The Swedish defense giant combines model-based definition with digital twins, threads and PLM tools to build its next-gen submarine destined for NATO service.
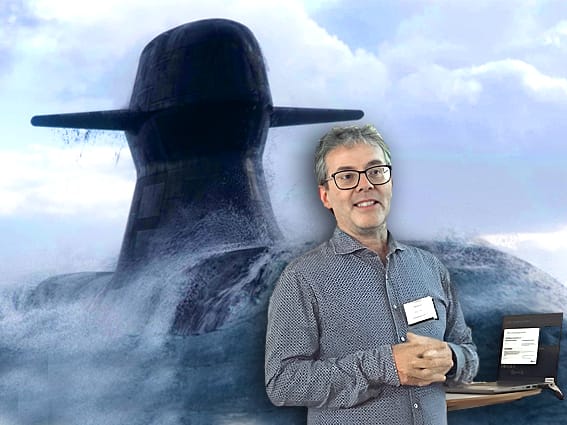
Successful product development increasingly relies on holistic, comprehensive solutions that tie together not only the value chains of product development and manufacturing, but also what happens to the product during the rest of its life—maintenance included.
Capable data management backbones and parallel organizational setups are the connective tissue, with PLM platforms and work structures that can handle the complex journeys through the systems. The pieces are clearly connected and with a relevant digital tool arsenal it becomes possible to support the organizational setups needed for extended process automation. Nobody escapes this reality, regardless of industrial activity.
Swedish submarine developer and warship shipyard Saab Kockums is a particularly interesting example of this, especially with the increased demands brought by Sweden’s new NATO membership. These advanced naval forces, such as submarines, signals intelligence vessels, surface vessels based on stealth technology, patrol boats and Stirling engines are developed and built at Saab Kockums’ facilities in the Swedish cities of Karlskrona, Helsingborg and Malmö.
Saab Kockums’ IT leader Pål Almén, discussed the company’s strategy at the PLM Experience Day in Stockholm. His talk covered the company’s investments in model-based definition (MBD), concurrent engineering, digital twins and threads and how they are deployed in the design and manufacture of the Crown jewel of the Swedish fleet, the A26 submarine.
“A submarine project takes about seven to eight years in terms of product development. After that, they should be operational for at least 30 years. The first maintenance comes after two years, then there are more extensive maintenance efforts every eight years. That says a lot about the complexity and demands of data integrity over time,” Almén said.
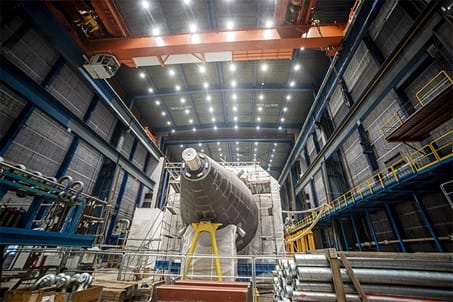
An A26 submarine is built from around 600,000 parts. In each standard maintenance window between 500 and 2,000 are repaired or replaced. During the more extensive eight-year maintenance/modernization, between 10,000 and 50,000 new parts are required.
It is not difficult to see the extent of the challenges in gaining systematic control over something of this magnitude, and Almén says the latest PLM tools and strategies play a crucial role, including digital twin and digital threads concepts using three connected, parallel digital twins:
- One for the submarine under development and manufacture
- One for the submarine in operation
- One for the submarine maintenance
The main commercial tools on the PLM side are PTC CREO (CAD), Windchill (PLM/cPDm), AVEVA ERM (ERP) and BAE Systems/Eurosteps ShareAspace (PLCS/standards-based data backbone). But how does it all work together?
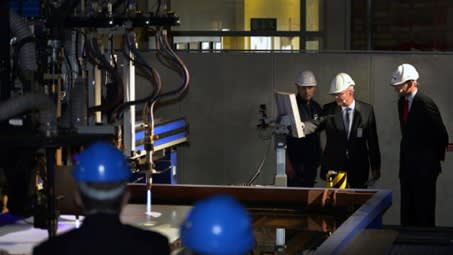
600,000 components at the installation level
The A26 is the definition of complexity. It’s built in five sections and has 140 systems on board, ranging from control and sensor systems to weapon systems, energy converters, air purification solutions and other critical systems. These require about 100 kilometers of cable and 10,000 unique pipes and conduits. And it has to support a crew of 25 sailors.
