Four basic stages that small manufacturers should follow to optimize their investment in automation.
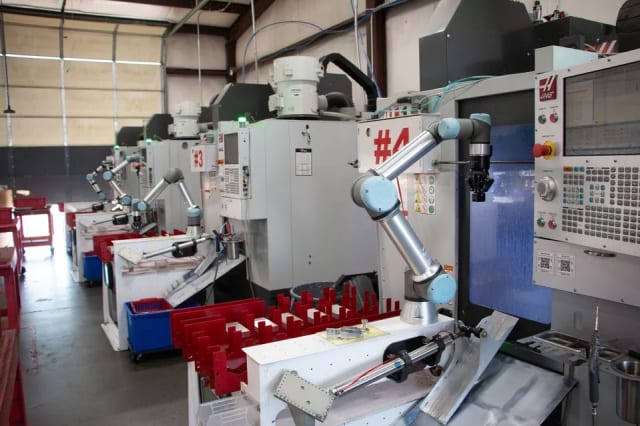
The rise of Industry 4.0 has brought technological transformation to many metalworking companies—particularly in the form of automation. However, not every company has the resources for a wholesale overhaul to fully automate its shop floor.
This doesn’t mean small metalworking companies are destined to miss out on the benefits of automation, though. By taking a few deliberate, strategic steps, these companies can successfully integrate automation into their business.
This roadmap shows how it can be done.
Broadly, there are four main stages of the automation journey that small manufacturers can follow to maximize their investment dollars in automation.
Stage One: Quick Wins
This is the most basic level of automation: tweaking existing processes with automation. This stage isn’t about transformation, it’s about using automation to enhance the processes already in place to resolve bottlenecks, improving the productivity of workers and the machines already in the shop.
“The very first thing shop managers need to do when it comes to automation is identify the exact process that’s most worth automating,” said Justin Geach, Global Director of Marketing at Master Fluid Solutions, an Ohio-based company that supplies metalworking fluid products and support to the global metalworking community.
“What we often see as most successful with our customers is automating processes and tasks that are easily repeatable and need to be performed all the time, since those are the processes that usually achieve the fastest return on investment (ROI). For that reason, we recommend automating some of the more basic but critical tasks such as part loading and unloading and tool breakage detection or coolant fill systems to enable lights-out production.”
There is no shortage of tasks that can be automated in a metalworking operation; that’s why it’s essential for small businesses to identify the most important task to automate first.
In fact, the first step may not be related to the shop floor at all—but may be found the office: “in the early stages, the best place to start is with software to automate business processes and record keeping,” said Geach.
By targeting a specific problem or bottleneck and investing in automating it, the returns on that investment can be used to implement further automation. Those returns can manifest themselves quickly after making that first step. Workers benefit from increased efficiency; an automated process enables them to focus on higher priority tasks and accomplish them with less effort and strain, leading to improved job satisfaction. Higher productivity can also result in higher throughput, faster time-to-part and time-to-market and improved profit margins.
It can be beneficial to bring in an automation specialist to help guide the process. “Working with an automation consultant can help shop managers plan out long-term goals and ensure they’re investing in the right equipment each step of the way,” said Geach. “Investing in automation can be a big expense for small businesses, so gaining an outside perspective from a consultant or well-regarded automation installer is a great place to start.”
Stage Two: Partial Shop Automation
Once a manufacturer implements some basic automation processes, it’s time to start connecting them together into a bigger picture. In this stage, equipment and robots work together to perform multiple tasks in longer workflows, reducing the number of manual touchpoints along the way. By eliminating significant waste and boosting productivity.
“For partial automation, we can recommend machine part loading and unloading systems for the higher production parts to enable lights-out manufacturing,” said Geach. “Keep in mind these systems should be flexible in order to quickly adapt to new jobs, as parts can frequently change in small business and job shops. Invest in basic equipment and systems to minimize bottlenecks in your production.”
It’s important for companies to avoid investing in the wrong kind of automation—to really take care to find the right fit of technology for the business. “For example, fully autonomous robotic systems are usually not necessary for small metalworking shops because there is often too much process variation to make large scale automation feasible,” said Geach. “Large scale robotic and material transfer systems may be better suited to production manufacturers.”
Another pitfall to avoid is not having the right personnel to install, program and troubleshoot automation equipment. Provide workers with incentives and opportunities to train in these areas to enhance their skillsets, grow their careers and continue providing value to the company.
Stage Three: Extensive Automation
The next step is to further integrate automated processes into a comprehensive operations-wide process, where most of the processes are automated by robots and other Industry 4.0 technologies, and where products can move automatically between stations with minimal worker interaction. “Later on in the process, it might make sense to expand to more advanced automation, depending on business and facility needs,” said Geach.
This high level of automation can benefit a wide variety of metalworking companies, helping to significantly enhance productivity and throughput. It also has the potential to create a virtuous circle, where improvements to the company’s bottom line enable further adoption of Industry 4.0 enhancements.
Stage Four: Full Automation
This final stage involves full automation of a metalworking shop, where all operations flow seamlessly in a single, fully integrated workflow with minimal to no manual touchpoints. Full automation enables a continuously improving operation with no wasted materials or steps and can contribute to a circular economy.
While this may not be the end game for every company, it does model the efficiencies that automation can bring to a metalworking company, enabling the company to determine the level of automation that best suits its business objectives.
Ensuring Employees are On Board
Throughout the process, it is crucially important to keep workers engaged in the transformation. They may recognize that automation can increase productivity, free up employees from repetitive tasks, and reduce the need for humans to work in potentially hazardous environments. But some of those workers may be concerned that robots will be taking their jobs.
A company looking to automate needs to approach the technology with the mindset of making better use of human employees rather than replacing them. The company’s workforce will be important partners in maintaining, implementing and monitoring the automation technologies being introduced.
“Automation should be understood as a complement to your existing workforce—not something to disrupt or replace them,” said Geach. “That’s why it’s important to implement automation at a sustainable pace. Investing in too much technology up front could overwhelm employees and lead to improper implementation, impacting overall ROI.”
A workforce can be resistant to change, particularly if it disrupts processes that workers have been using for a long time or requires a significant overhaul of the way they work. Geach recommends centering the discussion with employees around the ways automation will benefit them in their jobs—making it more than just how it affects the company’s bottom line. “Automation makes people’s lives easier so there are often a lot of positive aspects to highlight for frontline workers…it provides a learning experience to build skills for the future if employees want to take on the new challenges. It can also allow them to work on more meaningful projects and jobs.” He stresses that it’s also important to be upfront in addressing any fears about job cuts or how automation could impact their security. “Discuss the implementation roadmap so employees know what changes to expect to their processes, and when,” he said.
If You Fail to Plan, You Plan to Fail
While automation is complex, it is possible to implement it in a realistic and productive manner. This requires a thorough plan from the outset. “The most important thing to keep in mind about automation, especially for small businesses with limited budgets and resources, is simply to have a plan and know exactly what you want to accomplish with it,” said Geach. “Identify specific goals you want to achieve and then invest in technology accordingly.”