency to minimize the design impact on the environment.” Among other things, the project built on the Model-Based Systems Engineering (MBSE) methodologies and Digital Twins strategies developed and adopted more commonly in the automotive, aerospace and defence industries.
“HD Hyundai Heavy Industries is driving the establishment of a Smart Shipyard under the vision of Future of Shipyard (FOS) […] Through collaboration utilizing Dassault Systèmes’ excellent integrated 3DEXPERIENCE platform, we hope to expedite the achievement of HD Hyundai Heavy Industries’ goals,” said Seungho Jeon.