Over and above the sheer number of parts, any military system requires updates and upgrades to stay modern, which makes maintenance an extensive effort to administer.
But there is even more complexity, as new customers want their own variants of the submarines.
“We thus go from starting with a ‘simple’ configuration to having, over time, many more variants and variables in a model series,” says Almén. “Then it’s about keeping track of costs and lead times and we would like to be faster than our competitors.”
Almén adds that it is also a challenge that during the seven years the A26 takes to build, a lot can happen on the technology side that risks technology becoming obsolete before the ship is launched.
“For one thing, we have to keep all old versions of things on board, in parallel with the fact that technological innovations must be implemented during the course of the development and construction journey. This is tough, yes, but we have the methodology to solve the matter.”
Betting on model-based definition
How is it possible for a company to keep track of the gigantic volumes of data, complex product development and related administrative processes? PLM tools play an important role, and Saab’s set up uses a number of solutions, including:
• IBM Doors for requirements management
• PTC’s CREO for CAD design
• PTC’s Windchill for cPDm (collaborative Product Definition management)
• AVEVA ERM on the ERP side
• BAE Systems/Eurosteps ShareAspace as a backbone of the digital thread where this product lifecycle support standard (PLCS) platform connects software and data from the other applications.
MBD, digital twins and threads
The initial mandatory maintenance, which takes place every two years, requires about 10 weeks to switch out between 500 to 2,000 parts (or 10,000 to 50,000 parts for the eight-year maintenance interval) and new software depending on the type of modernization needed. To manage deep maintenance in parallel with modifications, things must be well prepared in terms of what is to be replaced or added, as well as what must be manufactured and what is ready to be installed.
“We constantly have the product spinning in different stages in the digital thread. Design of what belongs to the next modification, or subsequent upgrades, the next maintenance, or things that are manufactured ‘right now’ are examples of this,” says Almén. “At the same time, on the market side we have to keep track of and communicate within the organization around what should happen in the next upgrade,” he added.
Coping with this using manual paper handling is a nightmare, so here the PLM becomes an important part of the entire value chain.
“It’s important to realize that digital twins can mean slightly different things to different people. For the design and the internal development work it is one variant, for the customer it is completely different—the sailing twin,” says Almén.
Parallel processes shorten the development cycle
The idea behind these digital twins is to develop a model for integrated product development.
The point is to “push in” these flows under each other to keep all the respective timelines short as opposed to doing work in a linear way, with a flow where the actions on the timeline follow one after the other.
Almen says this concurrent engineering process that applies moves A26 production and subsequent tasks from a “waterfall-like” model to development in parallel tracks, but it took time for Saab to develop and implement. “We have to continuously look at what needs to be changed in methodology or adjusted procedurally, and how areas of responsibility and competence need to be developed, look like, sharpened and adapted to become effective information flows,” says Almén.
“Another way of expressing this is that you must have a collaboration and the PLM system is a prerequisite for this to run smoothly. Instead of thinking ‘when I’m done you can start,’ you should think: ‘When I’m done you can be done.’ Consensus is therefore an important aspect. But it also requires breaking up the product, or in our case define what is to be delivered onto the shop floor.”
He also points out that a lot has been done on the development side to establish MBD, for example to automate pipe manufacturing, from specification to finished pipe. No pipe is ever the same as the other, so this is an important factor, says Almén.
Integrated software
For Saab Kokums, this model-based definition roughly refers to developing a practice of using 3D models from CAD to define individual components and product assemblies.
ShareAspace integrates the information/data from the other different engineering domains; things like common surface and mechanical design or electrical design, to prepare the information from the various sources for manufacturing, and to be used in the ERP. The integrations between the systems are based on the “neutral” STEP format and PLCS, which results in universal compatibility where everyone can access, read and manage all the data included in the various designs.
The information from various 3D models and linked management processes is used in the maintenance and upgrade work. The ShareAspace hub thus becomes a secure information center.
Getting started
The work of building all the processes included in Saab Kockum’s MBD model began with Almén and his colleagues breaking down the submarine’s structure depending on the work required and what variant the parts are intended for.
“We generally talk here about front loading,” says Almén. “But the purpose of this is not to put the information in early, but rather to cooperate early in order to be finished early according to the plan you have.”
