New CAD add-ons from providers like Autodesk show engineers how to increase sustainability and cut costs in the design stage of product development.
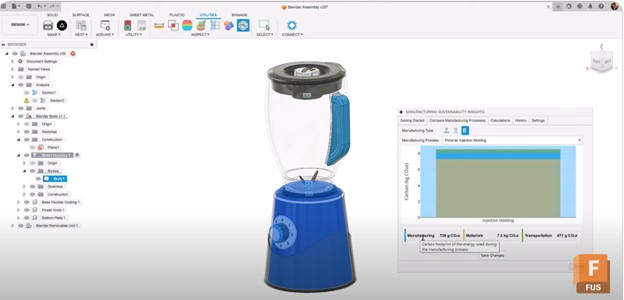
As the cultural and political debate over the existence of climate change and its impact continues, manufacturers are already working to lower the carbon emissions while reducing costs for the products they design and make.
Manufacturers are under more pressure than ever to reduce carbon emissions for a number of reasons, including meeting new regulations and reducing costs. Research by the U.S. National Oceanic and Atmospheric Administration (NOAA) and the Scripps Institution of Oceanography at the University of California, San Diego indicate high carbon emissions combined with El Niño conditions reduce the ability of a land mass to absorb carbon dioxide. When there is more heat in the atmosphere, an area can see an increased risk of extreme and erratic weather, like wildfires. Such events can negatively impact human lives and the natural environment. They also increase shipping costs and energy consumption for manufacturers, contributing to a cycle of waste.
Manufacturers have turned to software developers for programs that provide accurate, up-to-date and easy-to-use information to get better visibility of the sustainability and cost of the products they are designing. The goal is to grasp the impact that product’s design, manufacturing process and related logistics options have on the environment. Understanding and quantifying such data enables engineers to make adjustments that reduce carbon emissions in the design phase before a product ever hits the shop floor.
With more stringent sustainability and product lifetime regulations on the verge of taking effect in Europe and North America, manufacturers that engage in early adoption and gain fluency in the requirements will be well-positioned to abide by the new standards.
There’s a growing list of software that handles this task, including the Manufacturing Sustainability Insights (MSI) add-on for Autodesk’s Fusion 360 platform, Makersite’s Product Lifecycle Intelligence (PLI) software, SpheraCloud’s platform, Microsoft Cloud for Sustainability, General Electric (GE) Vernova and CorityOne. An in-depth look at the MSI add-on shows what it takes to create and test sustainability tools.
Demystifying carbon emission calculations
Autodesk began offering the MSI add-on for Fusion 360 in May through a collaboration with Gravity Climate, a San Francisco-based software developer. The add-on is powered by Gravity Climate, a platform of the same name, that contains a database of information that quantifies the effects of design changes. The add-on is currently being used by mechanical engineers, manufacturing engineers and designers and is available on the Autodesk app store at no cost for Fusion users.
Autodesk says its add-on helps users determine the best process, location and materials for a product. The total sum of carbon emissions comes from adding the amount of carbon it takes to capture the raw material from which the product is made and transport the raw material to the where it is processed. The cost of transporting the material a second time, from the processing plant to the manufacturing facility, is also part of the calculation.
The add-on shows why the place of manufacture matters: some countries have greener manufacturing standards than others. One of the useful features of the add-on is a history tab, which allows a user to display the design changes they make and how these impact the carbon footprint. Such information could inspire a user to reduce the amount of material needed to create the product and determine the “right” process for it.
Choosing a process like binder jetting delves into how many “logistical missions” a manufacturer needs to accomplish. Setting up a process requires planning, coordination and services. For example, if a manufacturer uses aluminum billet, they must transport a lot of material. This requires more transportation and will generate more emissions.
Autodesk product manager Matt Oosthuizen says the add-on incorporates a number of assumptions. This shows the program’s choices can be understood and are not hidden in a “black box.”
“If we take subtractive manufacturing, like CNC machine something out of steel, we take (the) volume (of the product’s form). There is a bounding box associated with it,” says Oosthuizen.
The bounding box, he says, determines the rectangular volume of the product by adding stock material onto it, finding the billet size needed to machine that component. This work by the add-on also determines the embodied carbon of the material. This is defined as the amount of carbon emissions associated with extracting, producing, transporting and manufacturing the product. The work also shows the loss factor—the amount of raw material—removed when making a part.
Using a digital twin in calculations
Software firm Makersite takes a different tactic than Autodesk by creating a digital twin of a product to understand its impact. PLI is designed to integrate with CAD and PLM tools to easily extract data. With PLI, an engineer can create multiple digital twins and distinguish them by the form of the product and changes in the materials that compose the product. This allows an engineer to visualize, compare and share different versions of the product.
PLI delves deep into its data set by providing an explanation of the supply chain dynamics to create a product, a breakdown of the product’s estimated costs and visualizations of the product’s lifecycle assessment. This last step shows the carbon footprint of the product from its existence to its disposal. The Makersite approach looks at the product’s end-of-life considerations and assesses supply chain risks like conflicts.
PLI has the capability to provide so much information that at certain points it begins to display data in a grid. This allows the user to see that obtaining a specific element requires the expenditure of a certain amount of energy and the energy expended will come from a certain source. For example, cobalt production is typically associated with the use of coal.
As manufacturers provide feedback to software developers working on these and other sustainability evaluation tools, they are disadvantaged by the secrecy surrounding manufacturing processes. Reducing cost, energy use and production cycle time helps manufacturers cut carbon emissions and benefit the environment. Unfortunately, the discovery of such information is also cause for competition.