MODSIM has the secrets to requirements-driven design.
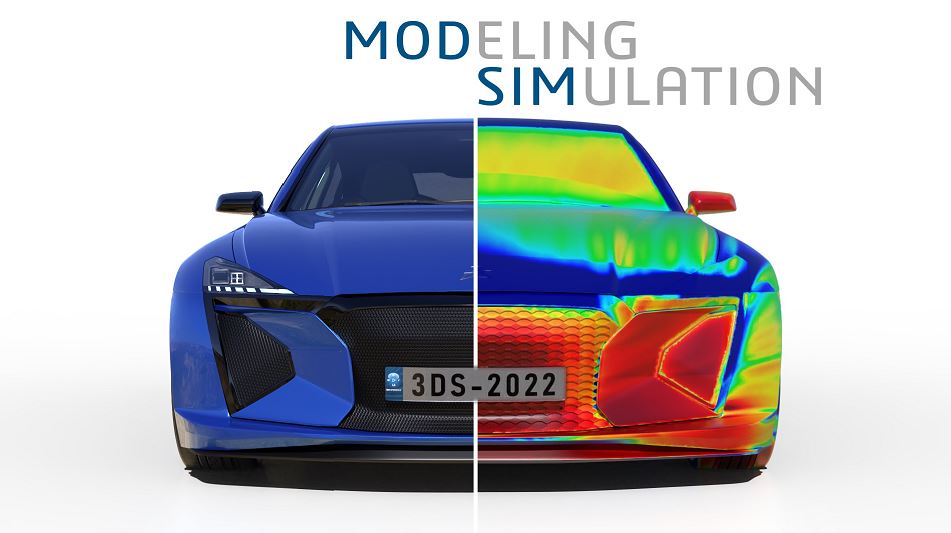
Dassault Systèmes has sponsored this post.
Over the last decade, the term simulation-led design has become well established in the engineering community. Instead of simulating close to the end of development to validate a design — only to find errors and spend lots of time and money scrambling to fix them — companies are now simulating early and often. This enables them to make informed decisions at the start of development when it is easy and affordable to solve product issues.
With the 3DEXPERIENCE platform on the cloud, however, Dassault Systèmes aims to take this concept further by blurring the line between modeling and simulation until they are almost indistinguishable. And in building this MODSIM approach (as the company calls it), they have developed an innovative design paradigm.
“Simulation isn’t the sole driver behind the design,” said Joe Amodeo, director of Process Automation and Optimization SIMULIA R&D at Dassault Systèmes, in a recent webinar. “It’s the very high-level requirements of what your product should be that is driving the design. The simulation is just part of the overall bigger process.”
Amodeo then went on to demonstrate the merits of MODSIM, and in doing so outlined a requirements-driven design process that could make simulation-led design outdated.
MODSIM: One geometry, one model, one virtual twin all wrapped in one
Dassault Systèmes defines MODSIM as a unified modeling and simulation workflow with a common data model, user experience and interface. In this case, this translates to being able to create CAD geometry, clean it up, run simulations and make other design decisions without leaving the 3DEXPERIENCE platform.
Amodeo suggests that the best way to describe MODSIM is to compare it with competing engineering design workflows. Traditionally, a user will make a CAD model, export it, clean up the geometry, mesh it, export that to a simulation package, export the simulation to high-performance computing (HPC) systems, run the simulation, wait for results, export those results to post-processing tools and finally export some results to a report of some kind.
“Every one of those steps involves exporting data, maybe losing some of that information, and it’s kind of inefficient,” said Amodeo. “But the biggest issue really comes when I want to make some design changes or iterate. You’ll find using this kind of traditional process that, depending on the change, I may have to go back somewhere close to the beginning and repeat those steps. For some of the more complex cases like a crash model, for example, that can take weeks.”

MODSIM looks vastly different, as its workflows include no file transfers. In fact, there is no file system at all. Data does not have to be transferred as it is accessible to all the tools on the 3DEXPERIENCE platform.
“Engineering becomes transferable,” said Amodeo, “making it more accelerated, more innovative, more efficient, with the hope being that you in turn can transform your businesses, leading to shorter product development cycles, more desirable products and more cost-efficient design processes.”
As the simulations add up, and the design iterates, the model in the 3DEXPERIENCE platform becomes closer and closer to the final manufactured product. These simulations can then link via co-simulations, or simplified model-based systems engineering (MBSE) models, to create a virtual twin of the final product.
