Agricultural drone design gets a boost with CAD.
Drones are pretty awesome and so is CAD. My background is in aerospace design engineering, so I can be expected to say that. I may be a little biased on the subject.
What I particularly like about the unmanned aerial systems (UAS) field is how the technology is increasingly being directed toward more humanitarian and beneficial applications. More and more companies are realizing that drones can be used for good, and one such company is U.S.-based Skybridge UAS, which is using its wealth of aerospace experience to develop drones for precision farming.
Precision Farming 101
A critical component of precision farming is the collection of high quality data to inform farmers about the conditions of their crops.
For decades, we have been aware that plants and crops reflect light in different parts of the spectrum, depending on their conditions. For example, live healthy plants absorb light in the visible spectrum (particularly red and blue) but reflect a lot of green light. This is why plants are green. But switch over to near infrared (NIR) and those same healthy plants reemit approximately 50 percent of their absorbed solar energy in the NIR portion of the spectrum. This is an evolutionary trait of plants—reemitting this light prevents them from overheating and dying.
The end result is that plants appear pretty dark in the visual spectrum, but when viewed with NIR cameras, they light up like a Christmas tree. They are very bright. Other information can be gauged from the nonvisual spectrum too. Freshly cut (or damaged) plants can ooze water from a cut or broken stem, and this appears as a different shade in a NIR/false color image. Conversely, sick or dry plants may reflect less NIR radiation back, so they will appear darker than healthy plants.
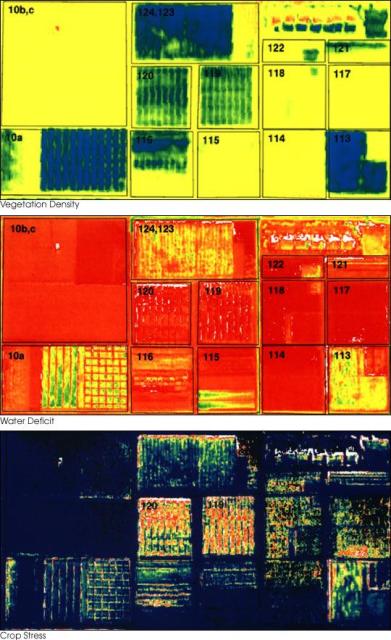
All of this information can be used to (literally) paint a better picture of a farm area using geographical information systems (GIS) software combined with GPS data, and can then be presented to a farmer to inform them of the situation on the ground. The farmer can then vary the amount of water or fertilizer, or even relocate crops, according to the optimal conditions. Variability is the key word here: gone are the days of just watering a field equally. With precision farming, sensor feedback is used to allocate resources where they are needed. This can potentially result in increases of up to 200 percent in terms of crop yield, which is very good news indeed.
However, boosting crop yield is only one side of the coin. On the flip side is loss prevention; and so far, Skybridge has demonstrated some impressive figures in that regard. By using the same methods mentioned above, Skybridge has shown that early detection of damaged plants can allow farmers to take corrective action before the problem spirals out of control.
In Figure 1 below, we can see the early warning signs of crop damage resulting from a pivot nozzle issue. Center pivot irrigation is a highly efficient irrigation technique that can be compared to a giant water sprinkler covering large areas of crops with water. Any blockages or issues with the system can result in plants not receiving the prescribed amount of water and this can manifest itself as lighter-colored rings on the thermal infrared maps. Depending on the scale, those underfed plants can result in huge financial losses through damaged crops.
In the example below, early intervention has saved the farmer from losing 9.1 acres of crop at 25 bushels per acre from a 56-acre farm. That’s 16 percent of the total crop! On this scale, that could have resulted in a potential loss of USD$1,362. However, if you scale that up to a 3,000-acre farm, a loss of 16 percent of the yield would result in a loss of $450,000.
The cost of scanning the field with Skybridge is just $1.50 per acre. Using the example above, a farmer would spend $4,500 on a 3,000-acre farm in order to save nearly half a million dollars—which most would likely consider a solid investment.
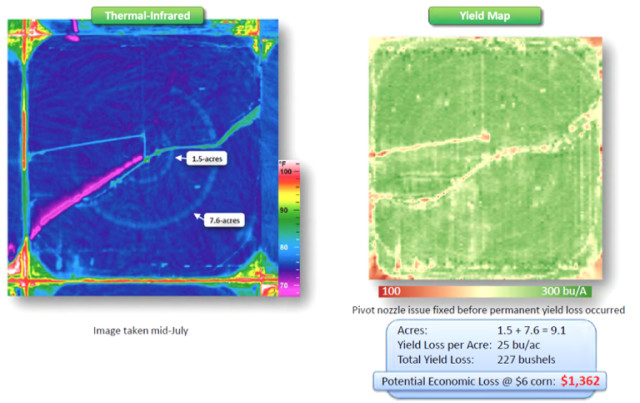
Skybridge UAS: Mil-Spec Drones for Good
Let’s be clear. The Skybridge drones are not your average off-the-shelf quadcopters. They are fixed-wing, petrol-driven birds with high operational ceilings, long loiter times, large payload capacity and military-grade flight controllers. And because of these high specs, Skybridge is not in the habit of selling these drones to the public. Instead, the South Carolina–based start-up is actually a service provider that makes its bread and butter by providing full service data collection and post-processing, scanning crop acreage and helping farms prevent loss.
