We asked one of America’s biggest EDM users about taking the plunge into Electrical Discharge Machining.
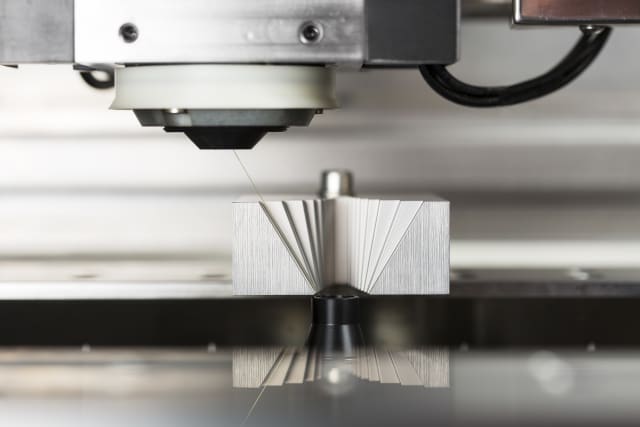
Most manufacturers these days understand that Electrical Discharge Machining (EDM) is a versatile manufacturing process that uses electrical energy to remove material from a workpiece. Compared to just ten years ago, today’s manufacturing professionals are more familiar with EDM and the basic capabilities of the technology. But how are the machines used by experienced pros, and what should manufacturers consider when deciding to run an EDM in their shop?
To answer this question, Engineering.com spoke with Phil Sommer, Director of Operations at Reliable EDM, America’s largest EDM job shop. Reliable EDM operates more than 85 EDM machines, including wire, sinker, and custom-modified machines. Based in Texas, the company specializes in making very large parts up to 10,000 pounds, mostly for the oil and gas industry. When the company was founded, it anticipated the majority of work would be for tool and die. But the use cases for EDM have evolved so much over the past 30 years that, according to Sommer, tool and die jobs contribute a only a small fraction of the business today.
An EDM Primer
Wire EDM: Wire EDM is frequently used for applications similar to broaching, making tight radius inside corners, slots, or operations on hardened alloys that require superior surface finish and no burrs. The machine feeds a wire through the cut while an electrical discharge erodes the workpiece and the wire. The machine chops up waste wire for disposal.
Sinker EDM: A sinker EDM follows the same erosion principle as wire EDM, but the electrode is shaped for the specific task. The eroding sparks occur across the surface of the electrode, which is made of graphite or copper. Sinker EDM creates blind holes and cavities, especially in hardened materials.
Common Use Cases for EDM
The reason Sommer originally planned for tool and die jobs is because EDM is ideal for these applications. Molds and dies are made of hard tool steel alloys, making conventional machining difficult. In addition, they require complex geometry such as deep holes, sharp internal corners, ribs, and deep slots. These features must be machined to precise tolerances. Because EDM is a non-contact machining process, using thousands of sparks between the electrode and the workpiece to erode or “burn away” the workpiece, it can do things conventional machining can’t, such as deep, sub-millimeter diameter holes on curved surfaces, sharp internal corners and extremely intricate shapes.
According to Sommer, Reliable EDM most commonly sees jobs requiring accurate keyways, internal splines, threaded ports and deep holes. However, EDM’s specialized capabilities also bring in more unique jobs. “We’ve bought the biggest machines they make, or modified machines to do big, heavy, complex parts for the oil patch,” explained Sommer, who says Reliable can now machine parts up to 14,000 pounds.
EDM: In-House or Contract?
For a manufacturing company that needs EDM capability, such as a machine shop that has taken on work requiring a keyway operation or other feature that requires EDM, it may be tempting to buy a machine and add the capability in-house. However, there are several factors that should be considered before stepping out to a trade show with your checkbook.
Labor: EDM is a highly specialized trade, requiring expertise and knowledge. In today’s manufacturing labor market, it can be difficult to not only hire the right people to operate a wire or sinker EDM machine, but also to continue to find people to manage employee turnover, even unexpectedly.
Machine Maintenance and Reliability: According to Sommer, EDM machines can be finicky and technical—small problems can shut down a machine. “That’s the advantage of a job shop, where there are more machines,” he explains. “I could have a power surge tomorrow and fry five machines, but I have the resources and personnel to avoid delays.”
Graphite Electrodes: A lesser-known consideration is the challenge of machining graphite electrodes. Graphite can’t be machined on a traditional CNC mill because instead of chips, it creates graphite dust. At Reliable EDM, graphite electrodes are machined in vacuum-sealed, dedicated CNC mills with no coolant system. Graphite is self-lubricating, and the dust is hazardous. “If you mix liquid coolant and graphite dust, you basically get concrete,” said Sommer. “Machining graphite is not easy. If you mill a piece of graphite on one of your regular machines, you will ruin that machine.”
Consistent Work: Will your business do enough work consistently to justify the EDM equipment over the life of the asset? Is it critical to have control over part quality, design iterations and delivery lead times?
Costs: According to Sommer, the largest costs at his company are labor, machinery and consumables, which include the wire as well as electrode materials (graphite and copper).
If your company can manage these challenges, you could potentially make money doing EDM in-house without needing to pay a contract shop a premium to do the work. However, the advantages of contracting out EDM work include reliability, performance and, in some cases, cost.
Reliability: Because job shops own many machines and employ many skilled operators, they can perform more reliably and react to unexpected problems more easily than shops with one machine.
Cost: For obvious reasons, despite the higher cost per part, avoiding the startup and equipment costs of running your own EDM can make contract work more cost-effective at low volumes.
Performance: A professional, experienced job shop can produce better results for challenging EDM jobs, such as tight tolerance work, deep holes or small, intricate operations.
A Final Thought on EDM
Phil Sommer offered this advice to manufacturing professionals considering purchasing an EDM machine: place a high value on support and service from the machine vendor in your evaluation.
“My advice would be to buy a name brand that will give you support—you will need it. If you buy a cheap one, you will be hung out to dry, not able to get parts, and other problems. Then, you’ve got a 250k machine and it’s just sitting there,” said Sommer. Especially in today’s time of supply chain challenges and shortages, his advice rings true. “Every EDM company has some issues, but you want to go with the bigger names for better support.”