Designing for sustainability from the beginning can pave the way for a brighter, greener future.
Fast Radius has submitted this post.
Written by: Izzy de la Guardia, Senior Design and Development Engineer, Fast Radius, and Kathleen Bollito, Customer Application Engineer, Fast Radius
Sustainability is the future of business as we know it. Businesses that shift to renewable energy can stabilize their energy prices, access tax credits and increase safety while they go green. Also, research shows that more than two-thirds of millennials will pay more for products and services from companies committed to sustainability. Over time, companies that do not become sustainable will fall behind their more environmentally-conscious competitors.
Industrial activity accounts for 23 percent of all greenhouse gas emissions, so there i’s a lot of room for improvement where sustainable manufacturing is concerned. Designers and engineers have the unique opportunity to incorporate sustainable practices throughout the entire manufacturing process as they bring products to life.
Below, we’ll explore how designing for sustainability from the beginning can pave the way for a brighter, greener future.
Three Design Strategies for Sustainability
Sustainable manufacturing involves manufacturing products using processes that conserve energy and resources, and minimize negative environmental impacts. You can make manufacturing more sustainable by reducing material and improving part lifetime and serviceability.
1. Reducing Material
When it comes to sustainable design, how much material you use is just as important as what material you use. Reducing physical volume can decrease machine time, energy consumption and the environmental impact of raw material extraction for some manufacturing processes. Plus, smaller and lighter parts produce fewer fuel emissions during transport. A 10 percent weight reduction results in a 6-8 percent boost in automobile fuel economy, while a 20 percent reduction improves aircraft fuel efficiency by 10-12 percent.
While you can still lightweight parts using traditional methods, such as adding shelling and including pockets or ribs, you also might consider new lightweighting methods and tools. These techniques allow you to achieve your desired performance while minimizing the material required. As you design your part, consider:
Generative Design:
Generative design uses iterative simulation to remove material from a design space given the loading conditions and target physical properties. It is particularly effective when paired with additive manufacturing due to the higher degree of design freedom additive offers, but a lot of generative design software also includes design constraints for traditional manufacturing processes like milling.
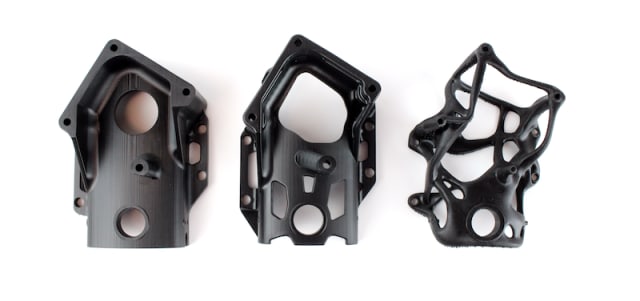
Lattices:
Lattices are repeated unit cells that enable material and weight reduction without sacrificing structural integrity. With the help of a simulation, you can quickly find the right unit cell to produce your desired mechanical response, making lattices an excellent way to reduce weight and material usage without compromising function.
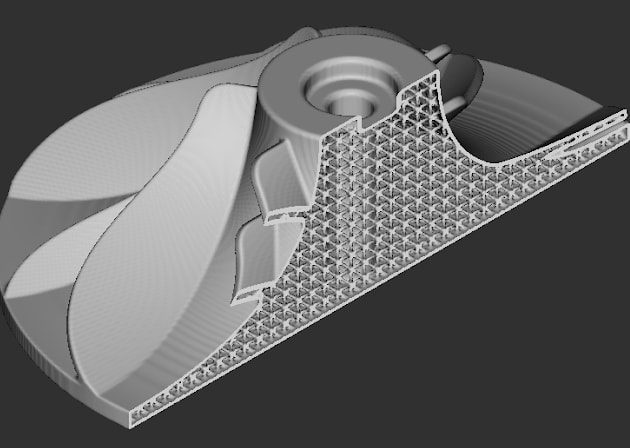
Additive:
Even without generative design principles and lattices, additive manufacturing processes use and waste less material than traditional manufacturing methods such as CNC machining. To make 3D printing even more sustainable, try to eliminate support material wherever possible when using fused deposition modeling (FDM) or stereolithography (SLA) technology. It may seem like an inconsequential amount of material, but it adds up over time.
