Catia CEO Olivier Sappin explains how Catia is evolving to meet today’s engineering needs.
CAD software has changed a lot in the nearly three decades that Olivier Sappin has been working on Catia, the software that launched developer Dassault Systèmes. Now serving as Catia’s CEO, Sappin is in the driver’s seat for the changes to come. And there are some big changes coming.
Engineering.com sat down with Sappin to chat about Catia and how it’s evolving for today’s engineering challenges. He’s got grand plans for AI, a three-pronged approach to sustainable product design and a clear vision of the longstanding Catia brand—it’s no longer just for CAD, but for engineering at large, he says. Here’s why.
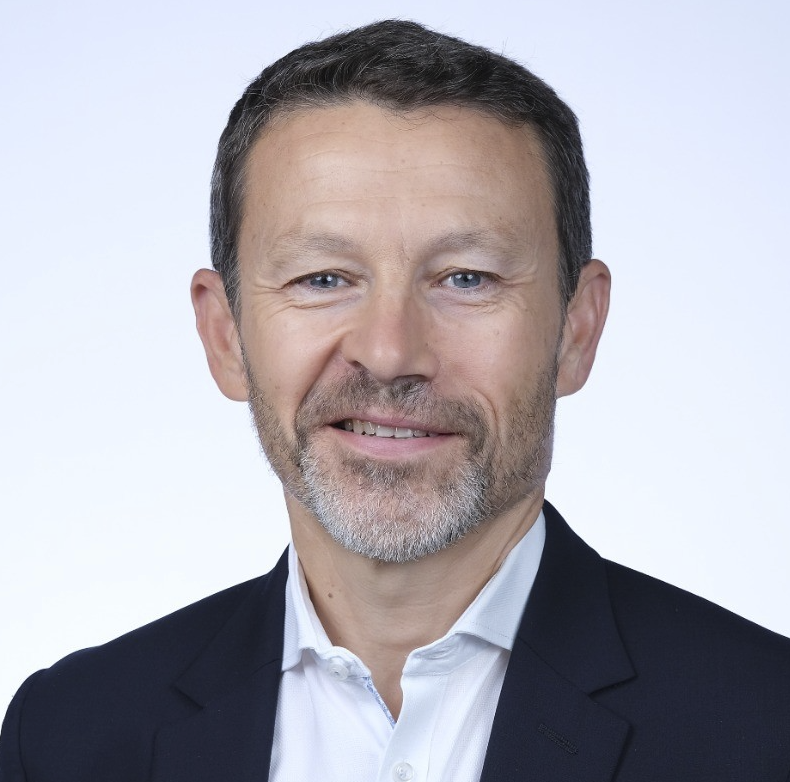
The following transcript has been edited for brevity and clarity.
Engineering.com: What excites you most about Catia these days?
Olivier Sappin: When I started it was really an exciting time. We were just working with Boeing to do a full digital aircraft, the 777, which was a complete digital twin. And at that time we decided not only to do engineering, but to expand on full PLM manufacturing. We decided that we would revolutionize the way people are doing product innovation.
Catia v5 was one of the first systems to enable our clients to capitalize their knowledge and know-how. And it resonates a lot today because the companies that work to capitalize all their knowledge will be the ones to take the most advantage of AI.
Without data, you cannot activate AI. ChatGPT works because it can run on billions of pages of text, images. You cannot find 3D assets on the web. You cannot type 777 and get the digital 777 because the IP is at Boeing.
So it’s a real advantage to have capitalized this knowledge and know-how. And that’s the main thing happening in Catia right now, to leverage artificial intelligence having the capacity to elevate our client’s data into real knowledge and know-how.
And by the way, this is why Catia runs on the platform. We are not running on files anymore, because the files are on everyone’s desktop or laptop and you cannot leverage them. So Catia on the 3DExperience platform on the cloud is definitely the way for our clients to get their data elevated to real knowledge and know-how that they can leverage for getting the most advantage of artificial intelligence.
Could you give any examples of how your customers have been able to use AI?
We’re actually working with key clients in the automotive, aerospace and other sectors. I can give you some examples but I cannot mention names at this point.
I’ll give you one typical use case. I’m working with a Japanese client and they want to automatically assemble all car components into a full virtual tree. And believe me, it still takes a lot of time. Let’s say engineers want to assemble a suspension. They need to take the spring of the suspension, the knuckle, the different parts. They need to get the knowledge about where this part is being assembled. They want to check new components, they want to validate the kinematics, they want to validate the NVH durability, they want to do a lot of simulation and it takes a lot of non value added tasks for them to rebuild that.
