Number four will surprise engineers who have designed in 3D for decades.
Dassault Systèmes has sponsored this post.
During a virtual round table, engineering.com sat down with three collaborative design software experts:
- Kevin O’Donovan, Technology Evangelist and founder of A Bit of This and That,
- Tim Greenwood, Senior Solution Architect Manager at Dassault Systèmes, and
- Daniel Pyzak, CATIA Mechanical Technical Director at Dassault Systèmes.
Though many topics were discussed (click here to watch), the experts also outlined five innovative workflow benefits of collaborative engineering software. Here is a summary.
1. Cutting Non-Value-Added Tasks
Many engineers will remember a time where they rolled up a rendering, put it into a paper tube, went to the upstairs office and unfurled it onto a desk saying: “Hey, boss. Look at this.” Though engineering software such as CAD and simulation brought this process into the digital world, much of the collaborative process was still manual. You walked between offices, sent emails and transferred files.
“We’re moving into a world where we can remove some of those bottlenecks and the non-value-added tasks of the typical engineer’s day,” says Greenwood. Engineers can define non-value-added tasks as any friction during the process of getting a design reviewed, approved or even looked at.
Pyzak argues that much of this friction has been addressed by cloud features within collaborative engineering software. He said, “The cloud changed completely the way of designing things and collaborating between people.”
The cloud gives engineers access to all the information they need as they need it. And everything is stored in a single source of truth (more on that later). This enables them to work faster, with a lower barrier to entry and a more immersed experience.
He described a scenario where an engineer at any location needs only a phone and internet connection to connect to their company’s database, share data and then revise, alter, annotate or approve 3D models. He adds that these process improvements have made a big difference for many companies. “We have more time to do the real work, invent, innovate and make new things,” Pyzak says. “That’s quite important for me.”
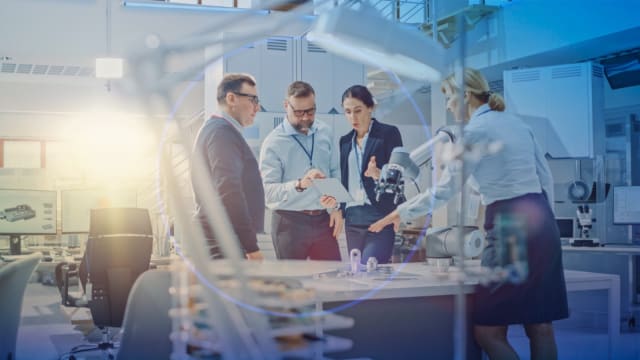
2. Configuration Control Without Chaos or Loosing Good Ideas
As products become more complex, more engineers with varying expertise will need to work together during development. With so many people able to work on designs and contribute, version control becomes critical to the success of solving a problem. If just one of those individuals were to work off an old version, it could cause chaos and dozens of issues down the road. With collaborative engineering software tools, however, everyone is working from a single source of truth.
“That’s the right term, the single source of truth,” says Greenwood. “You’re not moving data around and creating copies of that data. The data lives in the platform. Everyone can reference the right version of it … There are multiple revisions but you’re still referring to that one single source of truth.”
Along the same lines, O’Donovan points out that from version to version it might be hard to see what has changed. You might want to look at an older version to see the difference, but you don’t want to risk the wrong models being treated as the truth. With collaborative engineering software tools, however, O’Donovan notes, “I can see who changed it, why they changed it, it’s all documented.”
A challenge to implementing this strict level of version control is that it forces some organizations to hold back improvements until they reach a critical mass. The idea is to aggregate the changes into a new improved version of the product to reduce confusion and errors from numerous change orders. The problem is that this philosophy can cause good ideas to be put on hold, delayed indefinitely or forgotten.
Greenwood says with collaborative engineering tools, “we can reduce this dramatically and we can manage it. We can apply configuration control to build those changes in at the appropriate time. Make them known by everybody, make them visible and make them available to be adopted by manufacturing at the time that they’re able to adopt them.”
3. Virtual Meetings as Good, or Better, Than In-Person
With a single source of truth and the improved methods of communication mentioned above, it isn’t hard to see how these can drastically improve virtual meetings. Nonetheless, many still think that traveling long distances to meet over blueprints, shoulder-to-shoulder, is the best collaboration engineers can get. But the panel of experts argued that we can do better than, “We all had to jump on a plane,” as O’Donovan put it.
He added that virtual tools can digitize and simplify collaboration during the design process. One obvious reason is that it’s easier to discuss a 3D shape using a mouse and computer screen than a 2D blueprint and red pens. Another benefit is that all the information an engineer might need during the meeting is available on the cloud.
