ECM can seriously upgrade a manufacturer’s capability to produce these highly precise and demanding components.
EMAG has sponsored this post.
Gun barrels need to be precise, accurate and reliable, which makes it a challenge to manufacture them in a way that meets the industry’s exacting standards. Electrochemical machining (ECM) is a potential solution for manufacturers to meet—and perhaps exceed—the needs of this growing market.
The global gun barrels market is projected to be worth USD $9.3 billion by 2027—a significant jump from the $6.14 billion it was valued at in 2019—with a compound annual growth rate of 6.15 per cent. Much of this growth will be fueled by increased demand from defense forces and law enforcement agencies to modernize and enhance their capabilities in response to a rise in global unrest, threats of terrorism and cross-border conflicts.
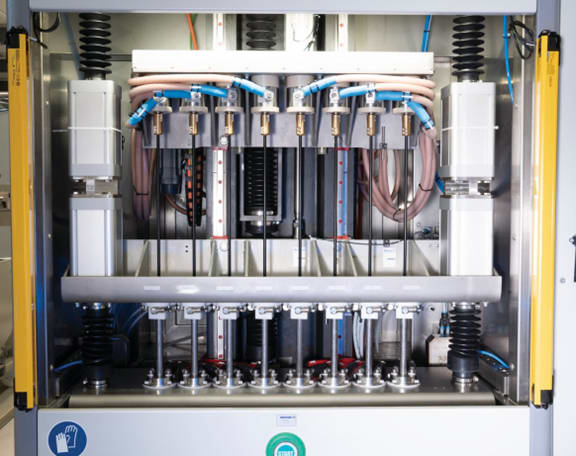
Making A Bullet Spin
Rifling a gun barrel involves etching grooves inside the barrel to make the bullet spin as it is fired. If a bullet does not spin as it flies, it must keep its body exactly in line with its flight path in order to fly straight and fast; if it goes even slightly out of line, it will tumble end over end. If the bullet is spinning, however, forces such as angular momentum keep it flying along its intended path—behaving not as a stationary oblong object, but rather as a spinning top. As a result, the bullet can travel faster, farther and with much greater accuracy than a bullet that does not spin.
Rifling Methods
Currently there are four common ways to rifle the gun barrel: button rifling, single point cut rifling, broach rifling and hammer forging.
EMAG demonstrates its PI 800 ECM platform.
Button rifling is a cold forming process that deploys a carbide tool—the “button”—with grooves in a specific shape and twist rate to swage rifling in the barrel. The grooves are cut in a single pass where the button is moved at a controlled rate through the bore of the barrel blank (the gun barrel before it is grooved). The benefits of this method are that it hardens the surface layer of the barrel, making it more durable, and since no metal is cut there are no chip control issues. However, the process induces stress in the bore of the barrel and requires an additional stress relief operation, increasing cost and time. Button rifling is a closely controlled method, making it easier to repeat with modern equipment in a mass production setting.
Single point cut rifling, or hook rifling, uses a carbide “hook” to cut a single groove in the barrel at a time. It requires multiple passes; the tool cuts a groove, indexes and then cuts the next groove. This method doesn’t place additional stresses on the metal the way a cold forming process does, and manufacturers can exercise precise control over the groove depth per pass. However, cut rifling can be time-consuming and is the most difficult method to achieve repeatability. Cut rifling requires a skilled tradesperson to operate the machine instead of enabling the machine to control the process; in fact, it often requires a custom-built machine with custom tooling provided by the barrel manufacturer.
Broach rifling uses a long tool with multiple teeth that extract small amounts of material out of each groove. The broach is fed down the barrel while rotating, with each progressive tooth making the cut a little bit deeper. The process is similar to single point cut rifling but only requires one pass and can be performed on the same kinds of machines used in button rifling. Like cut rifling, this method does not put additional stress on the material—and can be nearly as fast as button rifling. However, this method requires a different tool for every twist rate, and the tool design prohibits progressive twist; the tools are relatively fragile, adding to the cost and potentially disrupting production if they should fail. In addition, the surface finish is not as smooth as with other methods, and chip control could be an issue. As with cut rifling, a dedicated machine and tool set are required for the process.