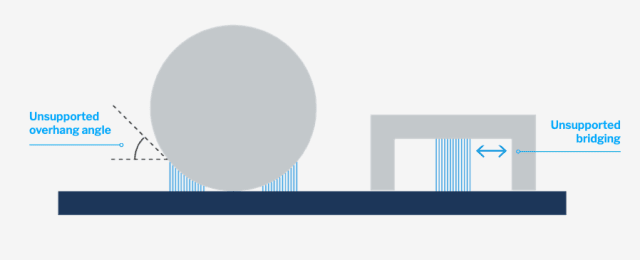
Part consolidation:
Consolidating parts will reduce raw material consumption, manufacturing energy and the environmental impact of shipping sub-components. If you have complex components or geometries, you can consolidate them into a single unit using additive manufacturing, thereby reducing fabrication time, material usage, weight and the amount of fuel needed for transportation.
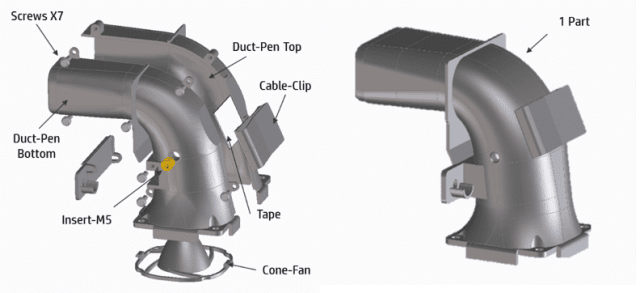
Keep in mind that you will have to balance sustainable design considerations with your part’s other needs. For example, ask yourself whether the material savings of an additively produced generative design outweighs the cost of that complex geometry potentially requiring more support material. You may realize you can achieve similar material reductions without requiring support by using shelling and latticing.
2. Designing for Lifetime
Longer usable life spans mean less waste, so designing durable and easily replaceable parts is critical. Designing for remanufacturing or refurbishment are popular ways to extend product lifetime. Designing for remanufacturing prevents parts from becoming obsolete without sacrificing performance, reduces CO2 emissions, conserves raw materials, and contributes to the circular economy. You can even rebuild remanufactured products to their original specifications with reused or repaired parts to make them last longer.
When a product cannot be reassembled to meet its original specifications, it is considered refurbished. Refurbishing—distributing previously returned products—is cheaper but less thorough than remanufacturing. However, it is still a good option from a sustainability standpoint. Manufacturers can repair defects and test functionality with refurbished products, and a refurbished product will always be more sustainable than a single-use product.
Whether you decide to go the remanufacturing or refurbishing route, you wi’ll need to design serviceable parts. Remember to:
- Simplify your design to reduce the number of failing items needing diagnosing, disassembly and reassembly.
- Standardize parts to reduce your per-cost production cost, simplify your inventory needs, accelerate the replacement process and generate more failure and reliability data to use when service planning.
- Add access panels, hinges or hatches to make servicing difficult-to-reach places easier.
It is also important to note that you need to balance different sustainable design principles. Part consolidation can reduce energy, raw material and fuel consumption, but it also impacts serviceability. When a part stops working, you will need to replace a large part composed of more sub-components instead of a single sub-component, so be sure to weigh your options carefully.
3. Ensuring the Design Process is Sustainable
You can also reduce waste by re-examining how you go about the design process. For example, if you use simulation and virtual assemblies to validate your design before you manufacture it, you can limit the number of prototypes you produce and prevent material-intensive redesigns. Plus, if you use additive manufacturing to create prototypes, you will produce less waste than you would with processes such as CNC machining or injection molding—especially if you print large parts on a smaller scale.
If you do decide to CNC machine a part, take standard stock sizes into consideration while designing to reduce waste material and save energy associated with machine time.
