These robots could help optimize your operation and enhance the work of your human employees.
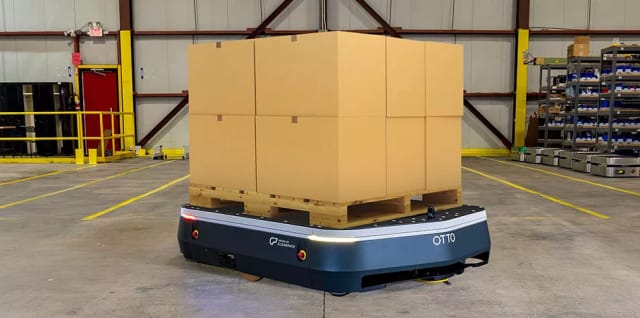
Robotics are becoming more commonplace on the factory floor—but many of these technologies are either stationary or follow paths across the facility that are predetermined, fixed and unchanging. Increasingly, however, facility operators are finding they need a robot that can understand and move through its environment on its own. That’s where an autonomous mobile robot (AMR) comes in.
AMRs navigate their environment semi- or fully autonomously. They consist of a mobile platform, most often (though not always) on wheels, and are outfitted with a wide variety of attachments or manipulators to perform specific tasks. Many AMRs use SLAM (Simultaneous Localization and Mapping) technology, which helps the robot locate itself in its environment and adapt its behaviour to dynamic situations.
AMRs can also navigate using cameras, sensors, artificial intelligence and machine vision. These technologies enable them to not only avoid collisions with machinery and people, but also to connect with other robots and digital systems to seamlessly integrate with the larger operation.
This ability to choose their own route through their environment is what sets them apart from their predecessors, autonomous guided vehicles (AGVs). AGVs follow a predetermined path to complete automated, repetitive tasks under a human operator’s supervision.
Why Adopt AMRs?
These robots can bring significant benefits to businesses in many industries. Here are a few benefits:
Worker Safety
AMRs can take on tasks that could be dangerous—or impossible—for human workers to perform. These operations range from cleaning and disinfecting areas in a laboratory, transporting dangerous materials, carrying heavy loads and working in extreme conditions that are uncomfortable or even harmful for humans.
More Flexibility
Shop floor operations don’t grind to a halt because a robot encounters a fallen box or a crowd of people. AMRs don’t need the direct supervision of an operator; they can assess and react to their environment in real time while completing their tasks—an ability that can be useful to all sorts of industries.
Boosting Productivity
AMRs tackle low-skill repetitive tasks such as transporting materials across a production floor, cleaning and package sorting. This enables employees to turn their attention to higher-value activities such as customer support or strategic planning. Employees that might have had to supervise a robot also focus on other high value work, leaving the AMR to navigate its own way around the work space.
Generating Data
An AMR doesn’t just work on its own—it is often connected to a digital platform and can communicate with other robots and company assets. The sensors they rely on to autonomously navigate generate significant amounts of performance data to help create actionable insights. This enables AMRs to also function as mobile data-gathering platforms that can empower enterprises to improve business operations from process efficiency to preventative maintenance to workforce behavior.
Types of AMRs
Because of the versatility of situations where an AMR can add value to a business, these robots come in a wide range of shapes, sizes and abilities. Here are a few broad categories of robots that could find a place in your operation:
Picking Robots
Picking AMRs identify, pick up and handle items from fixed shelves. In conventional picking, human pickers physically move from one shelf to another, picking products and placing them on conveyors, carts, or carrying them themselves. A picking AMR can take on the work of picking and transporting items between workers and stations, enabling workers to take the item they need without having to move around.
Sorting Robots
Sorting AMRs scan packages and determine where in the warehouse they need to deliver them. They autonomously plan and travel the optimal route, then deposit the package themselves or wait for a human operator to accept it.
Autonomous Forklifts
These driverless forklifts transport heavy materials across a facility. There are generally two types: a pallet jack, which can transport material from one position on the floor to another, and a pallet stacker, which stacks materials.
Inventory Robots
These robots automate inventory management. They keep track of inventory levels, product location, planogram compliance and can confirm product pricing. Inventory tracking, movement and reconciliation can be a time-consuming challenge, particularly for large-scale operations such as fulfillment centers—and inventory AMRs can track inventory with a lower chance of error than a human counterpart.
Drones
Drones are becoming increasingly common for tasks such as last-mile deliveries, autonomous inspection and even disaster response. These airborne robots perform accurate and ongoing monitoring of facilities and workforce. They can deploy high-resolution cameras and other sensors and use AI-powered software for analytics.
Autonomous Tow Tractors
These AMRs help automate the transportation of materials in dynamic and high-traffic environments. They reduce trips, particularly if they’re towing many items in cart trains; they can also help increase throughput productivity and enhance worker safety by being able to react to unexpected changes to avoid collisions.
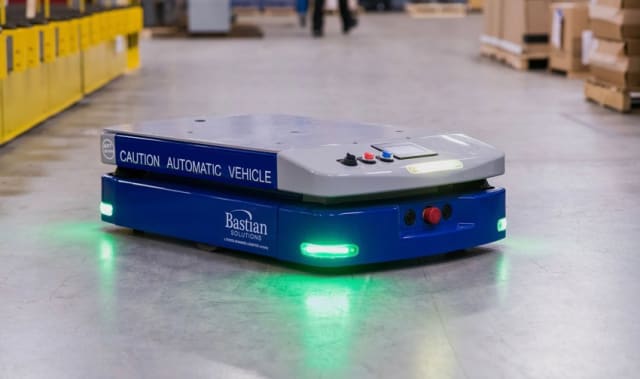
Automated Guided Carts
These robots are known for their small chassis and low profile, which enable them to fit under carts or shelves for transportation. These machines navigate small spaces with minimal or zero turn radius—and must be able to navigate around workers as well as other robots.
Cleaning Robots
These robots perform tasks such as scrubbing, mopping, vacuuming and disinfecting. Cleaning AMRs such as automated scrubbers are a relatively new entry in the market, and are becoming increasingly popular as solutions to limited work forces and skill shortages—as well as a heightened awareness of cleanliness and sanitizing as a result of COVID-19.
Industry Examples
Businesses such as warehouses, logistical companies, healthcare institutions and agricultural operations have been turning to AMRs to help them become more efficient, safe and competitive:
Warehouses
A variety of AMRs could be used in warehouse settings. Robots such as carts and forklifts can be deployed to transport raw materials to processing stations, as well as products in progress between stations and finished products to distribution centers. Other robots could be brought in to take on picking and sorting tasks, while inventory robots and even drones could track product location and movement.
Construction
Autonomous mobile robotics are already being deployed on the construction site. AMRs can be used for physically intensive work such as painting, drywall and masonry finishing. Autonomous robots can use sensors and cameras for safety and inspection—a task that drones could be particularly useful for. And AMRs can be integrated into building information modeling for large structures, producing and marking layouts onto existing floors. And an AMR is currently in development to autonomously detect and repair potholes on roads.
AMRs are being relied on more and more across a variety of sectors. With the ability to navigate and problem solve autonomously when carrying out their tasks, they unleash significant potential for increased efficiency, process optimization, data gathering and management, and worker safety. And with more operations connecting to the Internet of Things, having robots that can dynamically adapt to and enhance the work of human employees could be game changers not only for your shop floor—but your entire industry.