Columnist Wayne Schaefer highlights processes to document and report quality issues to management and beyond
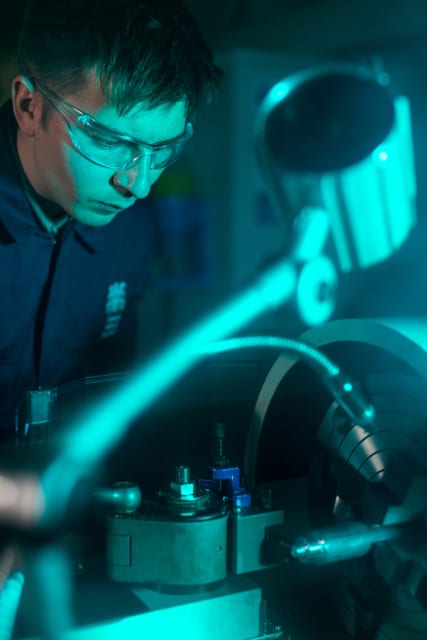
Engineering and management decisions leading to catastrophic equipment failures have been at the forefront of the news again recently. Within the realms of automotive, aviation, or even space industries, engineers encounter important decisions, often daily, that may significantly influence the outcome of a project. They have an ethical duty to guarantee that the products they are responsible for not only meet but surpass the established norms for design and safety. This responsibility could include products that engineers have knowledge of but are not directly involved with as well.
What happens when a safety or quality discovery is made that is not addressed after following normal company procedures? It’s important to remember that while standing up for safety and quality is commendable, it’s also essential to assess the potential risks to your career and prepare accordingly. Engineers must be prepared for times when management may not be receptive to the required changes. In those cases, you’ll need to decide whether you can continue working under those conditions or if it might be better to look for opportunities elsewhere where your commitment to quality is valued.
I wish I could say the path forward is always clear-cut; however, engineers must navigate the delicate balance between loyalty to their employers and their paramount duty to the public and the environment. In moments of conflict, it is essential for engineers to lean on the principles of integrity, accountability, and the pursuit of excellence. Documenting issues and seeking advice from external sources are some steps that can be taken without immediately jeopardizing one’s career. One of the golden rules of engineering is to never present a problem without having prepared several solutions. Let’s explore some talking points to aid the process.
Identify Specific Quality Issues
Start by clearly defining the safety or quality issues you’ve observed. These could be anything from recurring defects in products, deviations from specifications in materials or processes, to software bugs that affect user experience. It is vital to be specific about the description of the issue, where and when it occurs, and its frequency. It’s essential to identify the potential risks associated with the discovery.
Collect Quantitative Data
Gathering good quantitative data is crucial as it provides objective evidence that can be measured and analyzed. Documentation is a detailed and systematic approach to collecting, analyzing, and presenting data that substantiates the quality or safety issue you’ve identified. The same data can also be used to determine if remediation has been successful. This can include:
- Defect rates: number and types of identified defects.
- Performance metrics: possible deviations measured against benchmarks.
- Reliability statistics: failure rates (mean time between failures and possibly time to repair)
Compile Qualitative Feedback
Qualitative data is just as important and should not be overlooked. While more subjective, this information can provide insights into the user experience and potential areas for improvement. This can include:
- Customer Feedback: includes complaints, product reviews and suggestions.
- Employee Observations: encourage team members to report any issues they encounter in the production process or during their routine duties.
Utilize Diagnostic Tools
In engineering, various tools can help diagnose quality issues. For manufacturing, tools like fault tree analysis (FTA), failure mode and effects analysis (FMEA), and statistical process control (SPC) can be invaluable.
Document Everything
Documentation is of vital importance here. You must create a comprehensive report that includes:
- Detailed Descriptions: Describe each quality issue in detail, including when and where it was observed.
- Supporting Data: Present your quantitative data and qualitative feedback clearly. Use charts, graphs and tables to make your data accessible and understandable.
- Comparative Analysis: If possible, show trends over time or comparisons to industry benchmarks to highlight the severity of the issue.
Propose Preliminary Solutions
As mentioned earlier, never present a problem without a suggested solution. While your primary goal is to highlight issues, suggesting preliminary solutions or areas for further investigation can demonstrate a proactive approach and commitment to quality improvement. This could include recommending specific diagnostic tests, suggesting process changes, or identifying areas for further research. Presenting solutions also adds credibility to any concerns raised and can be instrumental in convincing management to embrace the solution. The profession of engineering, after all, is about solving problems, not just finding them.
Prepare for your Presentation
Depending on the seriousness of the identified problem, engineers can be called upon to present their finding and support or defend the necessary solution. This includes anticipating questions or objections from management and being prepared with responses. Practice presenting your findings succinctly and confidently, focusing on the evidence and its implications for the business. Focus on how the solution supports the company business goals in a supportive and non-confrontation environment.
By taking a thorough and analytical approach to gathering evidence, you can build a compelling case that clearly communicates the quality issues to management from an engineering perspective. This evidence-based approach not only makes your concerns harder to ignore but also positions you as a problem-solver committed to the company’s success.
A Personal Experience:
In the late 1980’s, as industry was starting implement changes to Estop Circuits, CNC equipment manufactures were slow to embrace the concept that teach pendants, just like their robot counterparts, should be outfitted with hardwired Estop and Enable Switches (also known as Live-man or Hold-to-Run switches). I was a relatively new engineer working for a large automotive company but I was also one to speak my mind. It was my belief that, given the similarities between robotic and CNC systems, the robot specification on teach pendants should be applied. As you can imagine, my youth and relative inexperience did not give me much credibility in winning my argument. However, I was also the lead engineer for my area, had done my research, and decided my last option was to stand up and refuse to accept delivery of the equipment.
I was absolutely convinced my stance was going to get me fired but I firmly believed I had an ethical responsibility to push my point. I must admit I was not being prepared for the amount of support and encouragement I received from my managers and coworkers all the way to our regional engineering group. After many spirited meetings over following months, the machines were retrofitted with up-to-date hold-to-run switches. Fast forward to present day and dual channel, control reliable pendants with hold-to-run switches are common on most CNC equipment. The moral of the story is that you never know what the outcome is going to be until you find your voice. Just make sure you have all the data you need to back up your case and solutions to fix the problem you’ve identified.