Many electric vehicle makers are transitioning from 400-volt to 800-volt systems for faster charging and higher efficiency—but some, like Tesla, are holding out.
As demand for electric vehicles (EVs) increases worldwide, drivers expect better performance. Longer range and faster charging are among their demands, and both boil down to the battery.
There are numerous research projects focused on solving these challenges, but the most promising one is increasing the battery voltage. Today’s EV batteries are commonly 400-volt systems, but EV manufacturers have already begun redesigning their vehicles to shift to 800-volt architectures.
Higher battery voltage means more energy and higher charging power, plus increased efficiency, better performance and weight savings for EV components such as motors and inverters. But high voltages come with new challenges as well. Here’s a look at why the EV industry is so keen to move to higher voltages—and how engineers are making it happen.
What it means to have a 400-volt or 800-volt EV architecture
The architecture of an EV is a complex system involving batteries, motors, sensors, electronic controls, auxiliary equipment, wiring and other components. The battery voltage, whether 400 volts or 800 volts, affects all of them.
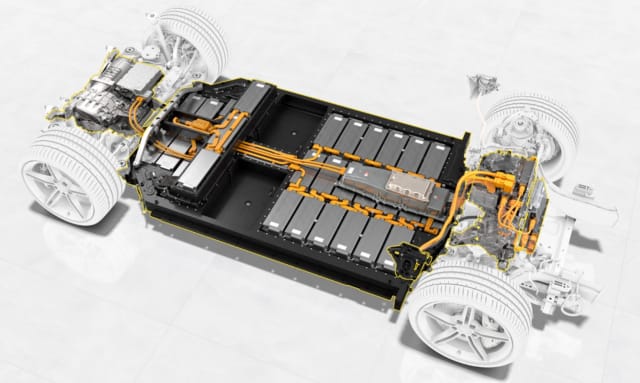
These values are not as fixed as their name suggests. For example, a battery voltage range of 300 – 500 volts is referred to as a 400-volt architecture, and a 600 – 900 volt range is considered an 800-volt architecture. Shifting to an 800-volt architecture is not a matter of simply connecting batteries to get a voltage of 800 volts; this operating voltage is a key parameter for designing all other high-voltage devices in the car.
Why EV manufacturers want to shift to 800 volts
Higher battery voltages mean increased EV efficiency, improved performance and better charging. For drivers, that means faster charging and less energy consumption.
The main parameter for charging speed is charger output power, which depends on voltage and current. Increasing the charging current would lead to more heat and energy loss, so increasing the voltage is a better way to increase power and get faster charging. With double the voltage and equal current, an EV charger could deliver almost twice the energy to EVs. Of course, the chargers and EV’s converters have to be redesigned to be able to carry significantly higher power.
The 800-volt architecture also reduces energy consumption. If a battery outputs the same power as its voltage increases, that means its current must decrease. Since heating and power losses are proportional to the square of the current, heat loss goes down as voltage goes up. Lower current also has a positive effect on battery aging, thereby extending the battery life.
Challenges of the 800-volt EV architecture
The 800-volt EV architecture has unquestionable advantages, but there are still challenges that must be overcome to smoothly integrate the technology in the market.
Charging infrastructure is the first issue. Charging speed depends on charging stations, and most are built to provide power for 400-volt EVs. To take full advantage of faster charging capabilities, 800-volt EVs will require more powerful charging stations.
Another issue is in EV design. The 800-volt architecture requires redesigning the circuits and components to ensure appropriate insulation, fail-safe systems and the right test procedures to prove the reliability of components in a high-voltage environment. The testing procedures must cover worst-case scenarios up to five times higher than the operating voltage of 800 volts.
The equipment costs tend to be higher for 800-volt EVs as well. For example, they tend to use pricier silicon carbide (SiC) switching components in power converters. SiC enables increased switching frequency with very low energy losses (2%) when compared to traditional silicon-based converters (5 – 6%). However, because of the lower current in 800-volt EVs, the wires and links can be thicker and cooling requirements are lower.
There are also safety concerns. Higher voltage systems need more physical space to avoid problems like overvoltage and arcing. Capacitors, for instance, require a minimum creepage distance between polarities to avoid arcing. As the voltage is higher, the required distance is longer—meaning bigger capacitors. This is very unfavorable for EV manufacturers, who want to make everything smaller and lighter to increase efficiency.
Different solutions for the 800-volt architecture
EV manufacturers have analyzed various approaches to overcome the challenges of 800-volt architectures. There are three promising approaches.
The first approach is to make the entire EV’s high-voltage system operate on 800 volts, eliminating the need for voltage conversion between components. This approach enables faster charging and better efficiency. However, it requires more EV redesign and higher costs.
The second approach is to have only some essential devices (like the battery pack and drive motor) on 800 volts, with the rest of the system remaining at 400 volts. The need for voltage conversion between 800- and 400-volt devices increases the cost and design complexity, and also adds conversion power losses. However, this solution requires less EV redesign and lower costs for the 400 V system, while still enabling faster charging.
The third approach is a hybrid solution that involves a battery system capable of switching between 800 volts when charging and 400 volts when discharging. Other high-voltage devices remain at 400 volts. This simple and low-cost solution enables faster charging, though discharging at 400 volts means that a reduction in energy consumption will not be achieved.
We will probably see all three approaches as EV manufacturers switch from 400 volts to 800 volts. As testing procedures develop and prices fall for 800-volt components, we can expect a full transition to the high voltage architecture. For heavy duty EVs that require high power, we may even see architectures beyond 800 volts.
Why Tesla is holding out on 800-volt EVs
The transition to 800-volt EVs is already well underway. Automakers Porsche, Hyundai, Genesis, Kia and Audi already offer EVs with 800-volt battery systems. Volvo, Polestar and Lotus have also committed to 800-volt architectures. Hitachi Automotive Systems is starting mass production of its 800-volt battery system.
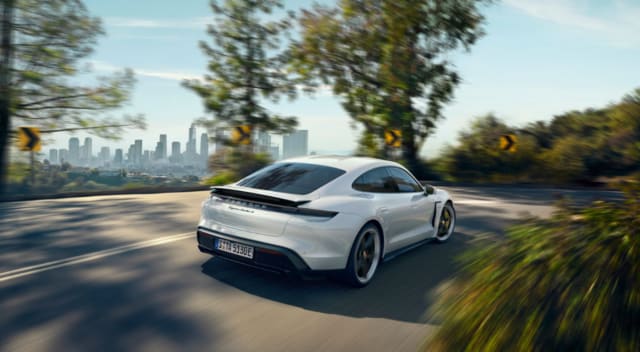
Interestingly, EV pioneer Tesla has not committed to shifting to the 800-volt architecture. CEO Elon Musk has questioned the value of the transition, suggesting it’s not worth the cost of redesign just yet—at least for the company’s smaller vehicles like the Tesla Model Y and Model 3. In the long term, though, he believes that an 800-volt architecture would make sense for a high volume of vehicles.
It may take some time, but one way or another, the EV industry is shifting into high voltage.