Think of it this way, you start with a CAD model in the 3DEXPERIENCE platform. You then enrich that model by adding an abstraction of the geometry. The model is enriched again by meshing the abstraction. The model is further improved by adding a series of simulations based on the mesh. These simulations are then added into a report that, again, becomes a part of the overall model.
Amodeo added that after producing a report within the 3DEXPERIENCE platform it can be easily updated as the model changes. Consider an engineer changing one parameter within the model. They can then update the model’s simulations and reports with the click of a button. Amodeo says, “that is a complete shift in paradigm, which saves a lot of time.”
A foundation for requirements-driven design
One of the biggest benefits of MODSIM is that it transforms engineering processes so they can be automated and directed by product requirements. Amodeo explained that if a parameter or requirement changes, the model, mesh and subsequent data will update with it. Simulations can then re-run with the new geometry at the push of a button.
This workflow gets more exciting when performing optimization and design space exploration studies. Since everything in the model is parameterized and connected, it is easy to set up iterative processes like optimizations. Just tell the software what parameters can change, what their limits are and what the goal of the study is. Everything then runs as expected.
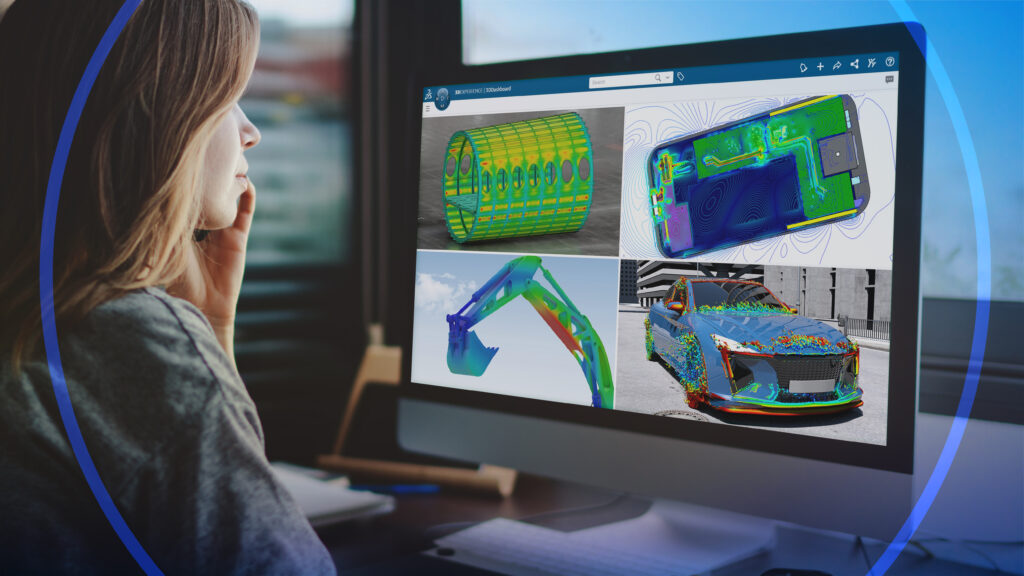
Amodeo added that once a design space is explored, the data all remain within the 3DEXPERIENCE platform. As for all the unique designs in that design space, he said, “We can now just choose one and say, ‘make that our new design’ and we’ve done all of this from the same interface. We haven’t moved any data; we haven’t changed apps or software packages; it is all happening in the same place.”
But how this leads back to requirements-driven design is the most interesting point. Consider the requirements of the final product change mid-development. Engineers can add those new requirements to the model.
“All of this is being driven by the requirements we have on the platform,” said Amodeo. “It’s about the ability to create and cascade requirements. So, the top-level requirements for a vehicle include range, acceleration, drive cycle, etcetera. Those cascade down to the subsystem, so the motor needs to have a certain performance, power, torque, operating temperature, etcetera. And we can cascade those down even further to the parameters that we’re going to use to actually design the model. So, these are parameters that are actually embedded into the CAD model that determine the actual shape, size and features of the model.”
Then based on the design space exploration, an updated design can be selected quickly after the requirements change. In other words, since all of the data from the design space exploration remains in the 3DEXPERIENCE platform, finding a new design is as easy as cross referencing the new requirements with all of the models assessed within the design space.
More benefits of MODSIM
Amodeo notes there are many other benefits to MODSIM, requirements-driven design and the 3DEXPERIENCE platform. They include:
- Automated modeling apps.
- CAD-agnostic integrations.
- Automatic and democratized simulations.
- Access to always-up-to-date data.
To find out more about these benefits, watch Joe Amodeo in the webinar, Going Beyond Simulation Driven Design with Virtual Twins.