The cold hammer forging process pushes an oversized metal tube over a hardened mandrel that has the negative of the grooves ground into its profile. The tube is fed and forged in small sections, resulting in a finished barrel blank with the desired twist and caliber. This method enables increased barrel durability. It also reduces the number of finishing steps required, shortening production time and manufacturing costs. And while it requires a significant initial investment in dedicated machinery and tooling, once the process is set up it is easily repeatable for increased manufacturing.
Electrochemical Machining
A recent development promises to significantly change the way rifle barrels are machined: electrochemical machining (ECM).
As it is a contactless procedure with no heat input, the process is not subject to any of the disadvantages experienced with traditional machining methods, such as tool wear, mechanical stresses, micro-fissures caused by heat transfer or the need for subsequent deburring operations.
The process can be used to polish and rifle the barrels at the same time, as well as to include chamber flutes.
“With this new state to the art of production, operational steps are reduced,” says Manuel Steinhauer, technical sales manager at the EMAG Group. “The workpiece only needs to be clamped once, which reduces the chances for out of tolerance parts. Because of how the process is designed, the outer diameter profile can be finished while the ECM is polishing and rifling the inside of the barrel.”
ECM is used to machine products with the anodic dissolution of metal through the process of electrolysis—including the machining of barrel grooves. An ECM tool is connected as the cathode to a DC voltage source. The workpiece functions as the anode. The two components are exposed to an electric charge within a liquid electrolyte solution that targets specific areas of the workpiece.
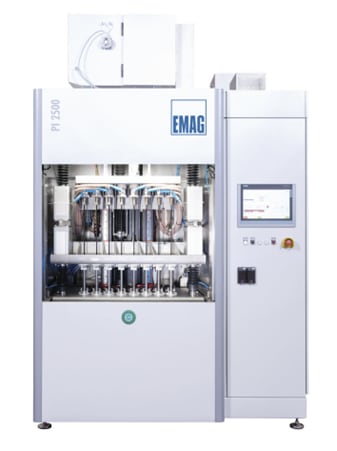
With ECM it is possible to create grooves, contours and other shapes with high precision—but without any contact and without either thermal or mechanical stress. Any material that is removed is precipitated from the electrolyte solution in the form of metal hydroxide.
ECM can be an ideal technology for machining rifle barrels. The narrow and elongated tool cathode can generate the internal geometry of the barrel with high precision. ECM is also safe throughout the process and enables easy cathode exchange and fast component loading.
Steinhauer says one of the biggest advantages is that no stress relief is needed—no stress is applied to the part during production. If parameter changes require a choked barrel, the machine can adjust to produce the required interior dimensions and still produce a consistent and smooth barrel. Hard materials like 416R or stellite (a special Cobalt-chrome alloy) have the same federate as 4140 or 4150 while achieving surface finishes below Ra 4 µ in.”
Unlike button and breach methods, ECM does not create mechanical stresses on the material. It can produce smoother results than broach rifling, and it is faster and requires lower initial investment than the hammering process.
Companies such as EMAG offer a line of specialized ECM machines. In fact, the company uses a special machine solution designed to produce highly precise geometries on short and long barrels alike. A wide variety of geometries and grooves are possible, including standard as well as polygonal and progressive rifling.
“With ECM you will reduce your cost per piece, have more stable production with higher quality and be very flexible in production. The best thing is your barrels will have better accuracy,” says Manuel Steinhauer.
In a highly competitive market, finding a manufacturing method that maximizes efficiency while reducing stresses and tool wear can have a significant difference on a company’s bottom line. Adopting ECM technologies could be a real game changer for gun barrel manufacturers looking to carve out their niche in the market.
To learn more, visit EMAG.