So with AI, we have been able to basically look after all the components of these clients and learn from past assemblies to automatically identify the functional area of the part, the one that helps to be connected to another part. And the system learns and automatically creates an assembly for the engineer. You can save a lot of time and you can imagine that with that you can potentially explore much more innovative ideas.
So it’s not only a time reduction, cost reduction, which is obviously an objective. But it’s also, within the same amount of time, how much space of possibility can you explore? To imagine, for example, a new car platform, to have an electric motor or battery and so on. And this is extremely helpful to accelerate innovation.
Another use case is to leverage natural language to interact with Catia. We think that asking direct questions to the system will be more and more common, so we are already testing about 50 to 60 different large language models to evaluate what would be the most beneficial to basically talk to Catia in natural language. So you can imagine that in the future you have a kind of assistant that will augment engineers.
How will that work? Instead of clicking and typing will users simply tell Catia to, say, sketch a circle with a diameter of 10 millimeters?
Yes, but not only that. We think that if we want to go to natural language, it’s not only to speak the language of the system. When you say please do me that sketch, it means you’re already a designer, because you know what a sketch is. And maybe some engineers don’t know what a Catia sketch is because they don’t know Catia.
So you potentially ask questions in the Catia language, but you would also be able to ask questions in the automotive language. ‘Please can you propose me a vehicle architecture that fits 5 passengers for a mid-size minivan in Korea?’
And so we will leverage the company know-how, but also what’s on the Internet. So, for example, you can find automotive handbooks, you can find regulations. If you want to develop a car for the U.S. market, for the dimensions of the car there are some boundary conditions to take into account which are declared in norms and regulations.
So AI will both use this type of regulation and academic knowledge plus the knowledge of the company, because each automotive OEM has developed cars for many years. So they also have their own expertise written in text, Excel spreadsheets or whatever. We will leverage both academic knowledge and client knowledge to give an answer into Catia in natural language.
We are not going to replace engineers, because the point is we are going to augment engineers. The differentiating point will be in the way people are looking at the answers, exploring different alternatives and making the right decisions. So we are not going to design cars with robots. We are going to augment the capacity of engineers to find the best innovation for the next vehicle.
What’s the projected timeline on the capabilities you’re describing?
We already have many AI technologies in our platform and solution. And I think progressively we are going to implement different capabilities starting next year.
Is Catia doing anything to aid sustainable product design?
Yes. There are three axes to this.
Sustainability for us starts with a very simple thing: improving product performance to get less emissions. For example, you reduce the weight of an aircraft, you reduce emissions. You improve the aerodynamics of a car, you reduce emissions. So the first thing we have done for many years is that we are helping our clients to improve sustainability goals by improving product performance.
That’s number one. Number two is we have introduced a specific dedicated product into Catia for LCA, lifecycle analysis. So it means that if you are an engineer, you can use this product to automatically generate the scorecard for where you are against sustainability goals.
We have been partnering with a company called Ecoinvent, which has the library of human activity that generates things that need to be reduced—so CO2 emissions, water consumption, greenhouse gas, whatever.
So if you are a Catia designer, you know the product, you have a geometry, you have the material. So we are automatically able to compute a set of parameters to help clients to produce a lifecycle assessment of their product.
And it’s important to do this in Catia. If you do it after the fact in an Excel spreadsheet, it’s good you are reporting, but what we want is not to do reporting. It’s to be able to assess the lifecycle analysis early enough, at the concept stage, so that when you find that there is a problem, you can still solve it. If you discover it too late, maybe you will not be able to change the product or it will be so costly that you will never do it. So the more we can take that upfront, the more you can influence.
So that’s the second axis. The third axis is very interesting. When you do design for circularity, it’s a whole new approach. It’s a completely new way to do innovation. Because you really need to have in mind not only that the product will fit to the client or will be aesthetic or will have the right performance, you have to take into account how much it is circular.
And so we have put together a systematic approach, which means that even before you start creating 3D, you think about the requirement of the product, you think about the function, you think about the logical architecture of that product so that it’s circular from day one.
The system approach is very key in the future of Catia in what we do right now. Catia for many years has been seen as a CAD system to do parts in 3D. But the reality is that now products are more and more complex, the mix of mechanical, electrical, software. So if you want to be able to design such a system, you need to have a system approach. The market is calling it model based systems engineering, MBSE.
So Catia is not only a CAD system anymore. Catia is a tool for engineering at large that combines what we do best on 3D for the last 40 years plus the system approach. And this system approach is very clear for all. It is very critical for sustainability and circularity.
Thank you for taking the time to speak with us today.
My pleasure. There is a real revolution in our sector. The passion for engineering is in our DNA, and this is why we want to serve this market in the best way.