Why BMW relies on diversified systems from SAP, PTC and Siemens, while Mercedes uses Siemens Teamcenter.
How an ideal PLM system should be set up at an automotive OEM is a frequently discussed question. The central pieces of a cPDm (collaborative Product Definition management) setup are complex regardless of which path you choose: whether a more homogeneous platform like that used by Mercedes Benz, or a diversified solution like those used at BMW.
The environment around a PLM setup is always characterized by diversification, with usually hundreds of different CAx and other software connected to the central structure and product databases. But regardless the choice of CAD system is of great importance. BMW’s recent decision to continue investing in Dassault’s CATIA — including a digital twin concept — demonstrates this idea, as does Mercedes’ decision in 2015 to replace CATIA with Siemens NX.
We will take a closer look at how BMW chose to configure its PLM setup as it looked in 2023, which is based on several commercial solutions alongside proprietary, self-developed databases. This strategy aims to make BMW more supplier independent by investing in solutions from three major PLM players: SAP, PTC and Siemens Digital Industries Software.
In contrast, Mercedes Benz has chosen a more homogenous approach based on Siemens Teamcenter in its corresponding setup. This will be discussed later in the article through a conversation with the man who controlled the swap to NX at Mercedes, Alfred Katzenbach.
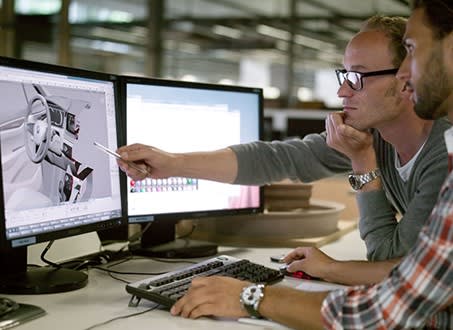
Some background about BMW and Mercedes Benz’s setups
BMW has several different systems and suppliers. On the PLM/PDM side, three systems are used — though this could be categorized as five or six depending on where you consider the proprietary solutions PRISMA (for geometry and functional data), Fundus and TAIS (the latter about to be replaced). The other, commercial systems in use at BMW as of 2023 include SAP’s IPPE, PTC Windchill and Siemens Teamcenter.
SAP IPPE is used for configuration, and for compilation of eBOMs (engineering BOMs, which are based on the design work and form the basis for manufacturing BOMs).
PTC Windchill is the new system for mBOMs, and for the sBOMs for managing software.
Siemens Teamcenter is also used for geometry integration and downstream processes.
Mercedes Benz has gone the opposite way. On the PLM/PDM side, Siemens Teamcenter and the proprietary product database SMARAGD are central, providing support for the development of mechanical components and a data hub for innovation-driven vehicle development. The investment in Teamcenter indicates the company’s reluctance to operate more than one PDM system, which would have been the case if in 2015 it had chosen to move on to Dassault’s CATIA V6 as the primary CAD tool (more on this later). Instead, it went with Siemens NX.
BMW’s Recent CATIA Decision
What should a world-class PLM system look like for BMW, one of automotive’s strongest players? The iconic vehicle manufacturer has been working intensively on this for a couple of years, and recently delivered an interesting partial answer: Dassault Systèmes’ 3DEXPERIENCE CAD app, CATIA, will play an important role in the company’s future engineering platform for product development.
A joint press release from BMW and Dassault Systèmes stated that the BMW Group’s future engineering platform will have 3DEXPERIENCE as a core. The essence of this is that 17,000 users will work globally on a digital twin of a vehicle, which can be configured in a range of variants of each model, with availability of data in real time.
This could mean several things for the future of BMW’s vehicle development. One interpretation is that BMW will continue to use and possibly expand the use of Dassault’s CATIA, as a design component of its PLM setup with a solution that is set up according to a digital twin concept. It is unclear whether they will go with CATIA V5, the newer V6, or a combination of V5 and V6.
From a forward-looking perspective, however, it sounds more likely that BMW would invest in a transition to the more modern V6 platform, which normally also requires that you also buy the PLM/PDM solution ENOVIA as the V6 database/backbone. This would make for four commercial platforms at BMW, rather than three.
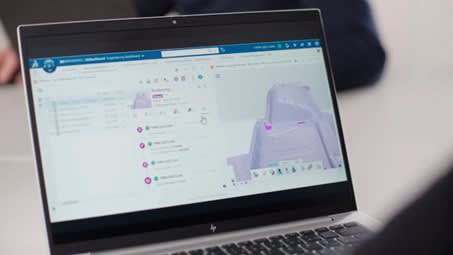
A conversation with the man behind Mercedes’ CAD switch
This is an interesting decision by BMW, especially in comparison to Mercedes Benz’s approach to changing its CAD system from CATIA to the Siemens Digital Industries Software flagship, NX CAD, in 2015.
One of the primary reasons for the change was that Mercedes did not want to operate two parallel PDM systems, which would have been the case if they had chosen to continue with CATIA and upgrade from the V5 to the V6 version.
In connection with Mercedes Benz’s 2015 CAD system swap (before the Daimler Truck spinoff), engineering.com engaged in a discussion with professor Alfred Katzenbach, then Director of IT Management at Mercedes-Benz’ R&D department. He was responsible for the project’s preparation and presentation to the board of directors.
