Explore how modern, integrated CAD/CAM software aims to address disjointed relationships between engineers and machinists.
Autodesk has sponsored this post.
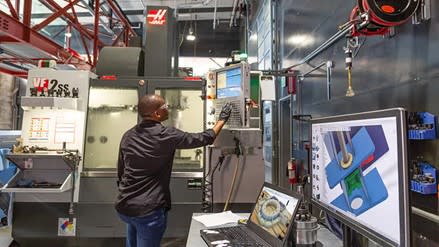
Close your eyes and picture a well-oiled machine shop. What do you see? Perhaps constant communication between team members, with data flowing seamlessly from the top floor to the shop floor.
If you work in the manufacturing industry, you know how difficult it is to achieve this manufacturing utopia of sorts. Unreliable post-processors, multiple software packages per company, siloed teams, and constant design revisions are just a few common barriers teams face today.
Manufacturers are rightfully frustrated by the gaps between designers, engineers, machinists, and fabricators. Fortunately, the next generation of manufacturing software aims to reconcile this relationship, ultimately promising more efficient and cost-effective machining workflows. But it doesn’t stop there. Today’s CAM software is working not only to fix the problems of the past but also to fundamentally change the relationship between software and the shop floor.
Modern manufacturing software aims to foster stronger relationships between engineers, machinists, CAM software, and machines. Once these elements are connected, companies can truly thrive. For this to happen, software companies like Autodesk are integrating CAD and CAM tools, closely partnering with machine tool companies, and investing in manufacturing execution systems.
Eliminating Silos by Integrating CAD and CAM
The dissonance between CAM software and real machines is merely one instance of an overarching problem in engineering: siloes. Whether it’s between CAD and CAM software, design and simulation, or electrical and mechanical engineering, siloes are a barrier to productivity and creativity. Modern engineering software has adapted by prioritizing the ability of users to switch seamlessly between domains.
Al Whatmough, Director of Product Management for Fusion 360 manufacturing at Autodesk, says his team is focused on that mission for Fusion 360, a cloud product development tool that offers a unified CAD and CAM environment. Mechanical engineers modeling a part and machine programmers developing toolpaths to make it can use the exact same software with the exact same user interface—giving each visibility into the other’s workflow, enabling collaboration and eliminating the need for error-prone data imports and exports. “It’s about creating tools that are accessible to everybody and, in doing that, enabling groups to talk more,” Whatmough says.
Laying the Groundwork with Machine Tool Companies
But integrating CAD and CAM is only one step in the quest to break down design and manufacturing siloes. For subtractive manufacturing, CAM software’s ultimate goal is to produce accurate instructions for computer numerical control (CNC) machines, called G-code. But all too often, that G-code deserves an F for failing to perfectly program the machine it was produced for. To bump that grade up to an A, communication between machine tool companies and CAM software companies like Autodesk is necessary.
Whatmough says Autodesk partners with hundreds of machine-tool providers, including major players like Haas, Mazak and Matsuura to help bridge this gap. Thanks to these partnerships, Fusion 360 includes an extensive library of the most popular CNC machines on the market. This library is stocked with post processors, the translators that take Fusion 360 geometric toolpath data and convert it into G-code for a given CNC machine.
These post processors require a significant back-and-forth between Autodesk and its partners, according to Whatmough, because the tricky part is not merely including the translators but ensuring that they produce accurate G-code.
Developing post processors machinists can count on, while significant, is only the beginning of building stronger relationships between CAM software, machinists, and machines. “Post processors are just the first little bit of work that needs to be done to enable the next round of work,” says Whatmough.
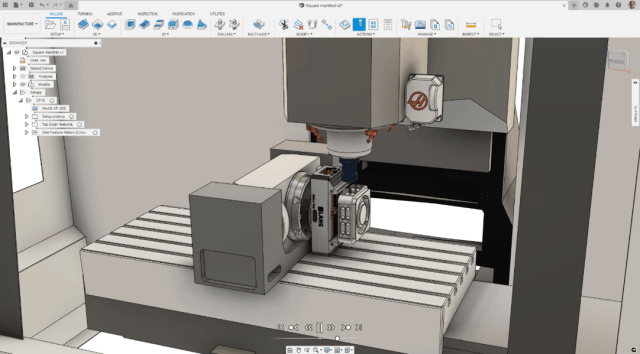
Data Management Ties It All Together
To illustrate the next round of work, Whatmough points to two recent Autodesk acquisitions that aim to close the gap between software and machines: Prodsmart, a manufacturing execution system (MES), and CIMCO, a developer of software for editing, monitoring, and managing CNC machines.
“Think of Prodsmart as the people on the shop floor and the data they use to produce and CIMCO as the machines on the shop floor and the data they need to make the product,” Whatmough says. “That starts to enable a conversation between what’s happening on the shop floor and the programming process.”
The ultimate vision Whatmough describes is a cohesive link between machines and software. For example, a machine could send its real-world state to CAM software, allowing the software to run simulations with exact tool dimensions rather than a best-guess approximation. Or, users could incorporate measurement cycles into a process. A machine might take and send measurements to CAM software as it’s running, which could update the toolpath in real time to account for any discrepancies.
You can think of this vision as a pragmatic digital twin, Whatmough says. The physical machine and its counterpart in CAM software should be in perfect harmony. And while the industry as a whole hasn’t yet reached that point, there’s no telling what value Autodesk’s approach will unlock.
To learn more about Autodesk Fusion 360, visit their website.