Expert PLM use can push Rimac from niche high-technology manufacturer to cost-effective mass-production partner.
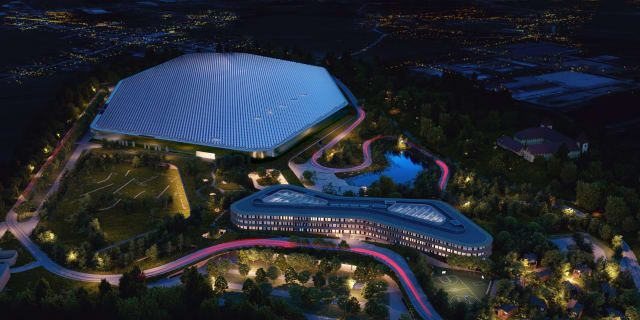
In April 2024, BMW and Rimac announced a long-term partnership to co-develop high-voltage battery technology for electric vehicles. This strategic alliance signifies a notable shift in the automotive landscape, traditionally dominated by original equipment manufacturers (OEMs) operating in silos. This new collaboration has the potential to reshape how car manufacturers create and produce innovative electric vehicle (EV) components.
In conjunction with this, BMW recently announced the extension of its collaboration with Dassault Systèmes to consolidate its product lifecycle management (PLM) strategy around the 3DEXPERIENCE platform. As Rimac Technology, known for its high-performance supercars, enters this partnership with BMW, it signals a transition toward mass-production standards. Let’s explore how PLM is likely to enable such transformation and examine the broader implications for the industry.
Rimac’s evolution from niche to mass production
Rimac Technology is part of the Rimac Group, a company with a reputation for building high-performance electric supercars and advanced electrification components. The Rimac Group includes the Bugatti-Rimac joint venture established in 2021, demonstrating the company’s capacity to work closely with other luxury automotive brands. Beyond developing its own supercars, Rimac has supplied electrification components to automotive OEMs such as Porsche, Hyundai, Kia, Renault, Jaguar, Aston Martin, SEAT, Koenigsegg, and Automobili Pininfarina.
Nevertheless, the partnership with BMW represents a significant milestone for Rimac, as it seeks to expand its manufacturing capabilities to meet the demands of a mass-production OEM. This collaboration will require the setup of dedicated automated production lines for high-voltage batteries at the Rimac Campus near Zagreb, Croatia. Mate Rimac, Founder and CEO of Rimac, sees the partnership as a full-circle moment, saying “My business journey began with a 1984 BMW 3 Series that I converted into an electric car in my garage at the age of 20, so it’s a perfect piece of symmetry to partner with the BMW Group today.”
This move from niche supplier to tier-one partner underscores the evolving nature of automotive partnerships in the electric mobility era. Rimac’s technical expertise in high-performance electric vehicles provides a solid foundation, though transitioning to mass production is likely to require a different level of operational and technological capabilities.
Aligning systems and data
Collaboration between OEMs and their suppliers can lead to significant innovations; it also comes with challenges, especially in aligning PLM systems and practices. When companies like BMW and Rimac partner to co-develop high-voltage batteries, they must harmonize their PLM ecosystems around a common interface to ensure a smooth exchange of information and efficient project management.
Disparate data formats, proprietary software platforms, and often outdated legacy systems can pose obstacles to seamless collaboration. To overcome these challenges, BMW and Rimac must agree on common data standards, implement secure data-sharing protocols, and integrate their PLM processes—from BOM to CAD, digital manufacturing and other enterprise capabilities. This alignment will allow both companies to maintain a consistent flow of information across the product development and manufacturing lifecycle.
Given Rimac’s expertise in high-performance electric vehicles, the company has the technical knowledge to meet BMW’s high standards for quality and performance. However, transitioning from a niche supercar manufacturer to a supplier for a mass-market OEM requires robust PLM integration for traceability, quality assurance, compliance with industry norms and cost targets. By addressing these PLM challenges early, BMW and Rimac can pave the way for smoother collaboration, ultimately focusing on driving innovation and technology component adoption in the EV market.
Streamlining supply chains is key to success
For the BMW-Rimac partnership to succeed, optimizing the supply chain is crucial. Efficient supply chain operations are key, especially when transitioning from high-performance components to high-volume manufacturing. By embracing open innovation, BMW and Rimac can engage with a broader network of suppliers and stakeholders, enabling collaborative innovation and accelerating the development and certification of new technologies.
However, several challenges can disrupt the supply chain. Legacy enterprise systems and data silos can reduce supply chain visibility and complicate traceability, leading to inefficiencies and increased risks. To address these challenges, BMW and Rimac should focus on digitizing their operations around a common data framework and harnessing real-time insights to drive improvements. This could involve implementing advanced data analytics to track inventory, automate logistics and simplify product costing.
Collaborative platforms that enhance connectivity across the supply chain can further boost efficiency by streamlining communication and coordination. These platforms facilitate seamless data exchange, enabling BMW and Rimac to coordinate their supply chains more effectively. By fostering a culture of open collaboration and adopting technologies that promote seamless data exchange, they can reduce lead times, ensure component reusability and mitigate risks associated with disruptions.
A digitized and interconnected supply chain will not only increase efficiency but also strengthen BMW and Rimac’s ability to respond to market changes and customer demands more rapidly. This approach will ultimately support their shared goal of driving innovation in the electric vehicle market.
Despite the shared vision of the BMW-Rimac partnership, several challenges lie ahead. Cultural disparities, technological integration issues and data security concerns can create hurdles. Promoting cross-cultural communication, fostering openness and ensuring robust cybersecurity measures are critical to overcoming these challenges.
Additionally, regulatory compliance and legal complexities add another layer of difficulty. Staying informed and aligned with industry standards, data privacy regulations and intellectual property laws will help BMW and Rimac maintain a successful partnership based on trust and accountability.
The BMW-Rimac partnership marks a significant milestone in the journey toward electric mobility. By addressing PLM challenges, streamlining supply chain operations and embracing open innovation, these companies are poised to set new industry standards. Although the road ahead has its challenges, the collaborative spirit of BMW and Rimac suggests a promising future where innovation drives the transition to electric mobility.
The partnership between BMW and Rimac is certainly a step toward a new era in automotive collaboration, one where high-end electric drive technology meets mass production. The success of this partnership depends on effective PLM alignment, efficient supply chains, and a shared commitment to overcoming challenges. As the automotive industry moves toward a more electrified future, the BMW-Rimac collaboration serves as a model for how co-development and co-production can drive innovation and reshape the industry landscape.