Many companies fail to unlock the true value and potential of the latest machine simulation technologies
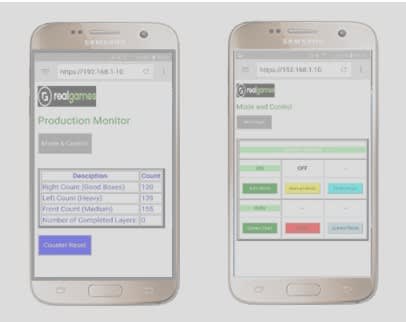
One of the challenges in industry is dealing with the lack of dedicated, specific machine control training for young engineers and other skilled technical support workers. In the modern business model, most engineers face tasks that leaves little time to build on their programming skills. The educational institutions for engineers teach the theory and basics of coding but the basic tools seldom prepare engineers for real life scenarios. These programs aren’t substandard—some things can only be learned on the job..
There is an expectation that employees will get specific training once hired or have a sufficient base from which to learn once working. In an industrial environment, many engineers rarely challenge their machine programming skillset beyond what is required in their current work. Building skills typically involves an experienced mentor and the chance to learn while working on real equipment. But throughput and revenue pressures leave little room for self-education, experimentation and learning from mistakes.
Advances in hardware over the past 100 years have left industrial controls engineers constantly playing catchup on technology. Before computers dominated the machine control industry, electrical relay panels had to be hard-wired to control machine operation. This was expensive, labor intensive and was not forgiving when it came to errors or alterations. During those years, advances in technology were slower, allowing companies time to create programming specifications. This physical nature of machine programming drove efficiencies in design because inefficient or redundant circuits increased costs for material, space and time to wire panels.
The current fast pace of advances in technology has interfered with this practice. Yes, some companies may have libraries of coding available, however, the programmer could be required to use other brands of software or hardware that they have no experience in. Specialty modules used in high level communication, data handling, motor control and more, can be confusing and overwhelming. Not only does this introduce new or untested coding but also requires interfacing that may not have been clearly thought through. This creates an environment which leaves creating code and integration up to the experience of the individual.
Using a simulated 3D factory floor and real Programming Logic Controller (PLC) and Human Machine Interface (HMI) hardware can help engineers hone their skills or to train others while remaining in a safe and environment. Simulation software has advanced to the point that machines and objects exhibit real-world characteristics. Collisions occur, boxes and pallets on a simulated conveyor can jam or fall off, creating an opportunity for fault logic and recovery routine, challenging the engineer to handle real-world problems without suffering the real-world consequences of waste, damage and downtime. Engineers, technicians and technologists are seldom formally trained in machine programming beyond introduction to the basics of the logic. Some challenges may be introduced that allow students to program a sequence of steps necessary to achieve a specific operational goal, such as programing a standard traffic signal but demonstrating actual programming techniques, are beyond the scope of these courses. Features such as hand and auto modes as well as fault handing or safety stop are rarely introduced. In fact, successful program development must be taught spanning multiple courses in PLC Programming, Robotics and Project Management that focus specifically on industrial machine control from the planning stage and through development to validation and testing. Even that kind of in-depth education just prepares a student to enter the workforce.
Programming styles are affected by the chosen hardware platform and language subset. However, simulations are program language and hardware independent—the same the same virtual factory environment can be used with a variety of control hardware and languages. However, even standard machine logic does not always translate easily between platforms, which create stresses on programming and result in poor programs overall. Simulations provide an avenue for training, testing to increase staff performance and the quality of their work.
This investment doesn’t have to break the bank. There are many simulation packages offered ranging from very simple graphics to slightly more costly but very realistic 3D factories. These packages can be ported to a VR system providing yet another level of experience. A simple, low cost setup could consist of a PLC, HMI and Ethernet hub. Considering that time and money is a constraint for most projects, these simple tools can result in less money spent on formal on-site or off-site training.
Not only can this setup be used for basic scenarios, but it can be scaled up to module full articulated interfaced or even basic Industrial Internet of Things (IIOT) such as shown in Figure 4 where a simple phone app is used to control the system. Since real hardware is simulated, there is virtually no difference between the simulated environment and equipment on an actual factory floor.
There is so much untapped potential that business can exploit, it’s surprising more have not embraced this technology. Having even one simulation trainer easily pays for itself in reduced training costs. The scalability and flexibly allows companies and individuals to start from the basics and build up to more complex and exciting scenarios.