Researchers at Ohio State study ways to protect robots from hackers.
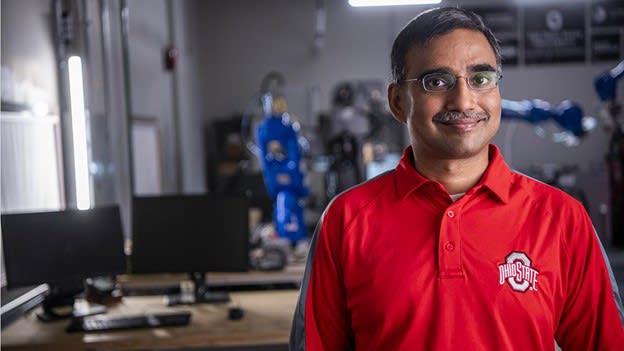
Industrial automation is an essential tool in today’s factories. Manufacturers face staffing challenges which can be eased by automation of key tasks around the shop, and development in the automation industry continues to make robots easier to deploy, integrate and program. However, like any internet-connected piece of technology on the factory floor, automation equipment, including robots, are susceptible to hacking and cyberattack.
Researchers at the Ohio State University Artificially Intelligent Manufacturing Systems (AIMS) lab led by director of cybersecurity Vimal Buck are studying ways to protect industrial automation, specifically industrial robots, from cyberattack.
According to the ISA Global Cybersecurity Alliance, cyberattacks in industry, including manufacturing, increased during the pandemic, as some employees moved to telecommuting instead of working on-site. IBM’s recent X-Force Threat Intelligence Index found that the manufacturing sector was the most attacked by ransomware, accounting for 23% of reports. By locking manufacturers out of their equipment, hackers extract a ransom because of the pressure of downstream supply chain demands. Manufacturers can’t afford to be at risk of cyberattack.
“Cybersecurity with robotics is kind of really scary,” says Adam Exley, a student researcher at the AIMS lab. “If you have a giant robotic arm, if someone compromises it in some way, it can destroy stuff. They weigh thousands of pounds, and they can move insanely quickly. … They can make the robot say it’s somewhere it actually isn’t. They can have it whip around 180 degrees and slap someone in the face, but to the computer system it just looks like it’s just standing there.”
In addition, hackers can target industrial systems with ransomware, locking operators out of system controls and demanding payment. Cyberattacks can also manipulate other internet-connected systems, such as valves, motors, or proprietary data storage. Depending on the target and severity of the attack, industrial cyberattacks can cause harm to your company’s reputation, injury to workers, and massive financial costs.
According to the ISA, major automated manufacturing cybersecurity risks include two main areas:
Cloud and Edge Computing: Because cloud and edge infrastructure is mainly used for data storage, the risk of a breach to these systems is mainly related to intellectual property theft or loss of secret data.
Integrated Technology: Smart devices, such as IoT-connected sensors, allow factories to aggregate data and control production, but also create vulnerable entry points for attack.
“The factories of the future are pretty much all interconnected, and they’re all on the Internet,” says Vimal Buck, senior researcher and director of cybersecurity at Ohio State’s Center for Design and Manufacturing Excellence (CDME).
While manufacturers and automation vendors take great care to use secure networks, redundancy is a fundamental part of any security strategy. The goal of the AIMS lab research is to develop a way for workers to quickly determine whether an issue they’re encountering is normal and easily fixable, or if the cause is more nefarious. That’s why the AIMS team is working on methods to predict the trustworthiness of robotic equipment and identify when it’s behaving abnormally.
The AIMS approach uses cameras and sensors to monitor the equipment, and examines the code that runs the automated systems for signs that something’s wrong. The team is also working with OSU’s department of integrated systems engineering, as well as university penetration testers to search for vulnerabilities.
The ISA advises the following tips to reduce cyberattack risks in manufacturing environments:
Hire the Right Professionals: The World Economic Forum recently discussed in an article how retraining personnel in cybersecurity may be a better strategy for countering attacks compared to hiring, as the world faces a shortage of cybersecurity professionals. According to Buck, as factories are more connected than ever, it’s important for all workers to have familiarity with cybersecurity best practices. “A long time ago, there were safety engineers, and it was somebody’s job to do safety,” Buck says. “And now it’s everybody’s job to do safety. It sort of touches everything. And I think cybersecurity is going to go that way, too.
“It’s not going to be that you need the cybersecurity person at your factory who’s just protecting against hackers. Basically, all the engineering talent is going to have to learn some of the basic skills. That’s where it has to get to. It’s going to impact every aspect of industrial automation and factories.”
Perform a cyber-risk assesment: A risk assessment should consider potential threats and vulnerabilities to guage the likelihood of a successful cyberattack, including assets and threats, allowing countermeasures to be planned.
Create a response strategy: This could include cyberattack insurance, a compliance audit trail, and investments in training. The right policies and procedures can create a culture that reduces the risk of cyber vulnerabilities and safeguard production.