Lessons learned from Boeing, CIMdata, a PLM coach and BAE Systems’ Eurostep about the status of digital thread concepts.
What does the digital thread concept really mean? There are several definitions, but Peter Bilello, president and CEO of CIMdata, shares an excellent description:
“Essentially, the digital thread is a map of decision nodes, which looks like a kind of spider web. For some, such a network is actually a realistic representation of how data and processes are interconnected in companies during the life cycles of their products. These networks need to conceptually connect hundreds, thousands, perhaps millions of information nodes and data stores, and that is where the value is expected to be found.”
He shared this illustrative spider web metaphor during the 2024 PLM Road Map & PDT Europe event held a couple of months ago in Paris. The event was organized by CIMdata and the BAE Systems-owned, standards-based and PLM developer Eurostep. The central theme of the conference was highlighted in the title: “The Digital Thread in a Heterogeneous, Extended Enterprise Reality.”
With a sold-out house, interest in the annual conference was at a record high. What was driving this interest and what were the lessons learned about digital threads? How are they being used in practice and what’s the general status on the digital thread journey? What does AI mean in this context?
In retrospect, this road map provided a universal value gauge of the state of digital thread concepts — particularly in the industry segment that is always at the technological forefront of product development, Aerospace & Defense. In today’s article, I have picked out some of the most important lessons brought up at the conference.
The road to becoming data-driven enterprises
The major trends around digital thread concepts are clear, even though the digital thread is not yet mainstream. There are still many questions and experiences are limited, but the work has started in several places. One thing is clear to Bilello, it would involve the “connection of thousands, or maybe millions of nodes.”
Eurostep’s Håkan Kårdén acknowledges the challenge of this claim. “The conference showed that many have set their sights on and even started implementing the transformation towards becoming data-driven enterprises. It is not easy, but it’s necessary to establish things like the digital thread,” Kårdén says. “At the same time, there are many who would rather talk about ‘business transformation’ than about ‘digital transformation.’ The picture is complex when many classic PLM truths are set against the possibilities of the new age. Here, it is not just the promises of the new technologies that rule, but just as much it becomes a matter of business development.”
“That said, [this] is expected to affect not only the digital thread but pretty much everything else, as well. Today, for example, it is highly doubtful how AI would cope with key areas such as system configuration in aircraft design, which require in-depth understanding. And hand on heart: Who would dare to fly in an AI-configured aircraft as the development looks today?”
Kårdén painted a general backdrop to development where product complexity continues to increase, which in turn is based on the needs for improved cross-business and cross-domain collaboration. In light of this, digital transformation becomes a success-critical issue, which results in manufacturing companies that want to maintain competitiveness and therefore must create robust digital threads across their organizations. This, in turn, is connected to the creation of digital twins and, ultimately, effective PLM integration.
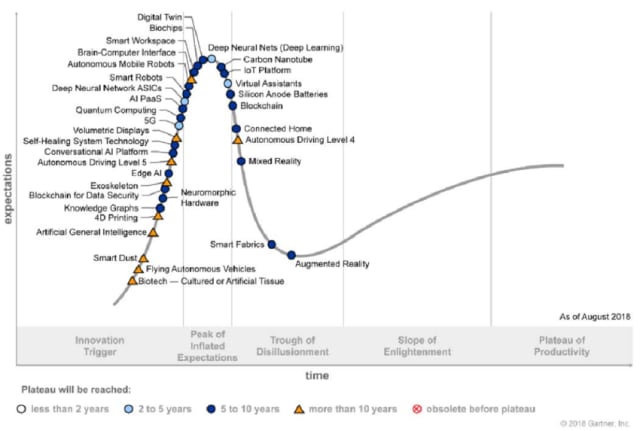
Gartner’s Hype Cycle is, in this context, an interesting measure of how bold new technologies often travel. Digital twins and threads are an example of what the development curve often looks like. These closely related technologies topped the Emerging Technologies Hype Cycle curve in 2018 and were expected to reach the so-called “productivity plateau” between five to ten years. Thus, right now, digital twins and threads are at a stage when the industrial applications have begun to take off.
From Boeing and Airbus to BAE Systems
At the conference, several companies on the aviation and defense side showed off a variety of interesting use cases. What are Boeing, Airbus and BAE Systems doing? Let’s review what Bilello alongside CIMdata’s practice director James Roche, Boeing’s senior business engineer Robert Rencher, PLM coach and blogger Jos Voskuil, and BAE Systems/Eurostep’s CEO Mattias Johansson had to say on the digital thread topic and status.
In summary, collisions are common between existing solutions and new technologies being introduced. The way forward often rightfully requires caution when new technological steps are to be taken.
Take Airbus as an example. New aircrafts are still developed and manufactured with “old” PLM technology, because you don’t want to take unnecessary risks. In addition, these planes have long lifespans of up to 40 or 50 years, which of course requires that the systems used within them must last the test of time. Add to this the fact that aviation operations are tightly regulated, and it means there are some tough obstacles in the development processes and the digital path forward.