The limitations of physical meetings should also be considered. A room can only fit so many people. So, those in physical meetings tend to be high enough on the food chain that they could make decisions, but low enough that they could comment on the physical designs. However, they weren’t always the people in the thick of things. This could lead to some faults or mistakes entering development or slipping through the cracks.
Greenwood says that now you can invite hundreds of people into a digital meeting room. This helps you get the right people, from various fields and specialties, to look at the designs. “It becomes harder to make the wrong decision,” he says, “as there is always someone there to say, ‘wait a minute, that doesn’t work.’ There are physical boundaries that we have, like the size of a meeting room. When you take away those physical boundaries, we can start to bring the right people into the right places.”
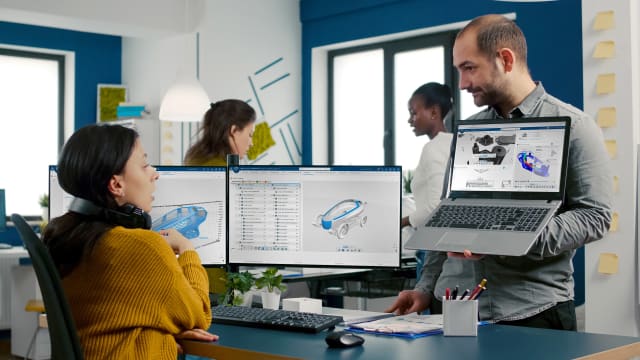
4. Seeing Designs in Person Using AR and VR
Engineers have been viewing designs on computer screens for decades. So, the fact that collaborative engineering software enables people to do this in a virtual meeting is more of an evolution than a revolution. However, that isn’t the only way engineers using these tools can visualize their designs—inside or outside of a meeting context. Collaborative engineering software can also use augmented and virtual reality (AR and VR) to help engineers interact with their 3D designs within a 3D landscape.
Pyzak puts it this way. “The biggest benefit of VR is the scale. You are inside an environment, you know what is two meters [high], you have the scale. In front of a normal screen, you don’t have the scale. And because of this perception of the scale, you can make the right decisions in terms of design.”
Imagine changing the shape of a pipe in a crowded junction within an oil rig. By putting on a VR headset, engineers can see if it’s realistic that a maintenance crew could get to that pipe and fix it. When working on a computer screen, Pyzak argues, that scale can be lost. The experts then suggested taking this process to an extreme. Engineers could go on virtual tours of the whole complex, during the design process and before anything is built. This will give the engineers a sense of what the oil rig will feel like, informing the design process.
“We shouldn’t also forget about augmented reality,” notes Greenwood. “Being able to overlay the virtual model onto the physical parts.” Now imagine the same maintenance crew needs to switch out some pipes for preventative maintenance. Instead of cross-referencing an erosion simulation on a screen, they can use AR goggles to overlay the results onto the real asset and easily see which pipes are due for a change.
O’Donovan notes that in the past, this kind of application of AR and VR would take months to prepare, as a specialist would need to build the VR model from scratch. Within that time, things can change between the VR model and the most up-to-date version of the product. However, with modern collaborative engineering software, you have access to a living virtual twin that can feed results into a VR headset in real time.
5. Better Optimized Products for Costs, Quality, Manufacturability and Sustainability
Perhaps the biggest benefit of collaborative engineering software is its ability to help engineers optimize products according to various criteria. Since everyone is working from the same data, and everyone has instant access to the results of others, engineers can better assess tradeoffs and get to market faster.
“For me it’s all about simulating it virtually before you’ve spent any real money on making it physically,” says Greenwood. “So, when you make it physically you know that it’s going to work … It’s all about trying to do that upfront simulation to make your mistakes. We make mistakes, we’re human, but you make them in the computer, and it doesn’t cost the world anything.”
These simulations and optimizations aren’t limited to the product itself. Manufacturing engineers can simulate the feasibility of constructing various parts and assemblies. Supply chain experts can optimize the logistics of getting all the resources needed to make the product. Environmental engineers can simulate the product’s sustainability or recyclability. Engineering leads can run assessments to ensure everything is still on budget. When these computations are fed into one another, optimization algorithms and artificial intelligence can then be used to whittle down design options until the best versions of the product emerge.
During this part of the discussion, Pyzak spoke about design to cost, and O’Donovan discussed design for manufacturing and virtual commissioning. Greenwood talked about sustainability. He says, “The tools are there now to allow the designer to check the environmental impact of his design and check based on specific rules and databases of information. As he’s doing his design, he can check whether that meets the environmental impact, cost impact and weight impact.”
But O’Donovan summarized this process as business resiliency. “Because you need to be able to deal with supply chain changes, cost of energy, cost of raw materials, substituting things. So absolutely the net-net is an environmental benefit. But today, it’s all about business resiliency. That saves money.”
To learn more about the benefits of collaborative engineering software, watch the full roundtable.