Newly developed software crunches the numbers to help determine if conventional or additive manufacturing is best suited for the job.
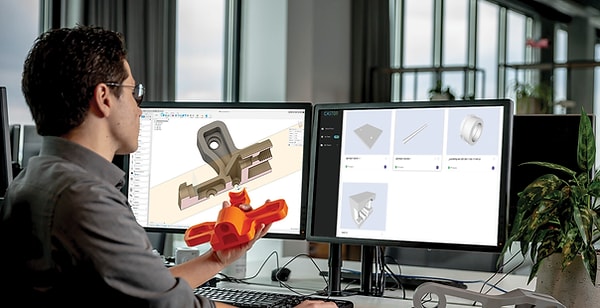
One of a manufacturer’s most important decisions could be to determine which production technology is the best one to manufacture their part. Does it make sense to stick with the traditional manufacturing processes or make the jump to new technologies such as 3D printing? That decision has many factors: part design, budget, complexity of the component, weight, number of parts to produce, how many parts to keep in the warehouse, carbon emissions, lead times and more.
Most design software can help inform these decisions based on design and material data, but industry is starting to see a new generation of new software developed specifically as a decision support tool for industrial manufacturers that automatically analyze a component’s design to determine if, and how, additive manufacturing is the solution to produce the part.
“We enable manufacturers to decide whether to use additive manufacturing over traditional manufacturing methods when it can save them time or money, reduced carbon emissions or provide a supply chain benefit,” says Omer Blaier, co-founder and chief executive officer of Castor, an Israeli software developer that’s trying to take some of the guesswork and intuition out of this decision-making process. “We’re not the doctors. We’re giving tools to the doctors to take better decisions,” he says.
Inputs for Output
The software analyzes a variety of files, including cut files, computer aided design (CAD) files and 2D drawings—not only on a technical level but also a financial level. This type of software performs this analysis at scale as well, looking at large numbers of files at the same time.
“You can upload the whole dashboard of a car, the whole inventory list of spare parts, the whole assembly or sub-assembly of a machine that a manufacturer wants to optimize,” said Blaier, adding that the software will assess whether it makes sense to use additive manufacturing to produce some or all of these parts or if traditional subtractive manufacturing is still the best option.
Castor can analyze thousands of parts at once and identify opportunities to change the design of certain parts if that makes using additive manufacturing to manufacture them more desirable. “For example, it will recommend to combine multiple parts into one or to make parts hollow if it thinks that additive manufacturing can create a change in the weight of a part,” says Blaier.
Tool maker Stanley Black and Decker was looking for a more efficient and profitable process for manufacturing one of its low-volume, high-complexity parts, which was made from highly customized components. Refining and innovating those components would usually take about eight weeks per iteration using traditional manufacturing processes.
The company tried Castor to find a better way to make the parts, using the software as a decision support system for identifying where additive manufacturing would be a viable alternative. The software provided a technical and cost-saving analysis for a full machine design, including recommendations for which 3D printing style, printer and printing material were most suitable for the part’s mechanical properties.
“[It] played a fundamental role in the process which led to the integration
of the first 3D printed metal production part at Stanley Black and Decker,” says Moses Pezarkar, Manufacturing Engineer at Stanley Black and Decker.
“The hardware is there already,” says Blaier. “Additive manufacturing equipment such as 3D printers can do amazing things, but the software, the applications, are lacking a way to determine how to use the benefits of these new manufacturing techniques.”
Combining technical and financial analysis is particularly innovative approach. Blaier says the software is 50 per cent technical analysis and 50 per cent economic analysis and can be customized to take into account a wide range of financial variables. “Companies can change the software to work according to the titanium price they know today, according to the hourly rate they pay today to their engineers, the electricity cost they pay today in their manufacturing technique, and the analysis is aligned with their customized input,” says Blaier. “They can use our defaults based on our experience from 50,000 parts we’ve finalized, or they can customize it to align with their manufacturing approach in general.”
Synthesizing technical and economic data bridges gaps that often occur between the design team and the production team which can lead to delays and rising costs.
“When you show the financial benefit to the production engineer, procurement manager, VP of engineering and even supply chain managers—people that have to do with the business side of things—then you have a good case to convince a design engineer that maybe his design might either be suitable as is or with some changes to adopt a different manufacturing technique than he designed the part for,” says Blaier.
Decision support software such as Castor informs those discussions and decisions before a company embarks on a project to transform their manufacturing processes. Seeing the benefits and challenges of additive manufacturing tailored to the company’s available resources and short- and long-term objectives can be invaluable.
This type of decision-making value is not lost on the major software developers, According to Blaier, Castor is embedded as part of platforms such as Siemens’ Teamcenter PLM, Materialise’s CO-AM platform and Ultimaker’s Digital Factory. Blaier says companies understand that there is a need for this type of parts-and-process identification tool before you deep dive into additive manufacturing processes.
On The Right Track
Another sign that castor is one the right track in terms of helping solve these issues was its selection as a winner of Hexagon’s Sixth Sense challenge program, which helps startups bring their products to wider markets and scale their business. Hexagon identifies high-priority economic, environmental and consumer challenges and asks companies to submit applications to describe how their products and services respond to those challenges.
“Castor is a great example of a start-up we want to support,” says Milan Kocić, Head of Hexagon’s Sixth Sense. “The unique solution is helping companies scale additive manufacturing operations, become more sustainable, cut costs and improve supply chain resiliency. By combining expertise and resources, we’re aiming to help Castor scale and make a real impact on industry.”
Today, manufacturers understand additive manufacturing has the potential to transform their operations, make them more efficient and responsive to the market, innovate and remain competitive. However, the real challenge is in determining when and how to integrate emerging technologies such as 3D printing into the shop floor in the most effective way. Software such as Castor enables companies to tap into the disruptive potential of additive manufacturing in a manner that is tailored to their specific needs and objectives.