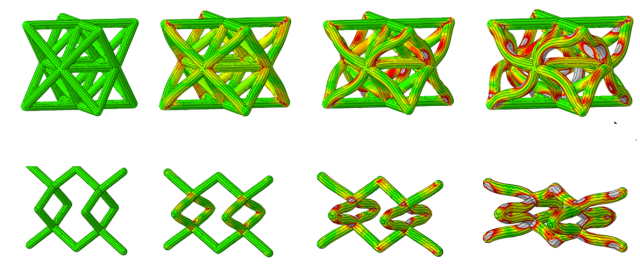
Also, be sure to think about different ways you can make post-processing more sustainable. For example, using texturing and eliminating the need for support material eliminates post-processing requirements, while fabricating a part in its final color eliminates the need for painting. However, if you cannot manufacture a part in your desired color, keep brainstorming other ways to make the process more sustainable, such as sourcing non-toxic environmentally friendly paint that excludes VOCs.
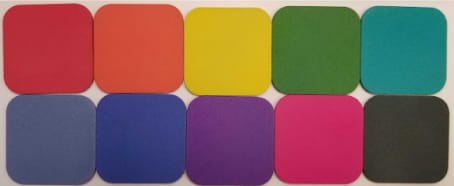
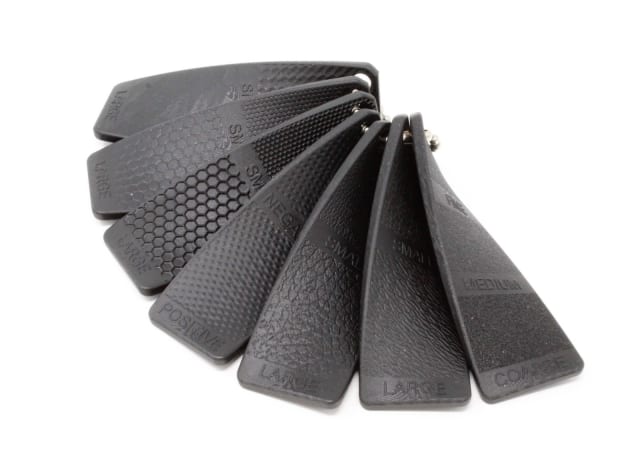
You will also need to go beyond thinking about the part itself and think about how it is produced. For example, in injection molding, a process that requires tooling created via CNC machining, complex geometries such as extrusions, undercuts and cavities require lifters and slides. Every additional feature increases the amount of material and energy needed to create the tool, so simple parts mean lower energy and material consumption. You can work with your manufacturer to modify your design to optimize manufacturing efficiency.
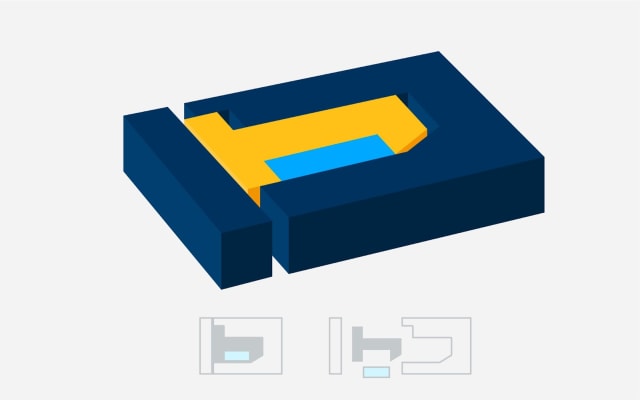
Finally, it is never too early to start thinking about how you are going to transport your parts. Try to design nesting parts or parts that will pack flat to maximize space during shipping.
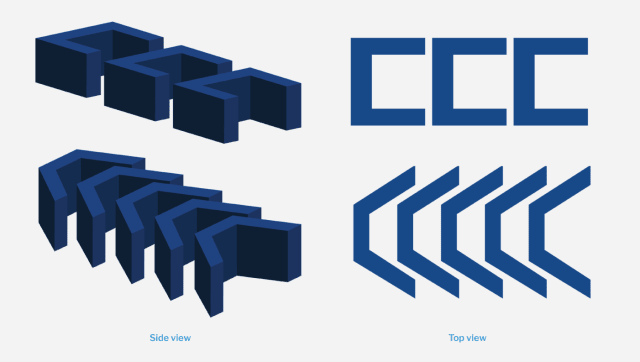
To foster sustainability in the manufacturing industry, you have to start at the source—design. By making thoughtful design choices, seizing opportunities to reduce material and maximizing usable life spans, product teams can do their part to make manufacturing cleaner and greener.
If you need a little help, consider working with an experienced manufacturing partner like Fast Radius.