“Actually, this flow is about employees in the process getting the information or data they always have needed, but now it can happen earlier in the process. Often, the process map now follows what has already been in place at a nominal level. The challenge is to establish a broader view among all employees of the overall development process. People have always seen their parts, but now they have to look ‘a little to the side’ too. But with the process map, we are really talking about a ‘customization’ of how the previous nominal level should now be applied,” says Almén.
From Process Plan to CAD, eBOM, mBOM and serviceBOM
So, how did Saab Kockums build this? Procedurally, the structure is as follows:
- The process plan holds everything together on the shop floor and is based on the same object in each individual BOM list. Often it is about the same object in the database; it’s just that it has several properties at the same time. The various domain engineers must be aware of this in order to be able to search for them. If they don’t, it will be expensive and inefficient to create something that already exists.
- A system BOM contains 20,000 functional components, or the logical objects that are then used as components in the “manufacturing BOM” (mBOM). This covers pumps, valves, computers and similar things. The A26 has about 140 integrated systems, so it becomes its own discipline.
- The CAD defines how things look and where they are positioned.
- The engineering BOM (eBOM)– which is an article list based on CAD and PDM, shows how the product is designed and serves as a basis for the mBOM. “It is sort of the heart of our product model,” says Almén. “It is then an ‘overloaded’ eBOM, i.e. whenever variants and new options are added, we also have an option and variant filter. So, with one and the same eBOM, you can filter out how each variant model looks.”
- The mBOM, which is actually the eBOM rearranged into work packages against production, is about 600,000 parts divided into 3,000 activities.
- The Service BOM covers the maintenance aspects or Integrated Logistics Support (ILS) data, which includes all measures for effective maintenance.
ILS connects to the entire product history
ILS is a management process that mainly used in the defense industry, for example by the Swedish Defense Materiel Administration (FMV) to ensure that a system or product can be used, maintained and stored at low costs, as well as meet high requirements for reliability and maintainability. Successful ILS work means spare parts, special tools, documentation and training are available upon delivery, and the supply of spare parts and required expertise is available throughout the product cycle.
“Our [manufacturing] plan is about exactly this; to plan in order to follow up in the most efficient way possible. What do I mean by that? If you cannot define the deliverables so that people understand what their deliverable is, it becomes difficult. It is important that the semantics and designations of things are the same as those that recur within the framework of the systems that build the product so that others can track them during maintenance,” he says.
The basic pieces in this process are the component libraries, and the ServiceBOM plays a major role in this.
“We perform maintenance analysis on around 20,000 objects that relate to this. Or between 5,000 and 10,000 spare parts that belong to the catalog,” says Almén. “Most things that require service are usually in the system BOM from the beginning. But then you can also look at the detailed design and things that are in the component library. This is a way to give the maintenance analysis a configuration-driven basis to work with. So, our service BOM is system oriented. There are many aspects to service, but these are some of the ingredients.”
Kokums also uses this system to generate the necessary spare parts. Often these spare parts are already in the eBOM, but sometimes they need to be created because they are at a different level in the maintenance mode. In-house production is taken directly from eBOM to serviceBOM, and installed software is included in the maintenance planning.
“Service part regarding the purchased component is another aspect. It goes into something called SICS, which is our LSAR tool for maintenance analysis, our maintenance database, where we store data around maintenance and proposed maintenance from our suppliers,” he says.
The spare parts catalog is based on taking structures from the eBOM or STEP files, generating a representation of the service part in Creo Illustrator, which is then exported to the right place.
PLCs and software updates
Software and updates are separate, but they are often linked to a component.
“Take for example a PLC (Programmable Logic Controller). If you want it as a standard component, you have to consider they have varied control functions and software. In this situation, you want to use the correct service part with the correct software for the intended purpose and also with information about where exactly they sit in the boat. Here you must know which unique program installations have been made on this PLC; for example, the system says: ‘If you are going to exchange this PLC, it must be equipped with this software.’
What about the future?
“We have some ILS databases, but we can also see that there are computerized maintenance management systems, both on board and at the dock. This means maintenance needs can be communicated automatically and proactively. Not least related to things that we already made up for in earlier phases of the product development work. In short, our customers also want to run more condition-based maintenance, they want to measure more and log more. We have to collect and computerize to be able to do it. We no longer have that many employees who stay for 20-30 years and who know when, for example, it is time to change that pump and that valve, etc. We have a lot to do here…”