A Forrester report highlighted that maturity impacts manufacturers’ ability to incorporate sustainability into PLM.
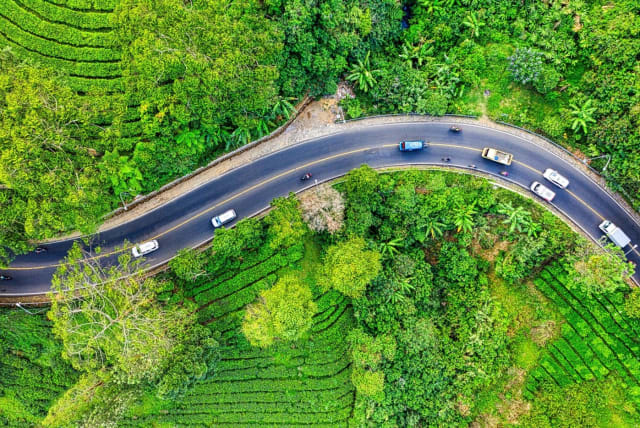
The concept of the Triple Bottom Line approach was coined by John Elkington in 1997 in his book “Cannibals with Forks: The Triple Bottom Line of 21st Century Business.” Elkington, a British entrepreneur and business strategist, introduced the idea to broaden the focus of businesses beyond purely financial metrics to include social and environmental considerations. Since then, the Triple Bottom Line framework has gained significant traction and has become widely recognized as a guiding principle for sustainable business practices.
Makersite commissioned Forrester to assess sustainability’s state and impact in Product Lifecycle Management (PLM) via a survey of 493 product design and sourcing decision-makers from manufacturing firms. The study revealed that decision-makers are at a crucial point in embracing integrated, sustainable practices to meet the needs of a dynamic global market. Key findings emphasize the importance of streamlined access to reliable data for efficient product design and sourcing, while organizations leveraging detailed product lifecycle intelligence gain a competitive edge with faster time-to-market and more profitable products.
Product lifecycle intelligence: the rise of analytics to drive sustainability?
Simply put, Forrester outlined five key areas manufacturers anticipate will significantly affect their products, prioritizing regulatory compliance, growth and sustainability:
- Evolving customer expectations.
- Growing emphasis on advancing a circular economy.
- Heightened demand for transparency in supply chains.
- Economic constraints.
- Challenges related to supply chain shortages.
First and foremost, deriving business value hinges on accessing pertinent data promptly to inform decision-making. Forrester highlighted organizations’ focus on key initiatives such as bolstering sustainability reporting for compliance and sales support as well as optimizing reliability and efficiency in material sourcing. Additionally, Forrester identified challenges related to data, including maintaining data in existing systems/libraries and measuring environmental impact.
According to the survey results, key initiatives across various industries to enhance efficiency and effectiveness in product design and sourcing included the following top five priorities:
- Improving the quality of data informing environmental impact assessments.
- Enhancing collaboration among stakeholders with a unified product and supply chain data model.
- Enabling ingestion of material, component, and supplier intelligence from multiple sources.
- Improving stakeholders’ understanding of sustainability and adopting additional tools to populate existing material libraries.
- Improving integration between data sources and PLM systems.
Broadly speaking, it’s a matter of building and maintaining an integrated product lifecycle ecosystem with cross-functional analytics that can be trusted, and ultimately linked to PLM processes and associated operational governance to drive effectiveness and efficiency at source.
Organizational maturity: a gap between vision and execution?
Beyond the availability and quality of data, functional data silos and the lack of integration were reported as critical maturity gaps for organizations aiming to drive product lifecycle intelligence to the next level. The least mature organizations are likely to suffer from excessive manual processes that are not fit-for-purpose, coupled with limited or sub-optimal automations, with a focus on efficiency rather than effectiveness.
On the other hand, more advanced organizations tend to prioritize the strengthening of regulatory compliance and sustainability improvement through the “ability to learn how to build high-performance, cost-effective, sustainable products […]” However, it was also reported that “less than half have an automated process in place for tracking a variety of metrics, including scope 1, 2, and 3 GHG emissions, the rate of change of material cost, waste generated and the time to market for product variants or new models.”
Clearly, basic data usage in sustainability initiatives often falls short of manufacturers’ aspirations, creating a gap between vision and execution. Key areas of deficiency include inconsistent monitoring, underutilization of advanced analytics and the need for more granular data.
Beyond the symptoms, what are the root causes?
Forrester pointed out that legacy PLM solutions frequently lack essential material, component, and supplier intelligence, posing challenges for manufacturers in meeting regulatory and customer sustainability and resilience requirements, ultimately impeding product innovation success. Furthermore, this raises several questions: Is it a data, process, or governance gap? Is it a system capability gap, an implementation or adoption gap, or a result of organizational maturity? Are the root causes a combination of these factors?
This aligns with the need for manufacturers to elevate their PLM practices, as emphasized in Forrester’s recommendations:
- First, it is about “modernizing product innovation processes and platforms” to empower designers with product lifecycle intelligence.
- Then, it is about “reclassifying sustainability as a performance initiative” to drive revenue and margin growth.
- And in doing so, “developing a business case for product lifecycle intelligence” to quantify its impact on competitiveness, time to market, and pricing.
- While “ensuring consistent enterprise-level ESG data” to streamline innovation and regulatory reporting processes.
The challenge of driving sustainability strategies forward may ultimately boil down to business change and agility. While high-level recommendations like “Stakeholders across the organization have access to a single source of truth for product design and sourcing” seem straightforward, the reality is more complex:
- Is the lack of PLM maturity primarily attributed to deficiencies in data management, inefficient processes, or inadequate governance structures within organizations?
- Are PLM maturity gaps a result of limitations in system capabilities of legacy PLM solutions, or are they indicative of broader organizational maturity issues such as resistance to change or insufficient investment in training and development?
- To what extent do PLM maturity gaps stem from a combination of factors, including outdated technology, organizational culture, and the complexity of global supply chains?
- How do PLM maturity gaps affect decision-making processes within manufacturing organizations, particularly in terms of product innovation, regulatory compliance, and sustainability initiatives?
- Are PLM maturity gaps reflective of a disconnect between strategic objectives and operational capabilities within organizations, and if so, what steps can be taken to realign these elements effectively?
Embracing business change and establishing supportive governance based on a structured data model across an integrated ecosystem are essential. There clearly is no one-size-fits-all solution. Business change should not be on par with trying to reinvent the wheel, but rather adopt good practice and accordingly adapt the organization’s operating model to maximize value.
This underscores the need for PLM and ERP editors to take the lead in adopting consistent, pre-configured industry-specific proven solutions to tackle the challenge, rather than providing IT toolboxes as a ‘blank canvas’ for building bespoke apps or dashboards with low-code no-code, or other citizen development options. Manufacturers are certainly less interested in building sustainability tracking software and associated system infrastructures—preferring to focus on innovation, commercialization, and portfolio optimization.