Simulation tools are widely accepted as foundational tools for industrial innovation and are being widely deployed to solve the grand challenges facing humanity.
Siemens has sponsored this post. Written by: Jean-Claude Ercolanelli, Senior Vice President of Simulation and Tests Solutions for Siemens Digital Industries Software.
In 2024, simulation tools are widely accepted as foundational tools for industrial innovation and are being widely deployed to solve the grand challenges that humanity is currently facing. With the accelerating growth in computational software and hardware capabilities, simulation has become ubiquitous in the design and development of new products.
Computations that took a week on the first personal computers back in the late 1970s can now be completed in milliseconds on a consumer-level laptop. Software developments have also massively accelerated the pace at which simulation takes place.
However, simulation technology in its current state has matured and hit a scalability ceiling. We have transitioned from a paradigm of computational limitations, where access to appropriate compute resources was a major hurdle (and manual efforts were negligible), to one where human expertise is becoming a scarce commodity. Accessibility to experts able to operate complex simulation software is the bottleneck.
Broadening the applications of simulation – offering anyone access to simulation technology and enabling simulation to be utilized in all phases of a product’s lifetime – is critical to surpassing today’s growth limitations. Substantial innovation in technology is required. Future innovations need to go beyond just improving accuracy and speed. They will need to lower the complexity, a major roadblock in the simulation industry.
AI, machine learning (ML) and large language models (LLMs) automation present new and exciting opportunities to democratize simulation. They could enable everyone who needs to perform a simulation to benefit from it. This shift holds the promise of significantly transforming the industry. Broadening the impact of simulation technology will allow the unlocking of novel markets. For example, marketandmarkets.com projects the size of the Digital Twin market to grow at a CAGR of more than 60% to $100 billion-plus in 2028. Similarly, the industrial metaverse is expected to be the same size and grow at the same rate.
The industrial metaverse and generative AI can democratize simulation, making it accessible to a much broader audience. To make this possible, future design environments will need to offer an experience as engaging and interactive as a video game, while keeping their industrial quality. Current barriers such as user experience and cloud computing access are being actively addressed and will enable us to rethink current approaches to democratization.
By maintaining continuous synchronization with its real-world counterparts, digital twins aim to integrate the real and digital with the ambition to enhance products, services and more. This is just the beginning. The industrial metaverse can act as a place where people and AI synergistically collaborate to create industrial innovations that solve real world problems and create further opportunities.
The ideal future scenario is one where designs and engineering data are constantly analyzed in the background. These analyses then keep designers and engineers continuously informed and systems optimized. Workflows are not only seamless but also highly automated — further unifying the virtual and physical worlds. Thereby designers will only partially be aware of the predictive technology in the background.
In the coming years, simulation will become relevant to a wider set of user profiles, be applicable to a greater number of use cases and be present throughout the entire lifecycle of products and industrial processes.
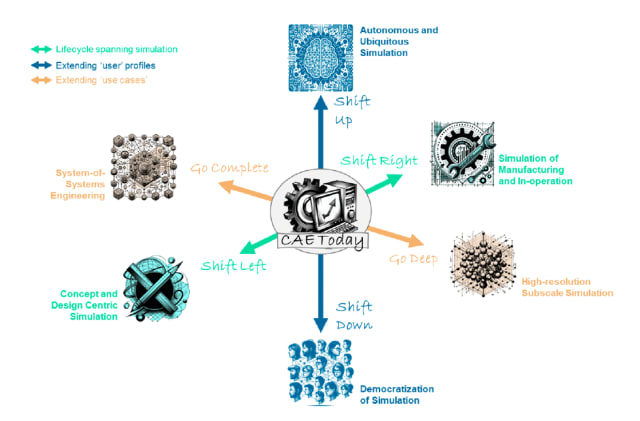
That all being said, the six main trends in the future of simulation are:
- Simulation is shifting left: Simulation will increasingly be applied at the early stages of product design, enhancing decision-making and cost-efficiency. With advancements in computational speeds, simulation will serve as a crucial tool in early design ideation, allowing non-expert users such as designers and sales professionals to perform preliminary assessments and increase return on investment.
- Simulation is shifting right: Simulation will extend its reach into manufacturing and operational phases, bolstered by the rise of IIoT. The capability to simulate intricate production processes and customized products will become integral for operational efficiency. Autonomous simulations will be central in asset management, with digital twins using virtual sensors to augment limited physical data.
- Simulation is shifting down: There will be a radical democratization of simulation, opening up its benefits beyond specialized engineers to a wider audience. User-friendly interfaces will cater to SMEs, hobbyists and the general populace, stimulating innovation and market expansion. This shift will see simulation tools becoming more accessible, resulting in a substantial increase in user base.
- Simulation is shifting up: The future of simulation is autonomous and omnipresent within the Industrial Metaverse and Generative AI frameworks. Cloud-based simulation microservices will facilitate the shift from human-dependent simulations to those that are self-evolving, minimizing the need for human input and maximizing efficiency and adaptability.
- Simulation is going deeper: Simulation tools will delve into higher resolution, enabling the modeling of systems across a broad spectrum of scales, from planetary to sub-molecular levels. This deep simulation capability will unlock new potential in advanced material design and other fields, pushing the envelope of efficiency and design precision.
- Simulation will be more complete: The growing intricacy of systems-of-systems will drive the shift towards more agile and collaborative engineering approaches. Model-based systems engineering (MBSE) and systems modeling language (SysML) standards will become more prevalent, as reduced order models (ROMs) derived from detailed 3D models become crucial for rapid prototyping and system analysis. This will streamline the entire development process from concept to completion.
Put simply, in the very near future, engineering simulation will be used to aid in the design, engineering, manufacture and operation of products or processes. Anyone who has the need will easily be able to predict all relevant behavior. The solutions will be achieved either in a prescribed timeframe (from real-time to overnight) to an indicated level of accuracy, or to a prescribed accuracy (from good enough to certifiable) as fast as possible.
And eventually, tools will be aided by AI, ML and LLM embedded via the digital twin and industrial metaverse. Thus, everyone will use simulation either consciously or unconsciously.
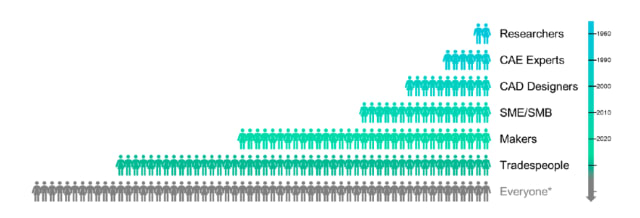
Backed by a global team of engineering specialists, Simcenter provides our customers with insight to the real-world performance of their products or process, allows them to accelerate innovation over the entire lifecycle and build a better tomorrow, faster. We are committed with our simulation and test solutions, whether software, hardware or services, to help industries have a positive impact on our world: improve how we live, how we travel, how we connect to each other and how we are cured.
To learn more, visit Siemens Simcenter.
About the Author
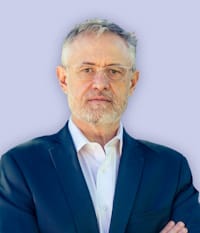