Simulation is becoming the norm for automation RFQs because manufacturers see the value in implementing the right way, not right away
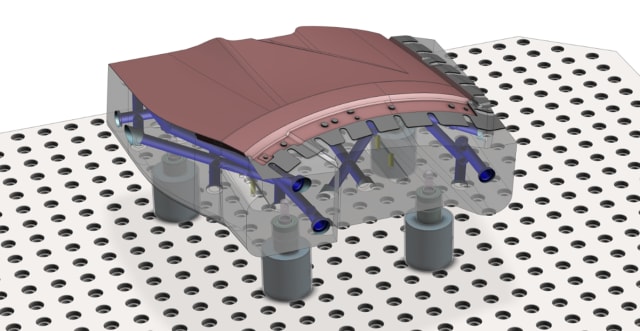
Industrial simulation is a transformative tool that can fundamentally change the way manufacturers do business—but manufacturers need to have clear goals in mind when incorporating the technology into their processes.
That was the principal message from three industry leaders who participated in a recent Association for Advancing Automation (A3) webinar.
“There are two reasons people get into advanced simulation and virtual commissioning,” said Phil Glennie, Director of Marketing and Sales at Longterm Technology Services, a manufacturing software reseller and integrator in London, Ont. “The first is that they want to. The second is that they’re forced to—and we’re finding that has really grown a lot recently.”
Virtual Commissioning
Virtual commissioning is, in essence, the practice of using virtual simulations to design, install and/or test control software in a virtual environment before implementing it in a real-world setting. In contrast, conventional commissioning involves testing directly on a physical machine or machines, a real programmable logic controller (PLC) and other physical components such as sensors and actuators.
One of the main advantages of virtual commissioning, however, is the ability to test and adjust much earlier in the development process with a digital twin—so that by the time it comes to real-world commissioning, many of the tweaks and adjustments have already been resolved.
“People are looking to technology and simulation to be able to address those earlier on in the process,” said Graham Wloch, Director if Business Development, Visual Components a developer of 3D manufacturing simulation software and solutions based in Finland. “It creates a better, more optimized situation…You can go from putting out fires and being reactive to being proactive. A lot of our customers are trying to do that, to get ahead of things and mitigate those potential issues whenever possible.”
Industrial automation is a field that moves slowly, mostly because implementing changes can be dangerous and costly. Companies are understandably conservative about making changes to their processes: the slightest misstep can result in a broken machine and potentially an injured employee.
In the past the operators of a manufacturing cell would have to determine what happens in each moment and manually program and synchronize each machine to move, or wait, at each moment—a process that can take weeks, particularly in the case of machines working closely together and moving within a fraction of an inch of each other. And while modern machines are more aware of their surroundings and adept at avoiding collisions, it’s still a laborious and expensive process.
This is how virtual simulation can be a real game-changer. A collision in a simulation won’t damage equipment and result in no lost machining time.
Simulation is Becoming the Norm for Project RFQs
Software and automation service providers are finding it increasingly common for manufacturers to include a “hard spec” request for a simulation or virtual commissioning for the job in question. While this means additional challenges for the suppliers, it brings about benefits for both the supplier and the client.
For the client, it provides a layer of control over the deliverables that they didn’t have before. In addition, the digital deliverable can be incorporated into the client’s existing digital library to update the simulation and can be repurposed in the future to reprogram lines and variables. “If you need to introduce a new product or program a line, and you have that digital twin established, you can have a person reprogram that line or re-test control logic from anywhere—they don’t have to be anywhere near the facility,” said Glennie. “It’s not just about the project being delivered, it’s about receiving the digital deliverable and weaving it into the existing digital twin of their facility.
For suppliers, it motivates—some might say forces—them to build a library of commonly used components and the schematics associated with them. It also makes it easier to check their work, including work that has been outsourced, and enables them to be more responsive to the client’s requests. It’s a particular benefit for small automation companies getting into the market; armed with simulation experts and a library they could compete on equal footing with larger, more established companies.
Implementing Industrial Automation, the Right Way
It may be tempting for a manufacturer to jump into industrial automation with both feet—after all, the benefits are clear to see. But it should be approached with caution.
“First, understand what you currently have, and then you can use it to make all sorts of changes down the line,” said Wloch. “You get your house in order, you get everything fixed and running efficiently, you figure out your bottlenecks. You might not even need automation if you just fix what you have—and if you use automation to improve it, it’s a win-win.”
Simulation software could be used to gain that understanding. Uploading any assets that were installed pre-simulation could help a company determine what works well and what needs to be improved. This could provide manufacturers with the data they need to make an informed decision about implementing the right automation tools in the right spots. “Customers who want to automate because ‘robots are cool’ don’t have the right vision and may not get to where they want to be,” said Wloch.
When examining a manufacturer’s existing assets and processes, it’s important to have good coaching and a skilled partner who can help guide it towards the right purchase and help the manufacturer build in-house capability to operate and maximize the technology’s effectiveness. Some software provides comprehensive services that includes factors beyond just automation, and others provide specific solutions such as robot motion software—and it’s vital for a company to choose the right fit.
In addition, while industrial robots are all very similar in how they function, they are very different in how they are actually programmed. Each vendor has a different way of programming their machines, which means a company needs to rely on people with expertise in multiple robot brands. Having different experts work in the same simulated virtual space enables them to work together to resolve those differences and align their products to work with each other efficiently before installing the machines next to each other in the real world. As a result, the manufacturer can spend less time worrying about which robots they have, and more time focusing on using the technologies to meet the company’s broader objectives.
The benefits of simulation are often scalable as well. The efficiencies gained from simulating one particular variable can be used again the next time that process is updated or enhanced, and potentially applied to other processes and manufacturing cells—it’s not a one-time benefit.
Making Manufacturers More Agile
Industrial simulation can enable manufacturers to respond to the increased demand for flexibility in their operations. It can also help build supply chain resiliency.
Manufacturing processes have conventionally been built with eye on simplicity: a manufacturing cell was built to work for many years, with incremental changes being implemented along the way. But today’s market requires more flexibility, and manufacturers are responding by implementing complex cells that offer more flexibility, that allow for smaller batch production and even allow for producing multiple products in the same cell. While this results in a more agile process, it increases the complexity of the program. “If you’re trying to be more flexible and agile with traditional ways you’ll quickly reach a wall you can’t get past,” said Alejandro Soler Fenoll, Senior Manager of Applications Engineering, Realtime Robotics, a Boston-based automation control software developer. “Customers are hungry for flexibility, they want very dynamic cells that they can repurposed in shorter periods [of operation].”
Industrial simulation has significant potential to transform the way manufacturers do business. “You’re still looking at a change that is on the level of [the transition from] paper drawings to CAD,” said Glennie.
The technology can help make companies more efficient in how they develop products and bring them to market, and it can help build resilience and agility to deal with new challenges and plan for future growth. The key is to approach this transformation with a clear vision of what the company has and needs, and a clear end result in mind.