The propulsion system is a petrol-driven propeller, which has been designed from commercial off-the-shelf (COTS) hardware. This engine combined with the custom-built airframe allows for a payload of up to 12 hours with a full sensor package of 25 lbs, or up to 100 hours with the full wing fuel tanks and minimum sensor package.
These impressive feats of endurance have all been realized with the use of CAD and CFD analysis in the form of FLUENT in the early stages, allowing Skybridge to optimize the design according to customer requirements, rather than making a trade-off from repurposed designs. It is in effect a bespoke industrial-grade drone with the brain of a military drone.
In fact, Ian Henderson, a founder of Skybridge, told me that the company plans to employ former U.S. military pilots to fly the drones, because this level of technology can best be harnessed by pilots who are experienced with Mil-Spec gear.
Specifications
- Maximum weight: 50 lbs depending on sensor payload
- Speed range: 35 mph to 100 mph
- Maximum endurance: 80 hours
- Maximum range: 3,500 statute miles
- Low altitude operation: 500 to 2,000 ft
- UAV equipped with both fully autonomous and piloted operation; waypoint navigation, return to base, auto land and auto takeoff
- No special launch or recovery systems needed
- Can be FAA Certified when necessary
- Continuous, real-time data stream as well as recorded data
- Customized data analysis and presentation software of sensor data available and fully developed
Sensors Available
- Multi-spectral IR (precision agriculture)
- High definition visual and IR (animal location, fire location day and night)
- Synthetic aperture radar (water location through the forest canopy)
- LIDAR (precision topological data gathering)
- Tagging system (animal tracking)
Solid Edge
Aerospace design would be a very different beast without the use of CAD. Skybridge UAS is well aware of this and has opted to use Solid Edge for its design work.
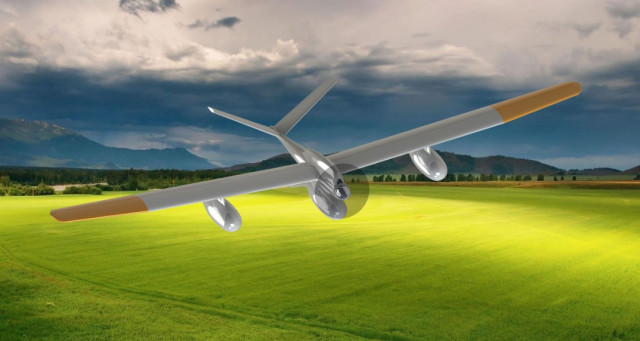
Because Skybridge UAS is a small startup with just three CAD seats in house, the company was eligible to receive a free year of Solid Edge software through Siemens PLM Software’s Solid Edge Startup Program.
“One of the largest struggles of a startup is obtaining adequate funding—and engineering, specifically enabled by a CAD tool, is the cornerstone of bringing the concept to reality,” said Henderson. “I see Siemens as a partner and investor in our company.”
Even when the program’s benefits expire, Henderson said, it makes sense to use Solid Edge because its monthly subscription allows users to suspend the subscription and to resume it on an ad hoc basis. This is good for periods of actual engineering, when three design seats may not be fully utilized. In these instances, only one seat can be left running and the company doesn’t have to worry about paying fees for redundant workstations. And when design phases ramp up again, the company can just reactivate the subscriptions and boost its CAD capability.
Henderson added that another benefit of using Solid Edge is synchronous technology, which allows users to add relations to the design, at any time and in any order. This makes the design more responsive to changes, and allows changes in assembly to respond dynamically to changes within individual parts, which vastly increases productivity.
Manufacturing
Skybridge UAS’ flagship drone model, the SB 1-2, is manufactured from a variety of composites and plastics, most of which have been designed in Solid Edge. The airframe is mostly carbon fiber, with the design work performed on site and the CAD models sent to a vendor in California for the layup, forming and autoclave work. In addition, Skybridge makes use of 3D printing for its landing skids, which are constructed from nylon. Assembly is performed on site.
Future Goals
Skybridge UAS has just received round one funding and is now looking for round two funding. The short-term goal is to begin the rollout of its agricultural service for the U.S. in early 2017.
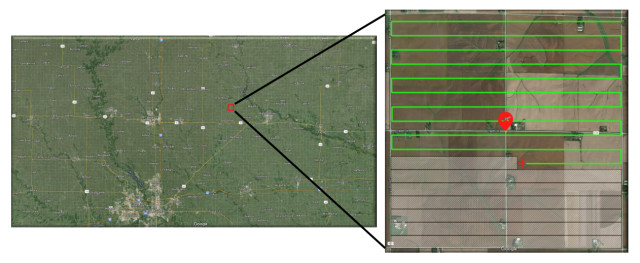
Beyond that, it is aiming for expanding globally and hope to offer services such as wildlife monitoring in Africa, olive grove monitoring in Spain and oil and gas pipeline inspections around the world (circa 2018).
And as Skybridge UAS is currently entering the round two funding phase, Henderson assured me that it is most definitely open to investors.
All in all, we can say good luck to Skybridge UAS. It’s always nice to see positive applications for drone technology.