Leaving the document paradigm to become data-driven
This does not prevent the existence of positive digital steps for development. Many in the A&D industry talk about becoming data-driven and leaving the document paradigm, which is a concept that links to the development of digital twins and threads, bringing them into the development process.
These developments in A&D, as in the automotive industry, are exciting. At the same time, they make for tough demands where data quality becomes enormously important. There are smaller projects moving in this direction, but the larger investments are starting to see the light of day. Furthermore, it is crystal clear that AI will have a rapidly growing role. But AI itself does not save anyone. AI can do a lot with text and maybe even program code, but running on product data requires not only data quality but also deeper understanding. For example, configuration control is key in aircraft design, and it is not something that can be left to AI to guess.
The digital thread in the aviation industry
As usual in product development, the airfield plays a prominent role when it comes to emerging technologies like digital twins and threads, particularly through lobbying of the Aerospace & Defense PLM Action Group. The group includes all the major players in the aerospace industry, with companies such as Boeing, Airbus and others represented. The driving force in this PLM-related group is Roche, who shared extensive insights from the survey, “The Promise and Reality of the Digital Thread” at the conference.
This survey digs deep into the status and implementation of digital thread concepts in A&D-related companies. One conclusion from the survey is confirmation that the digital thread is still in its early stages.
Here’s how it generally looks:
- New influences are driving the rise in digital thread investment.
- The next investment phase will bring greater change and higher risk.
- Industry leaders have different focuses in their implementations.
- Currently, standards and openness on the solution side are in short supply.
- Above all, the systems engineering side seems to be the main driving force for digital threads.
- Technological development is fast and business strategies keep pace.
- A third generation of digital thread technologies is about to see the light of day.
Boeing examines the digital thread
That Boeing is betting on going further and investigating digital threads is no surprise. In Paris, Rencher noted that digital twins and digital threads are tightly connected. A related project has been investigating applicable standards to support a digital twin/digital thread and is currently in phase four of seven. The use of standards as communicative bridges is extensive at Boeing. This is primarily to meet the diversity in its own and in its suppliers’ extensive and varied software arsenal.
So far, the following has been concluded:
- Standards for digital twin overlap, likely a function of standards bodies representing their respective views as an ongoing evolution from a historical perspective.
- The limited availability of mature digital thread standards requires greater attention from standards organizations.
- The concept of the digital twin continues to evolve. This dynamic will be a challenge for the standards organizations.
- Coordination of the development of the respective standards between the digital twin and digital thread is needed.
- The organization, definition and activation of the digital twin depends on the data and information provided by the digital thread.
A PLM coach’s view of digital threads
Speaking of the development of digital threads, Voskuil is on an exciting track: linking the conference theme to the fact that digital transformation within the PLM world tends to move from coordinated ways of working to connected ways of working. He believes this also applies to the digital thread.
What is the difference between a coordinated and a connected digital thread?
“A coordinated digital thread is one that connects different artifacts in a company. These relationships are created and managed to support traceability and an impact analysis. This digital thread requires human interpretation to process the information,” Voskuil said.
“The connected digital thread is one where the artifacts are datasets stored in a federated infrastructure of databases. Such a digital thread provides real-time access to data through applications or dashboards for users. The real-time access makes the connected digital thread a solution for multidisciplinary collaboration activities in real time,” said Voskuil. He illustrated this with the digital thread as an infrastructure on top of five potential business platforms: IoT, CRM, ERP, MES and ultimately the product innovation platform.
After the definition of these two threads, an important trend to realize is the “not-for-profit connected digital threads” such as GS1, the Digital Product Passport and upcoming Catena-X. These are infrastructures like the internet that get created for a connected purpose (industry/compliance/regulations) and are an important trend using blockchain, web3 and AI concepts.
In conclusion, Voskuil advocates that the connected digital thread is the future, stating “It portends the demise of monolithic PLM.” The change is needed for operational efficiency and compliance with more and more environmental regulations.
“The digital thread must be built on standards”
Why does a digital thread make sense? Johansson discussed this under the title, “Why a digital thread makes sense, why it goes beyond manufacturing and why it should be standards-based.” Given Eurostep’s role in the field of standards-based PLM, his views made sense.
Digital threads are not a PLM project, claimed Johansson. There is really no clear start or even finish. PLM shouldn’t even own the threads.
“They usually evolve over time based on a vision, business strategy and a need to solve the most pressing problems or respond to the most promising business opportunities. A digital thread, with a heavy emphasis on one part of the product life cycle, can easily result in suboptimization. What if there is a way to start neutrally with a predefined model to be implemented piecemeal?” he asked.
The answer is related to Eurostep’s collaborative hub, the ShareAspace software. A standards-based backbone that makes a lot of sense in many environments, especially those related to problems with different data formats and validity over time.
Johansson generally believes that standards-based solutions are good to build PLM on.