Surfaces best for modeling curvy shapes
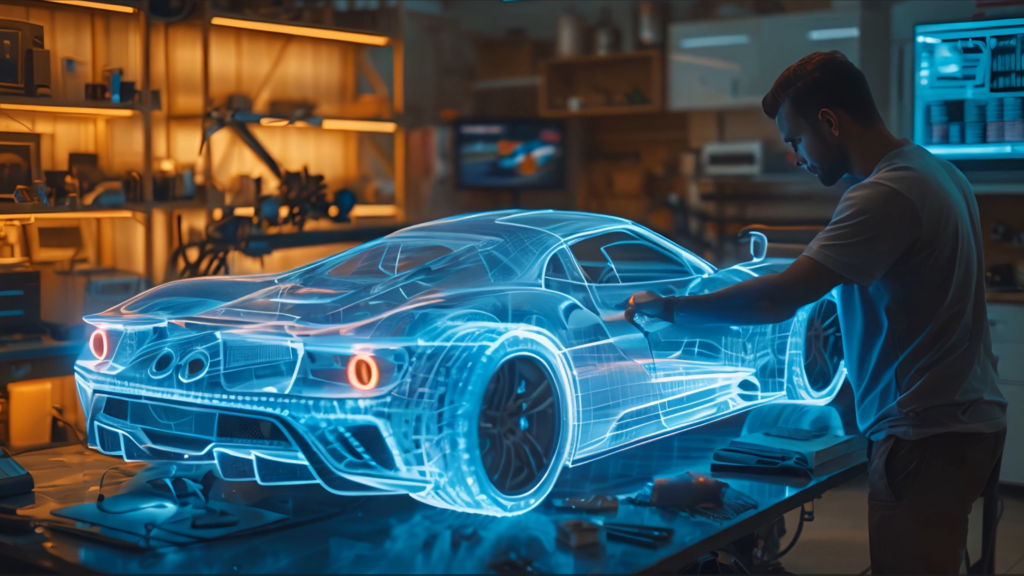
There are at least six ways that 3D objects can be modeled with computer software. What makes one of them, surface modeling, so special?
- Points
- Lines, arcs, edges, also known as wireframes
- Faceted surfaces
- Smooth surfaces
- Photogrammetry
- Solids
Here, we focus on surface modeling. First, let’s look at all the advantages surfaces have over other methods.
1. Smooth shapes
When a smooth, organic or curvy shape is to be modeled, a surface modeler comes in quite handy. This makes surface modeling software the preferred tool for industrial design, automotive designers and the streamlined shapes that the aerospace industry demands.
But beware: not all surface modelers deal in smooth shapes. Some surface models are faceted. Just like the facets on a diamond, the shape is composed of a collection of flat faces, either triangular or quadrilateral. For example, there is the TIN (triangular irregular network) that civil engineers use to model terrain by representing it as a mesh. That’s fine for projects measured on a big scale, such as miles. Brilliant is the program that is able to interpret the billions of point from a LiDAR scan, like the stars in the sky, as a patchwork quilt that drapes the Earth, but…
It’s not smooth.
Nor are the 3D prints made using STL files, also faceted models. That may be fine for a 3D print if the facets are small enough, but often, 3D-printed parts require a secondary operation to smooth out the edges a faceted modeler produces.
But to make surfaces that are truly curvaceous and smooth, with one blending into another in a way that is most pleasing to the eye, that requires higher-order mathematics. When an automotive body panel has to blend into another so smoothly that not even a reflection will reveal the blend, that is when we have found the Holy Grail: Class A surfaces (more on that later).
2. Easy to change shape
Most surface modelers used to make smooth shapes rely on polynomial curves called B-splines. Surfaces can be adjusted by manipulating the splines or the surface itself. For example, if a surface patch does not produce a pleasing blend from one area to another, such as on an automotive door panel, a user can adjust the control points of the splines until satisfied.
3. Precision
A surface can be blended and shaped with mathematical precision instead of relying on hit-or-miss visual techniques, such as adding or subtracting solid shapes. There’s also no need to make ultimate smoothness the task of manufacturing, as was done with lofting, when section cuts were drawn at regular intervals along the length of a ship and it was up to the boatmaker to make sure the final shape was smooth. Or the machinist’s file to smooth over the facets made from a STL file.
4. Visualization
The stunning images of automobiles we see on screens or pages are often not made with a camera but with a surface modeler or a hybrid surface-solid modeler. Surface modeling produces Class-A surfaces, the smoothest of all surfaces, which, after they have been textured and rendered, look so realistic that they are difficult to distinguish from a photograph.
Here are the disadvantages of surface modeling.
1. Not the easiest to use
Surface modeling takes more time and effort to master. Advanced surface modeling is no child’s play. Proficiency with surface modeling usually requires training and, almost always, considerable experience.
2. No mass
Surface models are only skin-deep. Only the surface with zero thickness is defined. A surface model can completely and precisely enclose a space (be watertight) and yet not know the volume of the space, like a stomach that doesn’t know it’s full. This limitation is overcome with a hybrid modeler, which combines a surface and solid modeler.
3. No interference
If a surface intersects with another, it can be used like knife to cut it. However, if a surface is completely enclosed by another, it can be of no use. For example, if you would like to make a hollow sphere by subtracting a small sphere from a larger one, you can’t do it with surfaces. The smaller sphere will exist in a vacuum, not in contact with the bigger sphere. However, spheres made with a solid modeler will have their interiors completely defined, as if they were full of matter. You can subtract the smaller solid sphere from the bigger solid sphere and get a hollow sphere (technically still a solid).
Solid models, with their precise internal definition, are therefore better suited to prevent “clashes,” what unintended intersections are called when one pipe “interferes” with another pipe or with the structure of the building, for example. Commercial building and process plant designers find such “clash detection” invaluable in preventing rework and downtime on the site.