Siemens Teamcenter was previously used as a PLM/PDM backbone. So, why did Katzenbach and his team advocate the switch to NX? As it turned out, the homogeneity issue regarding their basic PDM systems was a significant reason. Among other things, Katzenbach pointed to the problem of using and being forced to coordinate the data management between two different PDM systems. This was crucial. If Mercedes had chosen to continue in the CATIA environment and upgrade from the V5 to the V6 version, they would have had to run two systems in parallel: Teamcenter, which they already used, and Dassault’s new ENOVIA V6 which was required to use CATIA V6.
“Such an upgrade had become tough,” said Katzenbach. “Even when we reflected on the change from V4 to V5, we could see that such an upgrade was like a system change. It wasn’t just a version change. With this experience, we decided to ask ourselves the strategic question, ‘is this the best option for the company’ at the next possible opportunity.”
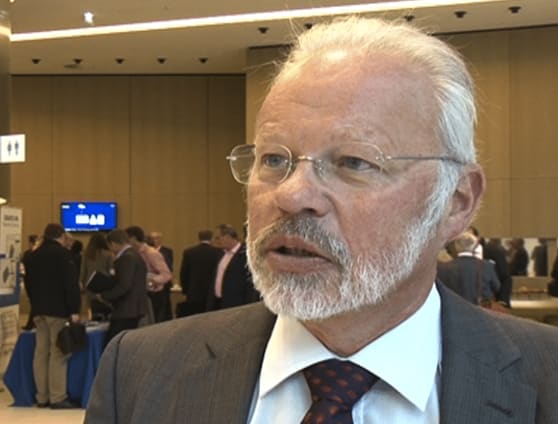
Poorer support for sophisticated technical design processes
From the beginning, Katzenbach planned to stay with the two-vendor solution they had in place, with CATIA from Dassault and Teamcenter from Siemens PLM. Undoubtedly, such a strategy has its advantages, both from a risk management and cost perspective.
So why did the former Mercedes R&D IT manager choose to go with the one-supplier option?
“In this discussion it became clear to us that with ENOVIA V6, as it stood, it would not be possible to support the sophisticated technical processes we have at Daimler (then a part of Mercedes),” said Katzenbach. “Also, if we would have chosen CATIA V6, then ENOVIA V6 was mandatory. We would have had to run two PLM-PDM systems (Teamcenter and ENOVIA) in parallel, which would have cost twice as much money.”
Alongside CATIA, BMW uses Autodesk ALIAS on the CAD side
But events played out differently for BMW who used to handle several PDM systems, but recently chose to go ahead with Dassault Systèmes and CATIA. Presumably they will continue for a while in the V5 environment, but if they want to move on to V6 or V7 when it comes to the table, the ENOVIA app on the 3DEXPERIENCE platform will be required and will add yet another system to administer.
Elsewhere on the CAD side, BMW uses Autodesk’s ALIAS for the styling processes.
But how did BMW’s systems breakdown look in general? We’ve taken a closer look at the matter, domain by domain.
Simulation & Analysis
BMW uses a multitude of current S&A software, including offerings from Ansys, Siemens Digital Industries Software, Dassault Systèmes, BETA, Altair, Hexagon and MathWorks. However, we are only listing solutions from the major suppliers (ISVs) here:
- ANSYS, including LS Dyna
- Siemens’ StarCCM+
- Dassault Systèmes’ DS Powerflow, DS Simpack and DS Abaqus
- BetaCAE’s ANSA
- Altair Hyperworks
- Hexagon’s MSC Nastran and MSC SimManager
- MathWorks’ MATLAB and Simulink
Requirements systems
On the requirements management side, BMW primarily uses PTC’s Codebeamer, while IBM Doors is about to be phased out. Also, the proprietary ZAK system is about to be replaced, and Codebeamer will take the main role. This solution can handle full vehicle requirements. IBM Doors was being used for powertrain requirements.
Model-Based System Engineering (MBSE)
In this domain, it is again a PTC solution in focus: PTC’s Integrity Modeler. BMW has also worked with proprietary solutions such as EESML (Magic Draw) and Wirkkettentool (Effect-chain).
ALM, Application Lifecycle Management
The current primary solutions in 2023 included IBM’s Rational suite, Atlassian Jira/Confluence, Teamscale, CodeSonar and Github, among others. Proprietary platforms are ASCENT and CodeCraft.
Electrical/Electronics
An exciting domain in light of the extensive electrification of the vehicle fleet, as well as the explosively growing importance of electronics in general. Here, BMW has chosen to rely on well-known software from Vector, Zuken, LDRA, Matlab, Autosat, Polyspace and Octane.
Digital Manufacturing
This includes domains such as digital twins, Bills of Process (BOP), and manufacturing BOMs. Software used includes Siemens Teamcenter/Tecnomatix solutions such as Process Simulate and Plant Simulation. A PTC solution is once again in the arsenal with the Windchill Navigate solution, as well as Dassault Systèmes’ DELMIA app.
An interesting recent player here is NVIDIA Omniverse, which is used for configuring and simulating digital factories. This software has played a major role in the digital factory developed over a couple of years in Hungary for the production of electric cars. The factory is not yet finished in physical reality, but exists as a complete digital model.
Manufacturing Execution Systems (MES)
Within MES, the software used includes IPS-L, IPS-C, IPS-Q, IPS-I and AIQX.
After-sales Services PLM
In principle, a series of proprietary solutions are used here. However, SAP’s IPPE has brought modernity with a new initiative: iFactory Shopfloor Digital.