Design, simulation and manufacturing goes digital to produce state-of-the-art rec van.
German motorhome manufacturer Hymer is expanding its use of digital design tools to develop recreational vehicles, adopting the Siemens Xcelerator portfolio of software and services for its VisionVenture concept vehicle. Hymer has reaped significant time and cost savings by relying on digital twins and virtual prototyping instead of building physical models and the company aims to achieve additional savings by adopting more components of the Siemens Xcelerator portfolio.
Using Siemens’ Solid Edge software for 3D CAD, Simcenter for predictive simulation and testing and Teamcenter for product lifecycle management (PLM), Hymer has reduced physical mockups and prototypes by 80 percent, according to Frank Heinrichsen, Hymer marketing manager. “By using the digital mockup capabilities of Teamcenter visualization, we can identify and resolve issues before they become costly problems,” said Heinrichsen.
Feature-Packed Vehicle
The VisionVenture, introduced at the Caravan Salon 2019 in Dusseldorf, features a host of technological features that were designed and tested virtually before being built physically. A pneumatic pop-top roof opens skyward for expanded space, with an integrated stairway leading to a private viewing balcony. The pop-top walls, approximately 7 centimeters thick, incorporate a honeycomb structure that inflates with heated or cooled air. The sun terrace below features a glass Infinity Screen offering panoramic views.
Built on a Mercedes-Benz Sprinter chassis, the body features an integrative front design, with smooth transitions between cab and body. The wheel arch panel and selected body parts are produced using 3D printing techniques, giving them a robust, rubber-like quality. The temperature-regulating, energy-efficient Chromacool technology from BASF reduces the surface temperature of the vehicle by 20°C and that of the interior by up to 4°C.
Hymer engineers have woven a digital thread along the entire product design process, using Teamcenter to build prototypes of their vehicles in virtual reality (VR). Designers import the digital twin created using Solid Edge and build digital mockups of the entire vehicle or a part of it to detect and resolve issues. For designing and routing fluid tubing and electrical harnesses, they rely on the Solid Edge Xpress Route 3D routing application.
To verify structural integrity of designs, Hymer engineers use finite element modeling (FEM) analyses, relying on Solid Edge for basic verifications and outsourcing more in-depth analyses to The Team Technology (TTT), an automotive lightweight construction department in the Erwin Hymer group. The TTT team uses Simcenter software for FEM analyses. The two-stage verification process reduces the number of physical prototypes required, according to Hymer.
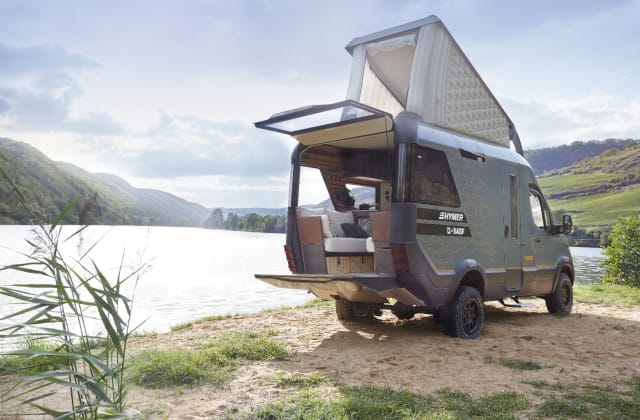
Digital Transformation
Hymer’s growing reliance on digital tools to streamline design is consistent with trends seen by Siemens across various industries, according to Dale Tutt, Siemens vice president of industry strategy. “Our customers are trying to get new products to market faster and they’re dealing with supply chain issues. There’s more and more software in all of the products that they develop. The solutions that our customers are producing are getting more complex,” said Tutt.
With manufacturers managing more complex designs and business arrangements, many are turning to digital tools to accelerate design and testing of new products, according to Tutt. Instead of building and testing physical prototypes, many manufacturers are using digital twins and virtual prototyping to save time and money. “Customers that are embracing digital transformation are able to go faster,” he said. “They’re reducing their overall cycle times by 20 or 30 percent through the adoption of these technologies.”
While Siemens has offered components of the Xclerator portfolio for years, Siemens Digital Industries Software launched Xcelerator in 2019, focused on solutions offered by DI Software. Siemens AG officially launched Siemens Xcelerator across all of Siemens in July 2022, as a curated collection of hardware, software and digital services from across Siemens and certified third parties. Incorporating familiar software tools such as Solid Edge and NX for mechanical CAD, Simcenter for simulation and testing and Teamcenter for PLM, Siemens Xclerator also includes tools for application development, operations, manufacturing and electronics disciplines, as well as automation hardware across all of Digital Industries and support services from Siemens personnel.
At the July launch announcement, Roland Busch, president and CEO of Siemens AG, said: “Siemens Xcelerator will make it easier than ever before for companies to navigate digital transformation – faster and at scale. By combining the real and the digital worlds across operational and information technology, we empower customers and partners to boost productivity, competitiveness and scale up innovations.”
As part of the portfolio launch, Siemens is aiming for its tools to become modular, cloud-connected and built on standard application programming interfaces (APIs). The company also announced an agreement to purchase Brightly Software, a U.S.-based asset and maintenance management software company that brings additional capabilities across key sectors to Siemens’ digital and software expertise in buildings.
Siemens also announced a partnership agreement with NVIDIA to increase use of AI-driven digital twin technology in industrial automation, along with a focus on the industrial metaverse–where real machines, systems and facilities are mirrored in the virtual world. As a first step in this collaboration, the companies plan to connect Siemens Xcelerator and NVIDIA Omniverse, a platform for 3D-design and collaboration. The connection is intended to produce physics-based digital models from Siemens and AI-enabled, physically accurate, real-time simulation from NVIDIA to help companies make decisions faster and with increased confidence.
Future Trends
Looking ahead, Tutt said an increased emphasis on sustainability and the environment will also elevate the need for digital transformation. “As customers start to think about how they’re designing products and bringing those sustainability requirements into it, this is another area where we’re going to see a lot of benefit and growth in digital transformation,” he said. “You’re able to understand how those products work much more efficiently. You’re going to design them with a different mindset so that you can use less materials.”
The industrial metaverse and virtual reality will also become more commonplace, predicted Tutt. “It’s more than gaming, it’s more than visualization. It’s really about being able to have real-time, physics-based simulations and operations of your products as well as your production processes.”
Industry trends may also follow those of mobile devices, which feature simplified interfaces and greater reliance on the cloud data. “I don’t know if we’ll get down to one-button layout like the iPhone has. But I think with technologies like virtual reality for designing and engineering new products and augmented reality out on the shop floor, we’re going to continue to see more of that.”
Hymer’s use of digital tools in designing RVs is just one example of how digital transformation is reshaping how products are designed, developed and tested. Time will tell how other companies and industries adopt digital processes to save time and money.