Seven organizations will use the money to improve the environmental sustainability, manufacturability and performance of FHE devices.
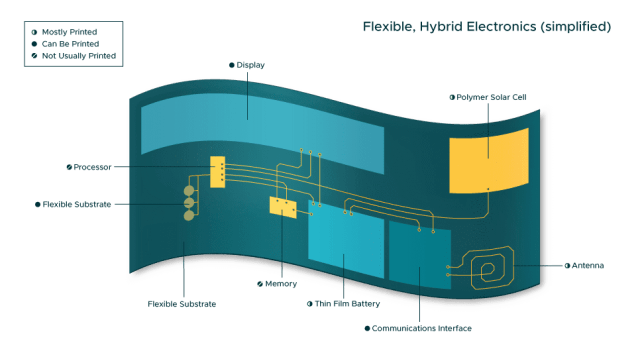
NextFlex, a U.S. Department of Defense-sponsored Manufacturing Innovation Institute funded by the Air Force Research Laboratory, announced $8.45 million in funding on Monday for flexible hybrid electronics (FHE) innovation.
The funding includes $4.25 million in cost-sharing contributions from participants and will go toward nine new projects that are part of NextFlex’s Project Call 7.0 to promote FHE development and adoption throughout the U.S.’s advanced manufacturing sector.
FHE combines the flexibility of low-cost printed plastic film substrates with semiconductor chips to create a new class of electronics. FHE devices and components are generally lightweight, thin and can be manipulated, bent, folded and stretched. It’s an emerging area of tech innovation largely funded by governments, investment firms and academic institutions that are trying to push the development of technological devices that can withstand a broader range of environmental conditions and applications.
These circuits are often made of a plastic polymer film and can be printed on different kinds of surfaces. Some semiconductor chips can be manufactured with metal oxide lithography and placed on a flexible substrate, bypassing the need for printing. However, chip placement poses technical challenges whether it’s done by forcing the chip into place, creating a depression in the substrate to place the chip, or by performing mechanical exfoliation via substrate cracking.
FHEs have many applications, but one of the most notable is for wearable devices and medical devices that need to softly adjust to the contours of the body. They’re also used in prosthetics, rollable displays, Internet of Things (IoT) devices, and sensors for a variety of applications.
NextFlex’s projects include the development of additive manufacturing approaches for integrated circuit (IC) integration into complex multilayer FHE devices, improved environmental sustainability of electronics with FHE manufacturing, manufacturing FHE-enabled automotive components, and manufacturing and safety assessments of wearable devices.
The funded projects under Project Call 7.0 represent a diverse set of companies and academic institutions that are working to advance FHE capabilities. Several of the projects will focus on expanding additive manufacturing approaches for FHE while addressing critical needs required to enhance domestic advanced semiconductor packaging capabilities that are part of the recently passed CHIPS and Science Act.
“These important new projects will enhance the state of the art in hybrid electronics, support national efforts for semiconductor package manufacturing, and help to transition an increasing number of new capabilities into the U.S. industrial manufacturing sector for further advancement of the industry,” said Malcolm J. Thompson, NextFlex executive director, in a news release. “The NextFlex member community is accelerating FHE and additively manufactured electronics toward commercialization in a number of critical application areas addressed in these projects.”
One of Project Call 7.0’s areas of focus is to improve environmental sustainability in electronics manufacturing. This will entail incorporating water-based inks and lower-temperature processing, and assessing the manufacturing reshoring of low-cost, single-use medical devices that are manufactured in a more sustainable manner and use less toxic materials.
Seven companies will receive funding under the Project Call 7.0 initiative. Lockheed Martin Advanced Technology Laboratories will use the funds to create FHE interposers for heterogeneous integration of a high-density fiber optic multi-chip module (MCM) for thinner interposers with finer feature capabilities.
GE Research and Binghamton University will develop radio frequency (RF) MCM with embedded die, printed substrates, antennas, and interconnects for low-loss, high thermal conductivity as well as manufacturing approaches for low-cost, sustainable, single-use medical devices.
Raytheon Missiles & Defense will develop printed interconnect solutions for microwave multi-chip packaging for improved die density. Meanwhile, General Dynamics Mission Systems will develop additively manufactured, doubly curved multilayer circuits with active and passive components for embedded RF functionality in complex structures.
Auburn University will put the funds toward sustainable, additively printed electronics featuring water-solvent inks, greater repairability for FHE, low-temperature processing with high reliability as well as the development of in-mold electronics interconnection and thermoforming for 3D-integrated applications in automotive, aerospace and medical device industries.
UES will utilize the funding to create scalable manufacturing systems for ELMNT liquid metal inks for highly stretchable electronics applications. Finally, Sentinel Occupational Safety will put the funds toward safety assessments of FHE wearable chemical and voltage sensors for reduced hazards in industrial occupations.