Rockwell Automation’s Industrial Decarbonization report outlines a pathway to decarbonization that benefits both the bottom line and the planet.
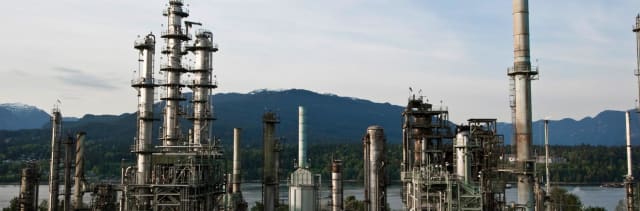
The global economy is under intense pressure to move to a net zero-carbon model—and industrial manufacturers have the potential to play a crucial role in achieving that ambitious objective. In fact, automation may provide innovative solutions that enable manufacturers to be commercially and environmentally successful.
Rockwell Automation, a supplier of industrial control and automation solutions, outlines how manufacturers can use Industry 4.0 technologies—and the rich data they can generate—to support energy transition to net zero carbon in its Industrial Decarbonization report.
“Decarbonization will be a story of innovation and optimization,” said Steffen Zendler, process industry strategy and marketing manager at Rockwell Automation. “Our customers have an installed base from which they need to earn profits today to invest in the energy transition tomorrow. Process efficiency is key to balance these competing ambitions.”
Companies can start this ambitious process by identifying what the report calls “zones of convergence,” where actions taken to increase operational efficiencies and reduce costs can also lower emissions—achieving quick wins that don’t negatively impact their ability to compete in the market. The report outlines five pathways for manufacturers to identify those zones of convergence, balancing the need to remain competitive with the need to reduce ecological impact of their operations.
The five pathways are:
- Energy efficiency: optimizing energy use and reducing energy consumption enables industrial companies to cut costs while reducing carbon emissions. The report points out that the majority of industrial greenhouse gas (GHG) emissions result from burning fossil fuels for energy.
- Extending asset lifespan: as equipment ages it becomes more susceptible to breakdowns and energy use inefficiencies. Improved asset optimization, including automation measures such as predictive maintenance and bringing legacy assets into a company’s digital platform, can help reduce costs and downtime, and reduce energy consumption.
- Optimizing inputs and resource use: Industrial processes can be quite energy- and natural resource-hungry, resulting in a large carbon footprint. Optimizing production processes, and identifying opportunities for efficiency and waste reduction, allow manufacturers to use only the materials they need in the most effective manner.
- Faster responses to incidents: A machine or process failure on the shop floor can have significant environmental consequences and result in an increase of emissions. Implementing IoT-based solutions such as sensors and alerts can enable operators to solve potential problems before they manifest, or respond more quickly and effectively to unexpected breakdowns.
- Reducing need for on-site staff: The less people needed on site, the less cost involved and emissions generated in transporting them to and from the work site. This is particularly true of industries that currently need operators in remote or sensitive locations, such as offshore oil, where those costs are magnified.
Any one of these pathways has the potential to enable industrial manufacturers to achieve efficiencies throughout their operations—but will require a thorough review of the way they manage their business. “Industrial processes will need to be reassessed and improved to increase efficiency, reduce virgin material use, and drive down GHG emissions across the industrial value chain,” according to the report.
Harnessing Data to Reach Decarbonization Goals
To achieve these objectives, and to maximize the potential of Industry 4.0 technologies, companies will need to generate, harness and gain insight from data throughout their operations. But this presents a particular challenge for industry, since many industrial manufacturers still gather data the old-fashioned way via pen and paper and input it into spreadsheets or systems that don’t necessarily communicate across the enterprise.
However, Industry 4.0 does offer solutions that can address those concerns. Internet of Things-based sensors can track variables such as energy use, emissions levels and others, often in real time. That data can be processed and used to identify opportunities to increase efficiency, reduce emissions, lower resource use and reduce costs. In turn, the data can be used to inform where and how automation is implemented across the production process. If done properly, it can create a virtuous circle: these improvements can generate more data, which in turn can be used to find further efficiencies.
In fact, automating operations can provide the context and insight needed to implement sustainable change, enable faster responses to problems, free up workers for higher-value tasks—including reducing the number of people required on site—and reduce the potential for error not only for internal business processes but also in preparing emissions disclosures to regulators. And while that amount of data is difficult if not impossible for individual employees to stay on top of, Industry 4.0 technologies such as machine learning and artificial intelligence can be deployed to support data analysis and business decision-making.
“Our customers really want to understand which activity would derive the greatest return on their investment and the largest in terms of reduction for emissions,” says Anissa Thomas, Global Sustainability Leader at Sensia Global, in the report. “Within each stage of the customer sustainability journey, there’s a common thread for digitalization: connecting disparate assets, visualization, and contextualization of data to improve decision making and drive automated workflows. We refer to this as ‘intelligent action.’ Sustainable operations are driven by intelligent action.”
Powering the Decarbonized Economy
A big factor in decarbonization will be the shift from fossil fuels to renewable energy sources—as well as capturing, storing or using industrial emissions in situations where alternative power sources aren’t feasible. Critical infrastructure is needed—asap—to support the transition away from burning fossil fuels. As well, proven and reliable automation technologies will be needed to enable manufacturers to capitalize on the potential of renewables.
New skillsets will be needed to support this transition, alongside infrastructure and new technology. In fact, it is estimated to need 22.7 million new jobs. Industry 4.0 can help companies meet that demand by deploying automation measures to take on some of the work wherever possible, support training for workers who will be performing new tasks and ensuring that operating procedures stay consistent during the transition.
The report focuses on one particular renewable energy source: hydrogen, which is not dependent on sunshine or wind. Green hydrogen has the potential to be a viable alternative to fossil fuels for industries that employ high heat in their processes—such as cement production and iron smelting—and which may find transitioning to electricity difficult if not impossible.
The International Energy Agency (IEA) estimates that renewable energy sources will need to provide 90 per cent of the world’s power by 2050—and an investment of $4 trillion by 2030 will be required to make this possible. While this seems to be a daunting goal, companies are already creating innovative solutions to the challenge: according to the IEA, many of the technologies required to reduce emissions are already at the demonstration or prototype phase today.
The companies that can leverage innovative solutions to reduce emissions, increase production to meet growing demand, and maintain a healthy profit margin will be the ones poised to succeed in the economy of the future—and existing Industry 4.0 technologies for automation and process optimization promise to power those innovations and help boost the bottom line of those companies. Is your company one of them?